トヨタ方式から学ぶ「7つのムダ」をなくす方法 本当に効率的な現場改善とは?
公開日:2024年06月27日
最終更新日:2024年09月26日
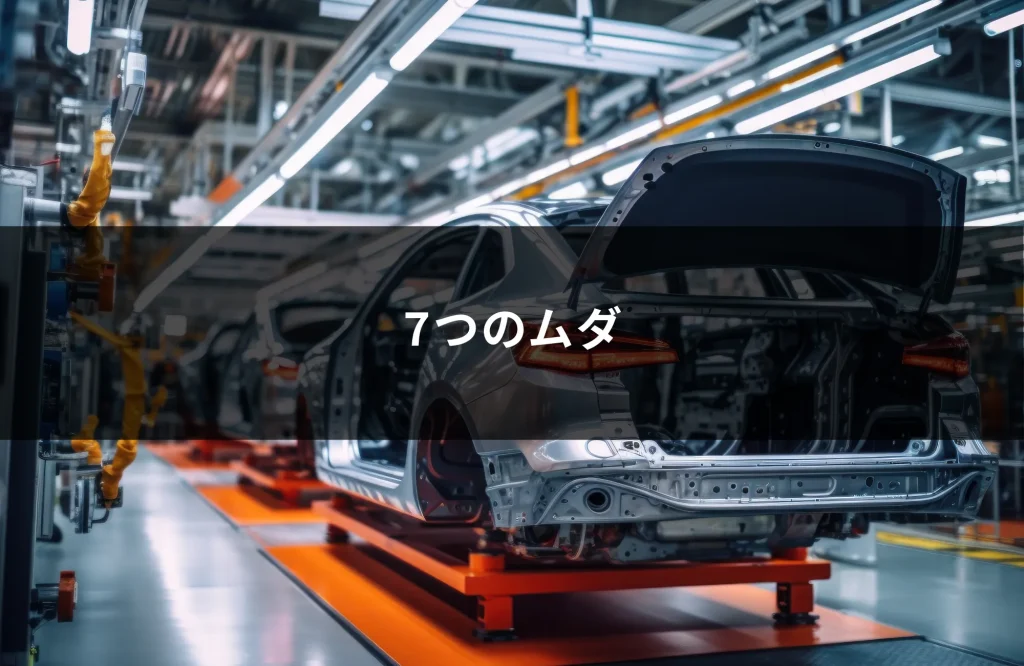
製造現場での効率化においては「7つのムダ」を理解し、それらを可能な限りなくすことが重要です。本記事では、7つのムダの考え方の根底となるトヨタ生産方式を中心に、ジャスト・イン・タイム(JIT)や自働化などの手法、「7つのムダ」の具体的な内容と対策について紹介します。また、生産管理システムの導入による効果についても解説します。
7つのムダをなくす:トヨタ生産方式とは
7つのムダは、トヨタ生産方式(TPS)を実現する4つの手法のうちの一つです。トヨタ生産方式とは、トヨタ自動車が開発した効率的な生産管理を目指す手法で、生産工程におけるムダを特定し、徹底的に排除するという思想でシステム化された生産方式です。
TPSの基本原則には、ムダを最小限に抑えるための継続的改善と、効率的な生産を実現するための作業の標準化が含まれ、これにより、品質向上とコスト削減が実現します。トヨタ生産方式は世界中の製造業に影響を与え、効率的な生産と高品質な製品の提供を可能にしました。
トヨタ生産方式の基本思想は「ジャスト・イン・タイム(JIT)」と「自働化」という2本柱で成り立っています。
JITとは
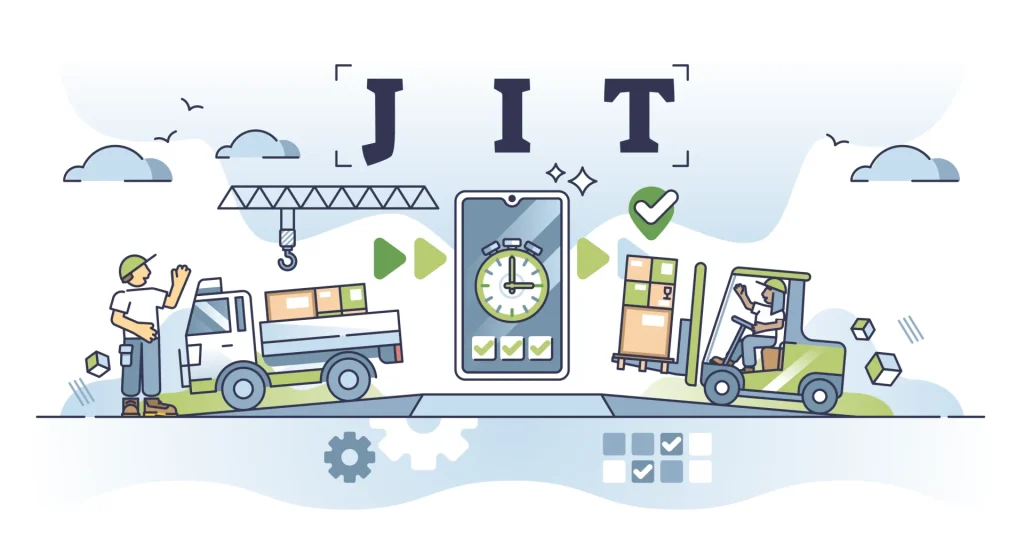
ジャスト・イン・タイム(JIT)は、必要なものを、必要なときに、必要な量だけ生産する手法です。これにより、在庫コストの削減とムダの排除が可能となります。JITはTPSの中心的な要素であり、サプライチェーン全体の効率化に繋がります。JITを実践することで、トヨタ自動車は在庫の最小化を実現し、資金効率を改善しています。さらに、サプライヤーとの連携強化により、顧客のニーズへの迅速な対応が可能になりました。
自働化とは
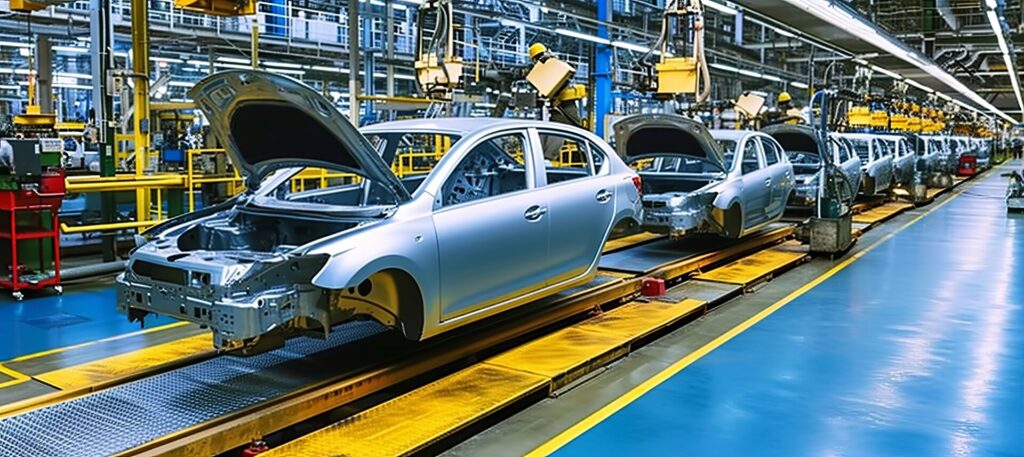
自働化(じどうか)とは、機械が異常を自動で検知し、生産を停止する仕組みです。これにより、不良品の発生を防ぎ、生産ラインの品質を維持することができます。また、人による監視が不要となるため、労働力の削減と生産効率の向上に繋がります。自働化の導入により、トヨタ自動車は生産ラインの安定性を高め、高品質な製品を効率的に生産することが可能になりました。
7つのムダの内容
「7つのムダ」とは、以下7種類の付加価値を産まない業務を指します。
- 加工
- 在庫
- 造り過ぎ
- 手待ち
- 動作
- 運搬
- 不良
- 手直し
これらのムダをなくすことで、製造過程の効率が大幅に向上し、コスト削減が可能になります。製造業において「ムダ」とは、生産過程における非効率な要素を指します。
加工のムダ
加工のムダは、製品を製造する過程で発生する不要な加工や過剰な作業を指します。必要以上の品質や機能を追求することにより、時間とコストが無駄になります。これを避けるためには、適切な標準作業を設定することが重要です。
在庫のムダ
在庫のムダは、必要以上の在庫を抱えることにより、保管コストや管理コストが増加することを指します。JITを活用し、必要な時に必要な量だけを調達することで、在庫のムダを最小限に抑えることができます。
さらに、定期的に棚卸しを行い、在庫の現状を把握することで、在庫管理の精度を高めることができます。
造り過ぎのムダ
造り過ぎのムダは、需要以上に生産することで在庫が増え、保管スペースや無駄なコストが発生することを指します。過剰な生産は、製品の劣化や陳腐化のリスクを伴い、最終的には廃棄コスト(死蔵品)の増加につながります。精度の高い需要予測によって、造り過ぎのムダを回避することができます。
また、生産ラインの柔軟性を高めることで、需要の変動に迅速に対応できる体制を整えることも重要です。
手待ちのムダ
手待ちのムダは、作業員や設備が次の工程を待つ無駄な時間を指し、生産効率低下の要因となります。作業工程を細かく分析し、ボトルネックとなる工程を特定し効率化を行うことで、手待ちのムダを削減することが可能です。また、設備のメンテナンスを適切に行い、故障による手待ちを防ぐことも重要です。
動作のムダ
動作のムダは、作業員の不要な動きや非効率な作業手順から生じる無駄です。工具や部品配置の見直しや、作業手順の標準化など、作業環境や手順を改善し、動作のムダを最小限に抑えることが重要です。動作のムダを無くすことで生産効率を向上できます。
運搬のムダ
運搬のムダは、材料や製品の不要な移動や運搬作業から発生する無駄です。運搬のムダは時間と労力を浪費し、生産効率を低下させます。材料や製品の流れを最適化するために、工場内のレイアウトを見直し、運搬距離を短縮することで、これらの無駄を削減できます。また、運搬用の設備やツールを適切に配置し、運搬時間を短縮することも重要です。
不良、手直しのムダ
不良や手直しのムダは、製品の品質不良により発生する無駄です。不良品の発生は、手直し作業や廃棄コストを増加させるだけでなく、顧客の信頼を損ない、訴訟が発生するリスクもあります。品質管理を徹底し、不良品を発生させないことが重要です。品質管理の強化と適切な設備のメンテナンスを行い、不良品の発生を未然に防ぐことや、従業員の教育や訓練を通じて、品質意識を高めることが求められます。
7つのムダをなくす手順
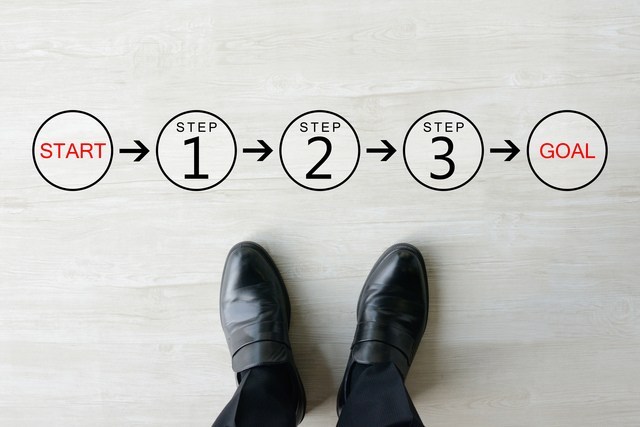
7つのムダをなくすためには、現場の観察から、原因の特定、改善策の検討、実行、そして効果の検証といったプロセスが必要です。
現場を徹底的に観察し、ムダを見つける
まず、現場を徹底的に観察し、どのようなムダが存在するかを見つけ出します。実際の作業状況や流れを詳しくチェックすることで、データだけでは見えないムダも明らかになります。作業員とのコミュニケーションを密にし、現場の意見や観察結果を共有することが重要です。
ムダの原因を見つける
次に、見つけたムダの原因を特定します。ムダが発生する背景には、作業手順や設備の問題などがあるため、それらを詳細に分析し、根本的な原因を明らかにします。その際、データを活用し、客観的な視点から問題を特定することが重要です。
改善策を検討する
原因が特定されたら、それを解消するための改善策を検討します。複数の解決策を比較し、最も効果的で実現可能な方法を選びます。
例えば、設備の更新や作業手順の変更、作業員の教育訓練など、具体的な改善策をリストアップし、それぞれのメリットとデメリットを検討します。改善策の検討には、現場の意見を取り入れ、実行可能な方法を立てることが重要です。
改善策を実行する
改善策がまとまったら、それらを実行します。その際、現場の作業員とのコミュニケーションを大切にし、協力して進めることが重要です。また、スケジュール管理や人手などのリソースの確保も必要です。定期的な進捗確認と調整を行い、問題が発生した場合は迅速に対応することが重要です。
改善効果を検証し、継続的に改善を行う
最後に、実行した改善策の効果を検証します。改善した結果をデータで確認し、必要に応じてさらに改良を加えます。その際、具体的な指標を設定し、数値で評価することが重要です。また、良い結果が得られれば他の現場にも横展開を行うことで、改善効果を高めていくことができます。
7つのムダなくすポイント
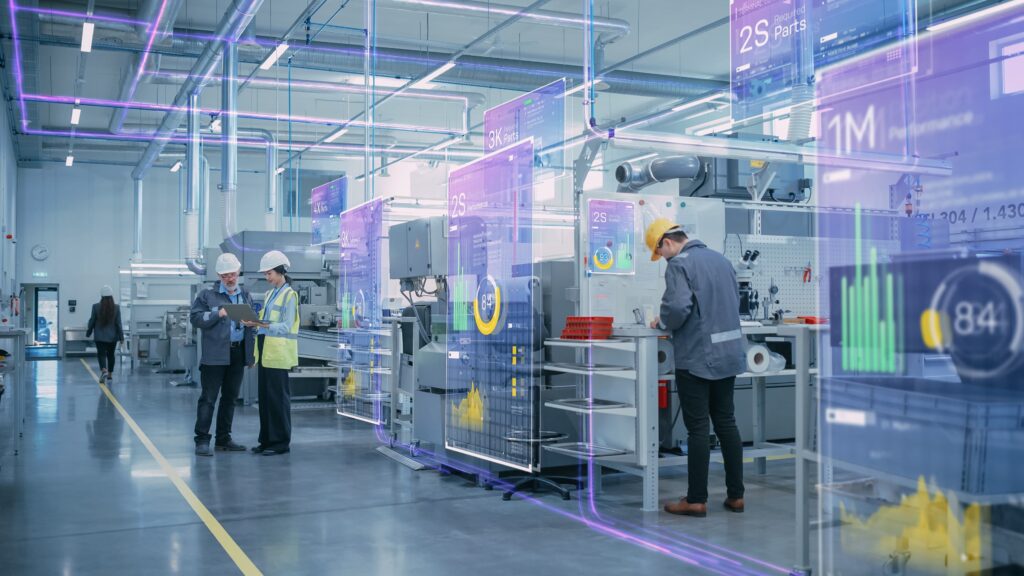
ムダの種類や原因の特定、作業手順や設備の改善、現場の意見の取り入れなど、7つのムダをなくすためのポイントを説明します。
ムダの種類・原因・場所を見つける
まずは、どの種類のムダが、どこで、なぜ発生しているのかを、データ分析や現場観察から明確にします。例えば、製品の品質不良が頻発する場合、その原因を追究し、どの工程で問題が発生しているのかを特定します。ムダが発生する要因を特定することで適切な対策案を検討できます。
作業手順を改善する
作業手順を見直し、無駄な動作や工程を削減することで、効率的な生産が可能になります。標準作業を設定し、作業員が効率的に動ける環境を整えることが重要です。
例えば、必要な道具や材料を手元に配置したり、作業手順を見直したりすることで、無駄な動きを減らすことができます。作業手順の改善には、一方的に指示するのではなく、現場の声を反映させ、実際に作業を行う人々の意見を取り入れることが大切です。
設備の改善、更新を行う
老朽化した設備の改善や更新を行い、品質不良の発生を防止することで生産効率を高めることも重要です。自動化設備を導入するなど、新しい技術や設備を導入することで、多くのムダを削減できます。
また、定期的なメンテナンスを行い、設備の故障を防ぐことで、安定した生産を維持することができます。設備の改善は、初期投資が必要ですが、長期的には生産性の向上とコスト削減につながります。
レイアウトを改善する
工場内のレイアウトを見直し、運搬距離を短縮することで、運搬のムダを削減できます。その際、現場の実際の作業状況を観察し、レイアウトの見直しにより、他の作業に影響はないかなどを詳細に検討し、最適な配置を決定することが重要です。
小さな改善から始める
最初から大きな投資のかかる改善を行わなくても、現場での小さな工夫や改善を継続的に行うことで、全体として大きな効果を得ることができます。例えば、作業環境での整理整頓や、作業手順の微調整など、日常的な改善を積み重ねることが重要です。
現場の意見を取り入れる
現場の作業員からの意見を取り入れることで、実際に役立つ改善策を見つけやすくなります。日常的に作業を行っている作業員の意見を反映させることで、現実的かつ効果的な改善策を立てることができます。
また、定期的なミーティングを開催し、現場の声を積極的に取り入れることも重要です。そのためには、作業者が現場でムダを感じる意見を集約できるような仕組みを構築しておく必要があります。
具体的な目標を立てる
改善のための具体的な目標を設定し、それに向かって計画的に取り組むことが大切です。生産効率の向上やコスト削減など、具体的な数値目標を設定することで、改善策の進捗を確認し、達成度を評価することができます。
データを測定する
改善の効果を数値で測定し、成果を確認することで、継続的な改善が可能になります。生産効率やコスト削減効果のデータを活用することで、客観的な評価が可能となり、改善策の効果を明確に把握し、さらなる改善につなげることができます。
品質管理を徹底する
品質管理を徹底することで、不良品の発生を防ぎ、全体の生産効率を高めます。品質管理は、生産過程の各段階で行うことが重要です。品質管理の強化により、不良品の発生を最小限に抑え、高品質な製品を安定して提供することで、顧客の信頼を得ることができます。
生産管理システムを導入する
生産管理システムを導入することで、さまざまなデータが分析できるようになり、ムダの発見がスムーズになります。システムを活用することで、リアルタイムでのデータ管理が可能となり、迅速な対応ができます。また、生産計画の立案から進捗管理、品質管理までを一元的に行うことが可能になります。これにより、生産過程全体を効率化し、ムダのない生産を実現できます。
7つのムダ削減に役立つ「生産管理システム」とは
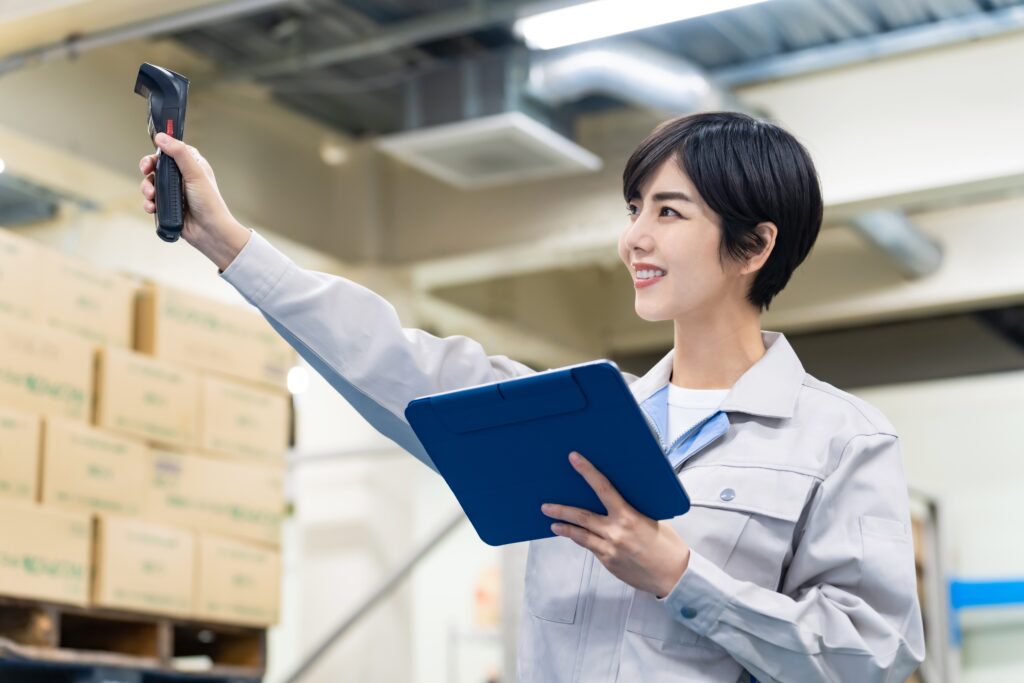
生産管理システムは、ムダを無くすのにとても効果的です。生産管理システムを導入することで、生産工程をリアルタイムに見える化でき、7つのムダを減らすための現状把握を効率的にできます。
生産管理システムとは、製造業の生産活動を一元管理するためのツールです。在庫管理や工程管理、生産計画の立案から進捗管理、品質管理までトータルで管理し、リアルタイムでデータ収集することで、ムダの発見や分析を行うことができます。
ムダのない生産体制を構築する方法の一例として、以下3つを紹介します。
生産計画の最適化
生産管理システムで最適な生産計画を立てると、造り過ぎのムダを防ぐことができます。また、作業実績データや作業負荷も集計することで、生産計画と生産実績の予実管理ができ、生産計画の改善にも役立てられます。
在庫管理の精度向上
生産管理システムの在庫管理機能で、正確な在庫をリアルタイムに見える化することで、適正在庫を保ちやすくなります。その結果、過剰発注による原材料や部品在庫のムダや、造り過ぎのムダを防ぐことができます。
品質管理強化による不良品削減
一部の生産管理システムには、ロット管理や期限管理、検査管理といった品質管理機能があります。ロット間違いや使用期限切れ原料の誤使用といった、製造工程での不良のムダを減らすことができます。検査管理機能で、各工程の検査内容も標準化できます。
また、各工程の記録を集約することでトレーサビリティも強化できるため、不良や手直しが発生した際の分析も容易になります。どのロットの生産時に、どのラインで誰が作業していた時に不良が発生したか把握することで、再発防止のために的確な対策を打つことができます。
生産管理システムでムダをなくした実例
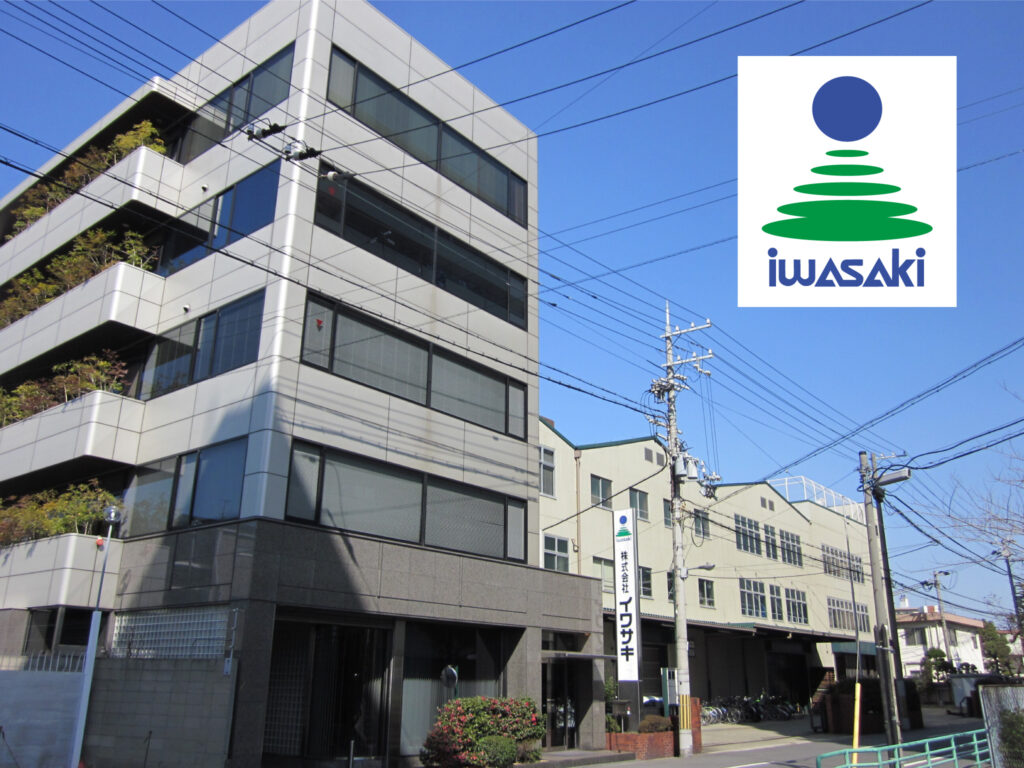
実際に、生産管理システムを導入したことで、ムダ削減に成功した事例を2件紹介します。
在庫のムダの削減事例
ある組立業界の企業では、在庫管理のシステム化によって、在庫を持たなくても良い部品や発注点を下げられる部品を発見し、在庫削減を実現しました。その結果、年間100万円の在庫金額の削減に成功しました。
詳細:在庫管理のシステム化に成功!リアルタイムな在庫管理で年間100万円の在庫削減
不良のムダの削減事例
ある化粧品製造企業では、類似原料の誤使用や工程飛ばしなどが原因の不良のムダが、年間数千万円分発生していました。そこで、生産管理システムとバーコード管理を併用し、各工程や原料使用時にバーコードによる正誤チェックを導入しました。異なる原料や工程のバーコードを読み込むとアラートが出るようになり、経験の浅い作業者でもミスを起こさない仕組みを確立しました。
その結果、誤使用や工程飛ばしによる不良のムダが0件になり、数千万円の廃棄コストを削減しました。
詳細:誤使用・誤投入0件、年間損失額の数千万円が0円に!ハンディ端末で工数削減・属人化解消も成功
22種類の生産管理システムをランキングで比較
初期費用相場や選び方のポイントをチェック
生産管理システムをそれぞれの特徴や初期費用相場などで比較したい場合は、「生産管理システムランキング」も是非ご覧ください。生産管理システムは、自社の製品・生産方式・企業規模などに適したものを導入しないと、得られるメリットが限定されてしまいます。事前適合性チェックや生産管理システムを選ぶ前に押さえておきたいポイントも解説していますので、製品選びの参考にしてみてください。