2023年07月26日
【在庫管理システム】老朽化したシステムを刷新し、保守部品の在庫管理を最適化!

システム開発会社
業界 | 産業機械装置業界 |
---|---|
会社規模 | 100~299人 |
機能 | 在庫管理 |
システム概要
課題
- 既存システムが業務に合っておらず、余剰在庫が頻繁に発生していた
- 在庫が24時間動き続けるため、正確な在庫数を把握できていなかった
- パソコンへの手入力で入出庫を記録しており、手間やミスが発生していた
- ロット管理をしておらず、棚卸差異の原因究明が困難だった
- 倉庫以外に存在する在庫の所在を把握できていなかった
解決策
- システムの入れ替えに伴い、実際の業務に合った運用方法を確立
- ハンディターミナルとバーコードを活用し、入出庫の記録を簡素化
- 在庫のロット情報・ロケーション情報をシステムで一元管理
効果
- 24時間動き続ける在庫状況をリアルタイムに把握可能に!
- 年間176時間の入力工数とミスを削減!
- 棚卸差異が発生しにくくなり、棚卸工数を年間25時間削減!
- 倉庫以外もロケーション管理することで隠し在庫の発生を防止!
導入の背景
老朽化したシステムの刷新とともに、業務のあり方を見直したい
今回、在庫管理システムを導入いただいたのは、自動車業界向けのシステムを開発・販売している企業様です。また、システムの安定稼動をサポートするために、ソフトウェア・ハードウェアの両面で保守サービスも提供されています。
従来は、20年以上前に自社開発した基幹システムの機能を活用し、さまざまな業務管理を行っていました。しかし、その基幹システムの老朽化が進んだこともあり、2018年頃からシステムの刷新を開始。最終的に、「スマートF」も含めた複数のシステムを組み合わせる形で、基幹システムの刷新が完了しました。
基幹システムの刷新にあたっては、単にシステムを入れ替えるだけでなく、「在庫をより適正な数で管理したい」「当たり前になっている作業品質や効率を改善したい」など、既存の業務のあり方を見直すという目標もありました。

スマートFに決めた理由
自社の要望にマッチした唯一の在庫管理システム
基幹システムを刷新するにあたり、すべての機能を網羅しているシステムはなかなかないことから、機能ごとに最適なシステムを選定することに。そんな中で、保守サービスで使用する保守部品の在庫管理システムとして選定していただいたのが、「スマートF」です。
トータルで7社程度の在庫管理システムを比較した中で「スマートF」を導入した決め手は、”費用対効果が見込めたから”でした。保守部品の在庫管理は、企業によって運用が大きく異なります。そのため、一般的な在庫管理システムでは求めている機能が備わっておらず、自社の要望にマッチしないと感じておられました。
しかし、「スマートF」はハンディ端末による入力機能や、適正な発注量の算出機能など、ほかの在庫管理システムに比べて自社の求める機能を多く備えていたといいます。また、パッケージシステムでありながら柔軟に機能を追加でき、導入費用も抑えられた点が、導入の後押しとなりました。
導入効果
24時間動き続ける在庫状況をリアルタイムに把握!
【導入前】
従来のシステムでは、倉庫から保守部品を持ち出した時点で出庫扱いになってしまい、在庫数が減る仕組みだった。しかし、保守サービスの特性上、持ち出した部品は必ず使われるわけではなく、後で戻ってくるケースも多い。そのため、在庫が足りないと思って発注した後に部品が戻ってきてしまい、余剰在庫が発生するという課題があった。また、24時間体制で保守サービスを提供しているため、在庫が常に動き続けて正確な在庫数を把握できていなかった。
【導入後】
倉庫からの持ち出しを出庫ではなく移動扱いとし、ロケーション管理する仕組みに変更。保守部品を実際に使用したタイミングで出庫することで、在庫状況をリアルタイムかつ正確に把握できるようになった。将来的には、最適な発注点や発注量を自動で計算し、適正在庫数を維持できるように準備を進めている。

ハンディターミナルの導入で年間176時間の入力工数とミスを削減!
【導入前】
保守部品の持ち出し・返却の記録をパソコンへの手入力で実施。特に、部品の持ち出しは年間で3〜4,000件と頻度が高く、かなりの工数がかかっていた。また、入力ミスによって棚卸差異がほぼ100%発生しており、本来は年2回でよい棚卸を毎月実施しなければならなかった。
【導入後】
保守部品の持ち出し・返却の記録をハンディターミナルで実施。バーコードを読み取るだけで素早く記録ができるため、従来の半分の時間で記録が完了し、トータルで年間176時間の工数削減につながった。また、入力ミスの削減によって棚卸差異が発生しにくくなり、棚卸の頻度を2ヶ月に1回に変更できた。
ロット管理・ロケーション管理によって作業品質が向上!
【導入前】
従来は在庫のロット管理をしておらず、棚卸差異が発生したときの原因究明が困難だった。仕入先のメーカーから不良の連絡があった場合にも、いつ・どの顧客向けに使用したのかトレースするのに時間がかかっていた。また、倉庫以外のロケーション管理もできていなかったため、保守サービス車両などに隠れた在庫が多数存在する状況となっていた。
【導入後】
保守部品を1点ずつロット管理する仕組みに変更したのに加え、保守サービスの作業報告書を記録しているCRM/顧客管理システム「SalesForce」との連携により、棚卸差異の原因究明が容易に。差異の原因を作業者に説明し、注意喚起できるようになった。また、保守サービス車両もロケーションの一つとして管理することで、どこに・何が・いくつあるのかが把握可能になった。
お客様の声
自社開発のシステムも含めて複数社を比較する中で、機能要件に対する充足度が高かったことから、「スマートF」を導入することに決めました。他社のシステムがほとんど要件を満たせていなかった中で、ネクスタは「なんでもやります」というスタンスで快く機能追加に応じてくれた点も、選定のポイントとなりました。
実際に導入する過程では、「Salesforce」との連携が思うように動作しないなどさまざまな苦労がありました。しかし、依頼や問い合わせでネクスタの導入支援担当に連絡すると、いつも素早く対応してくれたことが印象に残っています。
「スマートF」の操作に慣れるまでに少し時間もかかりましたが、繰り返し触っていく中で徐々に慣れていき、無事に既存システムからの切り替えを完了することができました。
株式会社ネクスタ:導入支援担当の声
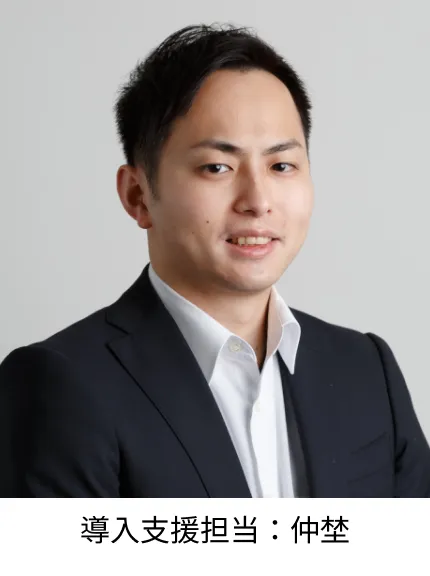
【運用提案する上で心掛けたこと】
導入スケジュールが決まっていたため、事前に外部システムとの連携仕様などを綿密に確認し、スケジュール通りに進行できるように意識しました。また、複数の運用パターンを提示し、作業者の方々がより運用しやすい方法を選択していただけるように心掛けました。
【導入時を振り返って】
外部システムとの連携が多く、動作確認や仕様調整の面でお客様にご負担を掛けてしまう部分も多々ありました。しかし、綿密にコミュニケーションを取った結果、お客様のプロジェクト推進チームと弊社が一体となって本案件を進めることができたと思っています。