バッチ生産とは?ロット生産との違い、具体的なメリット・デメリットを解説
公開日:2024年11月27日
最終更新日:2024年11月27日
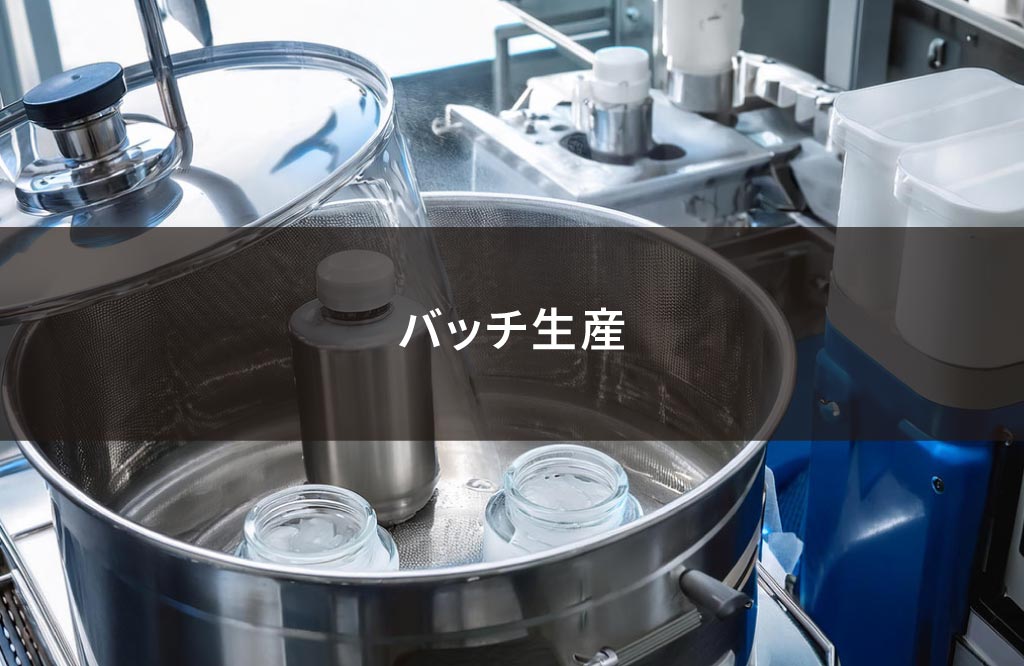
多品種少量生産に最適な「バッチ生産」は、製造工程ごとに一定量で区切り、独立した品質管理を可能にする方式です。厳格な品質管理が必要な医薬品・化粧品業界で多く採用され、柔軟に生産数量や生産品種を調整しやすいという特徴も備えています。この記事では、バッチ生産の基礎概念からロット生産や他の生産方式との関連、さらに効果的な生産管理システムの導入事例までを解説します。
バッチ生産とは何か
バッチ生産は、製造工程ごとに一定量で完全に区切り、まとめて生産する方法です。これにより、同じ設備・製造工程で異なる製品をフレキシブルに生産でき、一定量単位で工程ごとに独立した品質管理ができます。一方で、1回の生産ごとに段取り替えが必要となるため、生産効率やコスト、管理の複雑さが課題となる場合もあります。医薬品、化学品、化粧品など、厳格な品質管理が欠かせない業界で多く採用され、製品ごとに異なる処方や成分を扱う多品種少量生産に適しています。
バッチとは
「バッチ」とは、同じタイミング・条件で製造工程を完了した製品群を指します。この「バッチ」単位での生産により、各工程でのバッチごとに品質検査を実施可能です。品質検査やその他で不具合があれば、そのバッチ全体を廃棄したり手直ししたりします。また、万一異常品が流出してしまった場合でも、それがどのバッチに属する製品であるかが容易に追跡(トレース)できます。
ロット生産との違い
ロット生産は、バッチ生産を含む広い概念であり、製造工程を明確に区切るかどうかに関係なく、一定量ごとに製品をまとめて生産・管理する方式です。ロット生産では、生産期間や個数、製造バッチなど、あらかじめ定めた単位ごとに製品を管理します。そのため、ロットの定義を組織内で明確に決めておくことが重要です。例えば、「1ロット=その日に処理した製品」と定義し、1日に4バッチの生産を行う場合、1ロットは4バッチ分の生産物から構成されます。
他の生産方式との関連
バッチ生産は、少量多品種生産に適した方式であり、特に製品バリエーションが限定的な場合に向いています。一方で、他の生産方式にもそれぞれ特徴があり、目的や製品の特性に応じて選択されます。以下は、主要な生産方式の概要とバッチ生産との関連です。
ライン生産
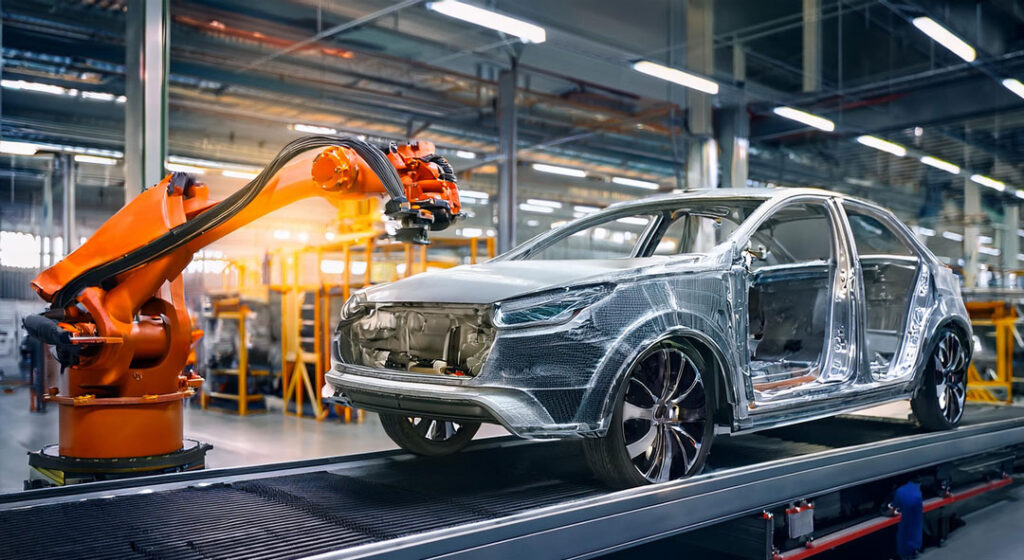
ライン生産は、工程を流れ作業形式で配置し、生産を効率化する方式です。一つの生産ライン上で全ての工程が順に進む点が特徴で、各工程に役割を分担することで生産性を高めやすく、大量生産に適しています。特に組立産業で広く採用されています。一方、バッチ生産は各工程を独立して運用する方式であり、ライン生産とは全く異なるアプローチです。ライン生産が効率的な連続作業を目指すのに対し、バッチ生産は生産面での柔軟性や品質管理の厳格さを重視した方式です。
連続生産
連続生産は、常時稼働している設備を使用した生産方式で、製鉄所など稼働の一時停止が難しいプロセス産業での採用事例が多くなっています。この方式は、バッチ生産のように生産単位ごとに稼働を中断する必要がありません。このため、大量生産が求められる製品や安定した需要が見込まれる製品の製造に適した方法とされています。
個別生産
個別生産は、一品ずつカスタマイズされた製品を製造する方式です。顧客の特定の要求に基づいて製品を設計・製造するため、製品の品質や仕様を細かく管理することが求められます。例えば、産業用の特注部品や機械設備に適用されることが多く、受注ごとに異なるプロセスで製造することが多いです。
バッチ生産のメリット
バッチ生産は多品種少量生産に適していることが主なメリットですが、それ以外にも複数の利点があります。
多品種少量生産に有効
バッチ生産の最大の特徴は、多品種少量生産に対応できる点です。特に、顧客の需要が変動しやすく、多様な製品ラインナップを求められる業界では、小回りの利きやすい生産方式が大きな強みとなります。例えば、化粧品業界では、季節ごとの新商品や限られた期間での販売が頻繁に行われるため、バッチ生産はこれに対応するための理想的な方式です。製品ごとに処方や成分が異なる場合でも、装置内の簡単な段取り替えをすれば、同じ設備を活用して狙いの数量を生産しやすいためです。ただし、このメリットを最大限活用するためには、設備導入時のバッチサイズ設計に依存する点に留意が必要です。
厳格な品質管理がしやすい
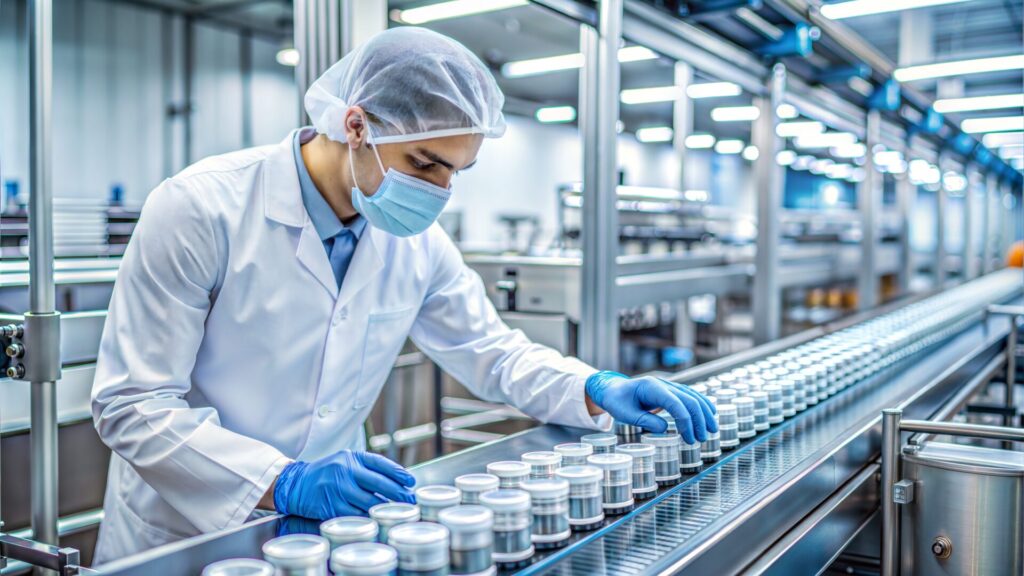
バッチ生産では、生産設備内に投入される原材料や処理物の品質を管理しやすい点が大きな特徴です。特に、GMPに基づいた厳格な管理体制が求められる医薬品や化粧品の製造において、この特性は大きな利点といえます。具体的には、液体や粉体の化学薬品では、バッチを攪拌した後、複数箇所からサンプリングして品質検査で確認することで、均一性を確保しやすくなります。製品を装置内で静置して熱処理する工程では、あらかじめ静置場所を定めて装置内ばらつきを把握することで、製品の品質を担保可能です。
生産数量を柔軟に変更できる
生産設備が小バッチ生産向きの構成である場合には、生産量を細かく調整しやすいため、製品の需要に応じて柔軟に生産計画を立案できます。大バッチ生産に適した設備であっても、バッチサイズの上下限について予め技術検証を実施することで、品質均一性を担保したまま生産量を調整可能です。
バッチ生産のデメリット
一方で、バッチ生産には無視できないデメリットも存在します。以下に述べるデメリットを踏まえ、バッチ生産を活用することが望ましいでしょう。
バッチサイズの変更が難しい
バッチ生産では、設備設計で適切なバッチサイズが概ね決まるため、既存設備では大幅なバッチサイズの変更が難しいのが実情です。極端な例ですが、100kg処理で設計された粉体混合装置に対して、10kgで適切に混合するのは設備構造上難しいケースが多いです。このため、設備設計の段階で設備での製造製品の種類・数量を考慮し、需要変動も考慮した適切なバッチサイズで設備導入することが必要です。
リードタイムが長くなりやすい
バッチ生産は、比較的少量の生産を繰り返す方式であること、同一設備で製造する他製品との生産計画調整が必要であることから、リードタイムが長くなる傾向があります。各バッチの切り替えごとに装置の稼働停止時間が発生するため、生産性向上にも限度があります。生産品種の切り替え時には、装置条件の設定や清掃などの段取り替えも必要です。また、各バッチの品質検査を確認してから次工程に進むことが多く、需要急増に対する迅速な対応は困難です。
生産管理が複雑
バッチ生産では、製品ごとに製造条件が異なることも多く、生産管理が非常に複雑です。製品ごとの設備占有時間、品種切り替えに伴う段取り替えについて、精度の高い情報をもとに計画を組むことが求められます。例えば、医薬品製造では、異なる成分や処方に合わせて操業条件を変更する必要があり、各バッチごとに正確な製品・工程の管理が必須です。僅かな管理不足であっても、重大な品質トラブルや生産遅延に繋がるリスクがあります。
誤投入などのミスが起きるとロットアウトとなる
バッチ生産では、一度のミスがバッチ全体に影響を及ぼします。例えば、原料を誤投入したり操業条件設定を誤ったりした場合、そのバッチ全体が不良品となり、全量廃棄せざるを得なくなります。これがロットアウトと呼ばれる現象で、特に医薬品や一部の化学品のように高価な原料を使用する場合には、大きな損失となります。厳格な管理体制とチェックプロセスが必要不可欠です。
原料の誤投入防止に役立つ生産管理システムとは
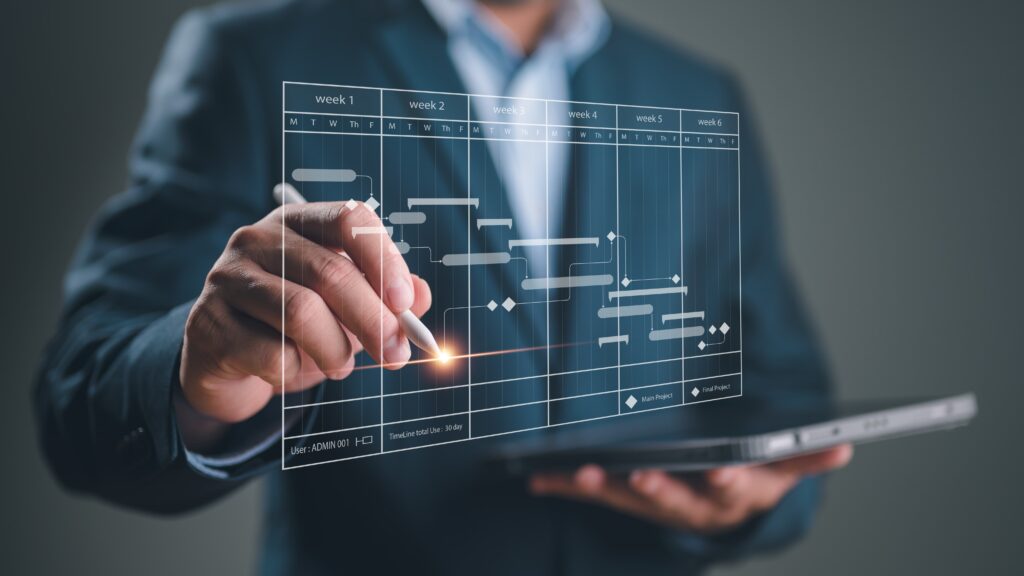
バッチ生産におけるミスを防ぐために、近年では高度な生産管理システムの導入が進んでいます。特に、原料の誤投入を防止するにはシステム管理が有効であり、品質の維持とコスト削減に大きく寄与します。
バーコード管理による人為的ミス解消
生産管理システムとIoT機器を連携すると、ヒューマンエラーを防ぎ、誤投入のリスクを大幅に減らすことが期待できます。導入しやすい一例は、ハンディ端末によるQRコード管理やバーコード管理です。QRコードやバーコードの管理では、原料コードを工程投入前にスキャンし、指示内容と作業内容をシステム上で照合する、などの処置が可能です。これにより、誤った原料が読み込まれた際にアラームを発報させ、誤投入によるロットアウトを未然防止します。このように、生産管理システムとバーコード管理を組み合わせることで、人的ミスを防ぐことが可能です。
→バーコード管理により、属人化を解消し、人的ミスを激減した事例はこちら
原料管理の見える化
生産管理システムは、原料の在庫状況や使用履歴をリアルタイムで把握できるため、管理の「見える化」が実現します。これにより、原料の欠品や過剰在庫のリスクを減らし、ロット生産で求められる複雑かつ効率的な生産計画を立てられるようになります。また、各バッチの製造履歴がシステム上に記録されるため、トレーサビリティが確保され、問題が発生した際にも正確なデータに基づいて迅速対応が可能です。さらに、化粧品や医薬品業界の原料管理において重要な「期限管理」も、生産管理システムで手間なく正確に管理可能となります。システムやハンディ端末上で原料の期限を見える化できるため、先入先出の徹底や期限切れ原料の誤使用防止に役立ちます。
→原料の見える化を達成し、誤使用・誤投入0件を達成した事例はこちら
22種類の生産管理システムをランキングで比較
初期費用相場や選び方のポイントをチェック
生産管理システムをそれぞれの特徴や初期費用相場などで比較したい場合は、「生産管理システムランキング」も是非ご覧ください。生産管理システムは、自社の製品・生産方式・企業規模などに適したものを導入しないと、得られるメリットが限定されてしまいます。事前適合性チェックや生産管理システムを選ぶ前に押さえておきたいポイントも解説していますので、製品選びの参考にしてみてください。