過去トラとは?IATF16949規格との関連、記載すべき項目、活用方法を解説
公開日:2024年11月15日
最終更新日:2024年11月18日
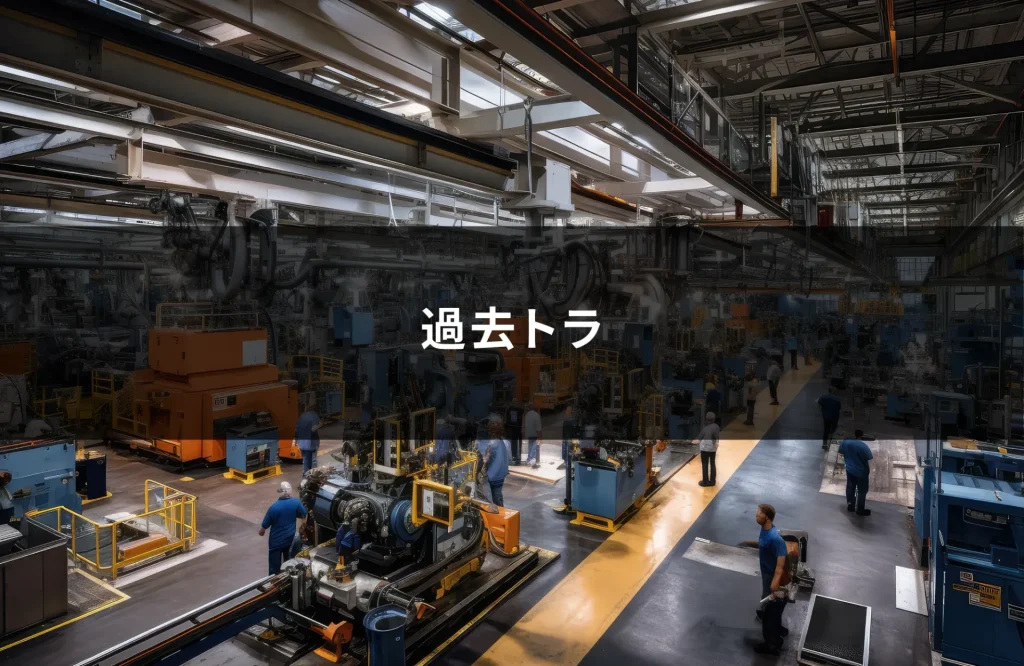
製造業におけるリスク管理や品質向上には、過去のトラブル事例をまとめた「過去トラ」の活用が不可欠です。本記事では、過去トラの概要とその活用方法、さらにISO9001やIATF16949といった国際規格との関連性について解説します。
過去の不具合データを有効に管理・共有し、組織全体で活用することで、同様のトラブルを未然に防止し、プロセス改善や新製品開発に役立てることができます。過去の経験を活かし、製造現場の品質と信頼性を向上させましょう。
過去トラとは
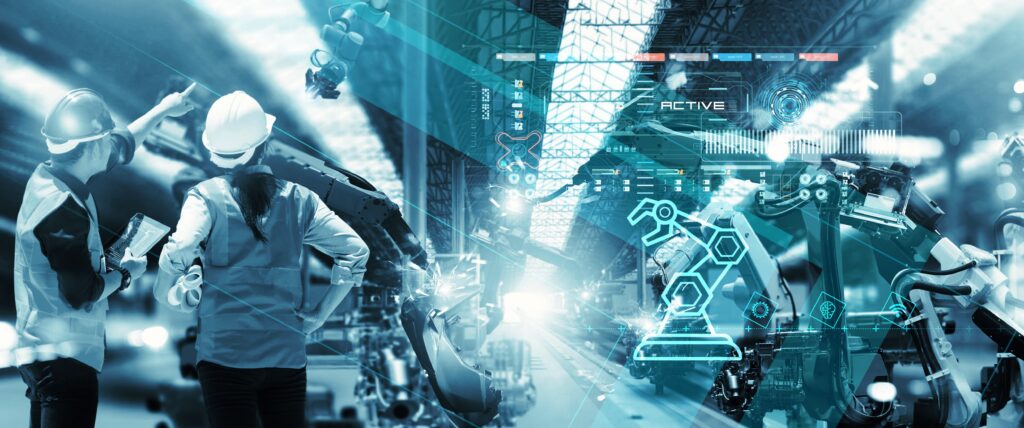
過去トラとは、「過去のトラブル」の略であり、企業や組織が過去に経験した不具合に関する情報を指します。トヨタ生産方式でも活用されている重要なツールです。
過去トラの意味
過去トラは、過去に発生したトラブル・ミス・事故などに関する事例を収集・分析し、活用できる形に纏められた資料やデータベースのことです。
過去トラ情報は、製造業で多く利用されますが、物流業界・卸売業界などを含め、あらゆる業務プロセスにおいて役立ちます。
過去トラに注目する理由
過去トラに注目する最大の理由は、組織として類似トラブルを未然防止するためです。「愚者は経験に学び、賢者は歴史に学ぶ」という言葉にもあるように、組織が経験した過去事例を最大限活用することが、組織風土としての品質向上に繋がります。
また、過去に発生したトラブルの原因と対応策を記録し、組織全体で共有すると、同様の問題が再発するリスクを減らすことができます。同様の問題再発は忘れ去られた頃に発生するケースが多いため、定期教育資料として活用してもよいでしょう。
過去トラ情報を新製品設計やプロセス改善の際に参照することも効果的です。新製品において、類似トラブルが未然防止できるため、製品の信頼性・工程安定性などのリスク低減に繋げることができます。
過去トラに関連する規格
過去トラ情報の管理と活用は、品質マネジメントシステムの規格要求事項で定められています。ISO9001やIATF16949といった規格は、過去のトラブル情報を活用して品質を向上させることを求めています。
ISO9001要求事項との関連性:6.1 リスクおよび機会への取組み
ISO9001は、品質マネジメントシステムに関する国際規格であり、組織が顧客の要求を満たし、持続的に改善を行うことを目的としています。
要求事項6.1『リスクおよび機会への取組み』の中で、望ましくない影響を防止または低減することが求められています。
要求事項7.1.6『組織の知識』からは、失敗から学んだ教訓を組織の知識として維持し、必要な範囲で利用できる情報にしなければならない、と読み取ることができます。
このように、過去の不具合・トラブル事例集を記録し、組織の知識として活用することで、類似の事業・製品・プロセスに関するリスクを減らす取り組みを実施しなければなりません。
IATF16949要求事項との関連性:6.1.2.1 リスク分析
IATF16949は、自動車産業向け品質マネジメントシステムの国際規格であり、次のような要求事項があります。
6.1.2.1 リスク分析
組織は、最低限、次のことをリスク分析に含めなければならない。
a) 製品リコール、製品監査、フィールドからの返品・修理、クレーム、スクラップ、および再処理、から学んだ教訓6.1.2.2 予防措置
IATF 16949:2016 – 公式解釈集
f) 類似プロセスでの再発を防止するために学んだ教訓の活用
つまり、過去トラ情報の管理・活用が、IATF16949規格で求められているということです。特に、自動車産業では製品の安全性や信頼性が厳しく求められるため、過去トラ情報も確認することで、品質の継続的な改善とリスクを確実に減らす必要があります。
他にも、IATF16949では、「不具合モードの文書化」「再発防止策の実施および評価」に関する要求事項が定められています。これにより、過去に発生した不具合やトラブルが組織全体で共有され、品質管理の強化につながることを目的としています。
過去トラを活用するメリット
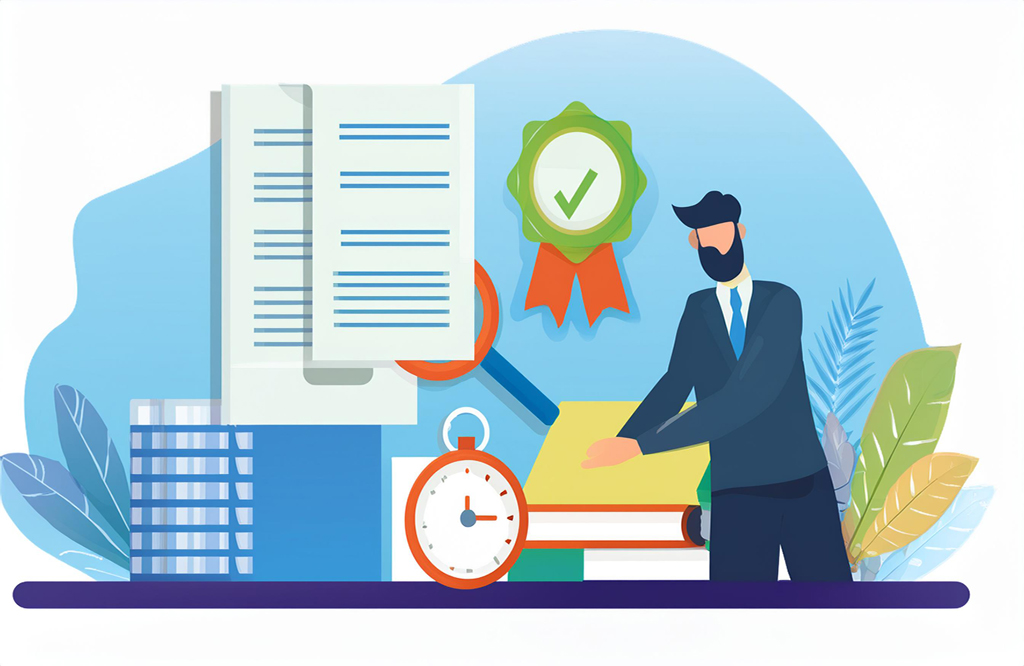
過去トラ情報の活用により、組織内の歴史を参照しながら設計・開発・工程改善に取り組むことができます。その結果、工程不良や品質不良の再発防止、設計コストの削減など、多くのメリットがあります。
知識の共有
過去トラ情報を組織内で共有することで、個々の経験や知識を組織全体の資産として活用できます。これにより、過去トラ情報に類似する問題の未然防止策を反映した設計・改善が立案され、組織として効率的に業務を遂行できるようになります。
過去トラ情報をデータベース化し、検索しやすい形で管理することで、必要な情報に素早くアクセスできることも重要です。さらに、製品設計や工程変更などのデザインレビューにおいて、過去トラ情報から類似事例の確認を求める規定を制定・運用することも、組織の知識を活用するうえで非常に有効です。
工程トラブルの未然防止
過去トラ情報の活用は、工程不良の未然防止に役立ちます。過去に発生した工程不良の原因や対策を記録し、類似の工程でも問題が発生しないように設計・維持管理することで、新しいプロセスでの工程トラブル発生リスクが低減できます。
また、工程改善を意図した変更であっても、過去トラを踏まえた改善が必要です。このため、QCサークル活動などの参考資料としても効果的です。
品質不良の予防処置
過去トラ情報の適切な参照・分析により、新製品における品質不良発生を防ぎます。製品設計・工程設計の過程で、過去に発生した類似製品の品質不良を確認し、その再発防止策を取り入れることで、新製品の品質不良発生の大幅な抑制に繋がります。
また、過去トラ情報を活用して、類似の品質不良の兆候を早期に見つけるための監視体制の構築も可能です。
このように、過去トラ情報を設計段階から活用すると、設計ミスや後工程での手戻り、試作・量産試作における検証事項を減らすことも可能です。結果的に、製品の設計から製造段階に至るまで、トータルコストの削減が可能になります。
過去トラ情報のフォーマットに必要な記載項目
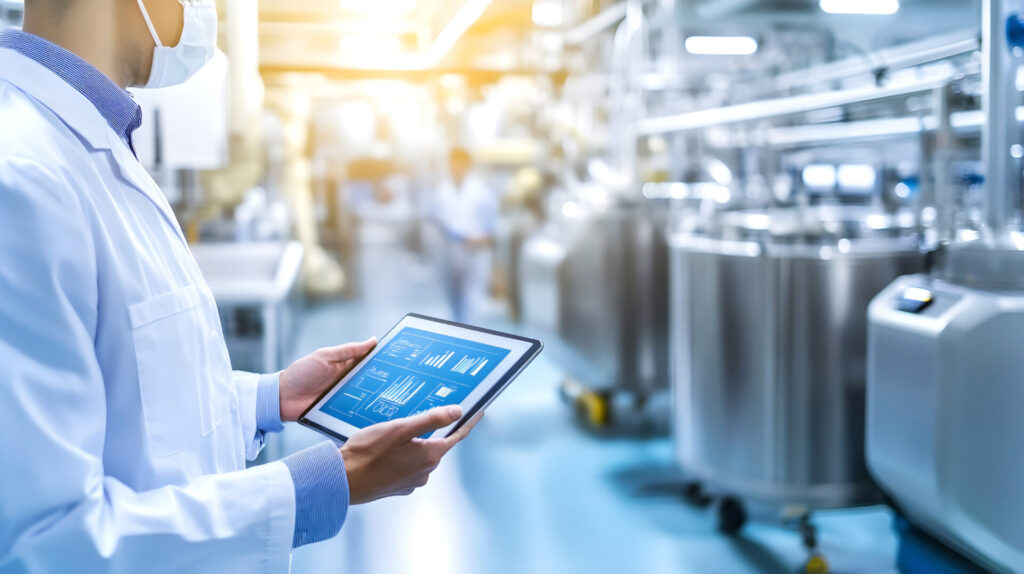
過去トラ情報を有効に管理・活用するためには、適切な記載項目を設定して、対応する情報を記録することが重要です。
発生日付
過去トラ情報には、トラブルが発生した日付を記載します。再発防止策を講じた後、発生日時をもとに効果を追跡することで、同様のトラブルが再発していないかを確認できます。
また、トラブルの発生日時を集約すると、温度・湿度などの季節的要因、天候による設備・材料への影響を考慮した分析が可能となります。
担当者・関係者
トラブル対応の責任者や、問題解決に関わった担当者・関係者の名前も記載すると、数年後に情報を参照した際であっても、必要な問い合わせを迅速に行うことができます。また、情報の共有や引継ぎにも役立ちます。
タイトル
過去トラ情報のタイトルは、トラブルの内容を簡潔に表現したものにします。これにより、データベース内で情報を検索する際に、簡単に目的の情報を見つけることができます。タイトルには、トラブルの概要や主な原因を示すキーワードを含めて、簡潔に記載するとよいでしょう。
概要
トラブルの概要には、次の3点の情報を簡潔に記載します。
- 発生した問題の状況
- 問題の影響範囲、
- トラブル発生メカニズム
これにより、データベースなどにある多数の過去トラ情報の中から、どのようなトラブルが発生したのかを検索しやすくしたり、適切に抽出しやすくしたりします。
本文
本文には、トラブルの詳細な内容、原因分析と推定メカニズムの詳細、対策の実施内容とその効果を記載します。詳細な情報を含めておくと、類似の問題が想定される場合に、適切な予防策を講じることができます。
写真や図
必要に応じて、トラブルの状況を示す写真や図を添付しておくと、トラブルを経験していない人であっても内容を理解しやすくなります。
まとめ
最後に、トラブルの要約や、今後の対策に対するアドバイスを記載します。まとめでは、再発防止のための教訓や、組織全体で共有すべきポイントを明確にすることが重要です。
過去トラ情報の活用方法
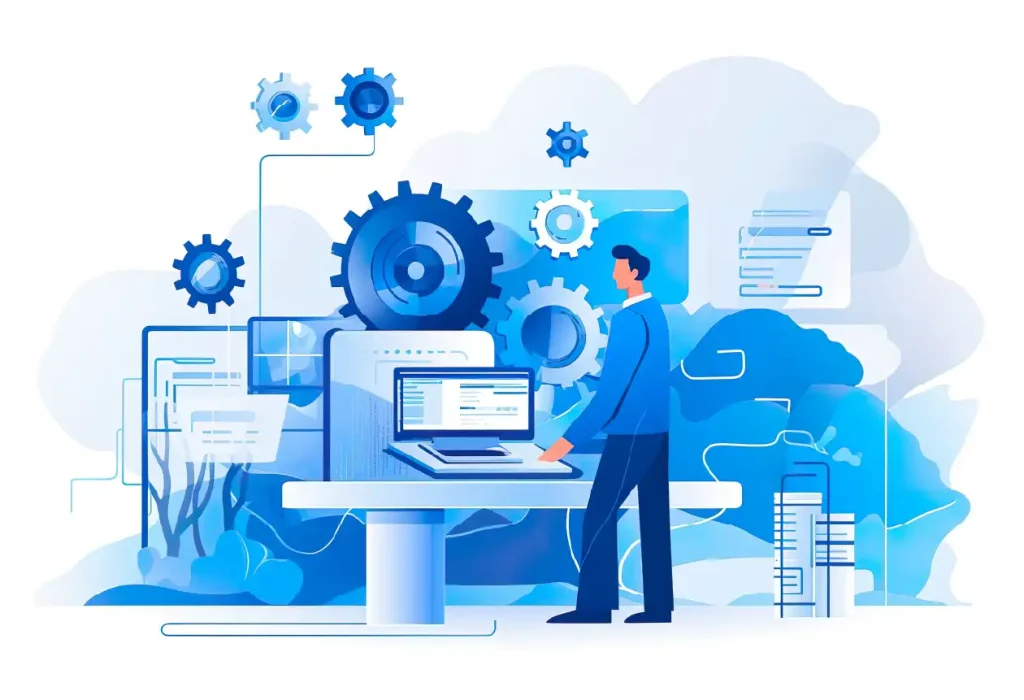
過去トラ情報を効果的に活用するためには、組織全体で共有し、継続的に利用する仕組みを構築することが重要です。
組織内でのデータベース化が大前提
過去トラ情報をデータベース化し、全社的に共有することで、情報へのアクセスしやすくします。情報が蓄積されていたとしても、全従業員がアクセスできなければ十分に活用できません。また、トラブルが生じた際には、全ての過去トラをデータベースへ入力できる仕組みも欠かせません。
また、データベースは、容易に検索・参照できる形式にし、適切な項目で内容が記載されている必要があります。これにより、情報の抜け漏れを防止できます。
定期教育による風化防止
過去トラ情報を社員教育の一環として定期的に使用すると、情報の風化を防ぎ、トラブルに関する情報を改めて認識させることができます。特に新入社員や他社・他部門からの異動者に対して、過去トラ情報をもとにした教育を行えば、熟練の担当者と同じ目線で業務に取り組めるようになります。
FTAとの組み合わせたリスク評価
FTA(故障の木解析)を用いたリスク評価に、過去トラ情報を組み合わせることで、より精度の高いリスク評価が可能となります。過去のトラブル事例をもとに、潜在的なリスク要因を洗い出し、適切な対策を行えるようになります。
FMEAを通した製品設計・プロセスへ反映
FMEA(故障モード影響解析)に過去トラ情報を活用することで、製品設計やプロセス設計における潜在的な不具合を事前に予測し、対策を立てやすくなります。記載されている過去の組織内における経験をもとに、リスクの高い部分を特定し、設計段階から問題発生を防止することが重要です。
22種類の生産管理システムをランキングで比較
初期費用相場や選び方のポイントをチェック
生産管理システムをそれぞれの特徴や初期費用相場などで比較したい場合は、「生産管理システムランキング」も是非ご覧ください。生産管理システムは、自社の製品・生産方式・企業規模などに適したものを導入しないと、得られるメリットが限定されてしまいます。事前適合性チェックや生産管理システムを選ぶ前に押さえておきたいポイントも解説していますので、製品選びの参考にしてみてください。