QCサークル活動のポイント:メリット・注意点、現場改善の具体的な進め方まで解説
公開日:2024年12月05日
最終更新日:2024年12月05日
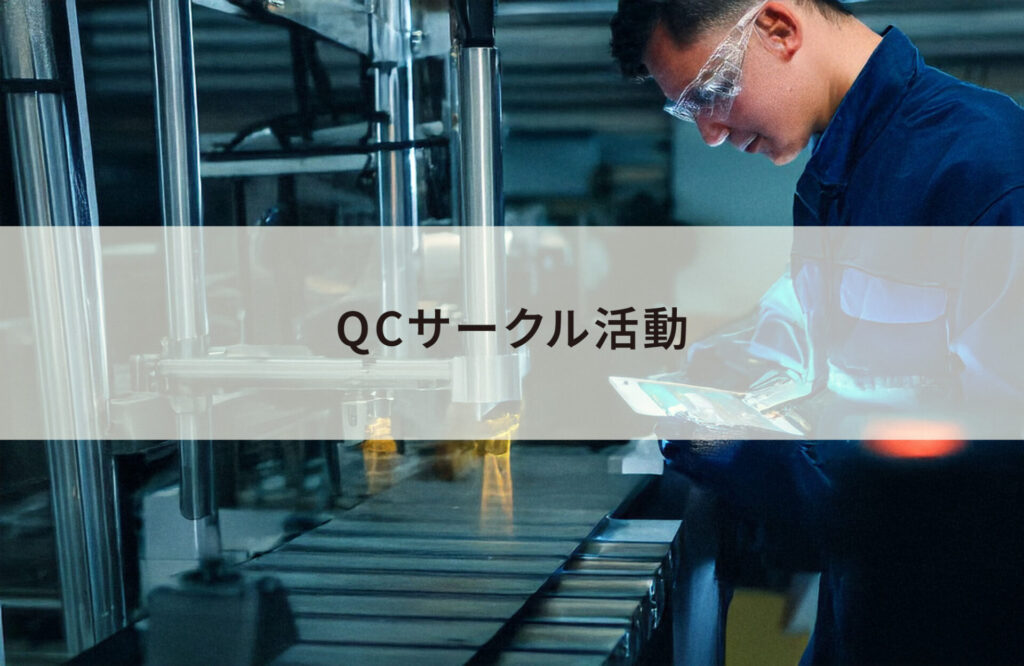
QCサークルとは:ボトムアップ型の現場改善活動
QCサークルは、小グループ単位で自発的に行うボトムアップ型の現場改善活動で、TQC(Total Quality Control/総合的品質管理)の一環として発展してきました。チームとして現場での主体的な改善活動を加速し、製品の品質向上や業務効率化を実現することで、企業全体の業績向上に貢献する活動です。
QCサークルの起源:TQCにおける現場の取り組み
QCサークルは、1960年代にトヨタ自動車へ導入・発展したTQC(総合的品質管理)の取り組みの中で生まれました。
TQC(Total Quality Control)は、全社的な品質管理を実現し、全員参加で企業全体の品質向上に取り組む管理手法です。その中で、QCサークルは、製造現場の問題解決や業務改善活動を担う存在で、TQCの理念を現場レベルでカタチにするための活動といえます。
小グループで行うボトムアップ型の改善活動
QCサークルは、経営層や上司からの指示に基づくトップダウンではなく、職場の構成員が自主的に進めるボトムアップ型の改善活動です。現場の小グループが主体となり、職場の課題を自ら見つけ、参加者同士で協力して問題解決に取り組みます。従業員の問題解決能力を向上させたり、業務に関する知識を深めたりする機会としても活用できるでしょう。
その結果、熟練の個人単独の取り組みだけでなく、経験の浅い従業員のスキルアップ・技能伝承などにより、組織全体の生産性向上に繋がります。
QCサークルの組織構成
QCサークルは、職場から選定されたリーダー・メンバーから構成され、職場を熟知した上席・管理職がアドバイザーとして参画します。リーダー、メンバー、アドバイザーの役割は次の通りです。
- リーダー:メンバーの意見を取りまとめ、活動の方向性を決定し、進捗管理を行う。
- メンバー:取り組みに関するアイデア提案、具体的な改善作業を行う
- アドバイザー:方向性の軌道修正をしたり、技術的・管理的サポートを行う
5〜10人程度の少人数でグループを構成することが多く、メンバー全員が意見を出し合い、改善活動に取り組みます。
QCサークル活動のメリット
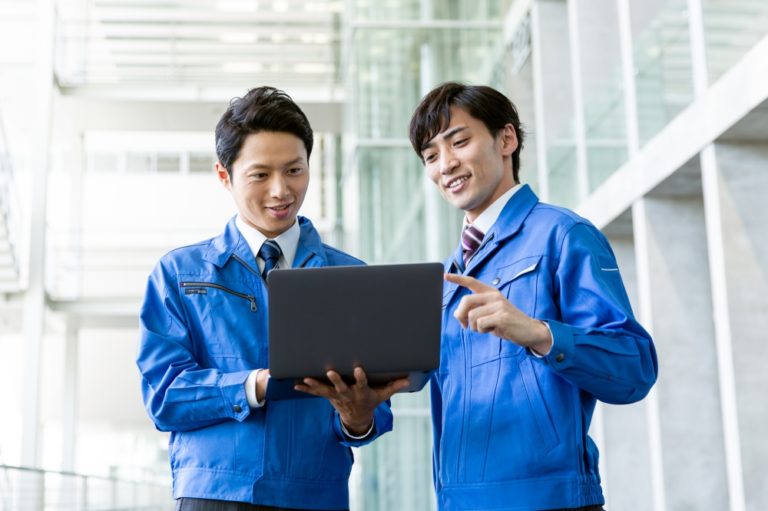
QCサークル活動は最終的に組織全体の生産性向上が最終目標ですが、それぞれの職場において生産性向上以外にも多くのメリットがあります。
職場のチームワーク向上
QCサークル活動では、改善活動を職場内で分担して取り組むため、チームワークの向上も期待できます。意欲や力量に富むメンバーが一人で実行するものではなく、職場の各メンバーが協力して課題解決に取り組みます。
特に、接点の少ない異なる立場・役割のメンバー間でもコミュニケーションを取りながら進めるため、お互いの理解や信頼関係が深まります。その結果、業務でやや遠い関係性の人と関わる際にも、円滑に進めやすくなります。
製品品質・コストへの意識向上
QCサークルは、製品の品質(Quality)・コスト(Cost)に関する改善を目指した取り組みです。現場での通常業務では、目の前の与えられた作業以外に目を向ける機会は多くありません。しかし、実際の業務では、製造した製品をできるだけ高品質・低価格で作りこむことも重要です。
また、QCサークル活動では、具体的な品質向上・コスト削減の貢献目標を掲げて活動を進めるため、従業員の意識向上にもつながりやすいです。さらに、活動の取り組みでは、自分たちのアイデアや努力がカタチになるため、普段から従業員一人ひとりが品質やコスト管理に目を向けられるようになります。
従業員のスキルアップ
QCサークル活動を通じて、経験の浅い従業員を中心として、次のようなスキルを向上させることができます。
- 現場ノウハウ継承:経験豊富な従業員から作業に関する暗黙知を引き継ぐ
- 問題解決能力:現場の課題を分析し、改善策を考える
- データ分析力: 改善効果を客観的に評価するため、データ分析手法を身につける
- コミュニケーション能力:意見交換や議論を通じて、関係者と円滑に対話する
- プレゼンテーション能力:活動成果を報告し、他者に分かりやすく伝える
これらのスキルアップは従業員個人としての成長だけでなく、職場全体のパフォーマンス向上にも寄与します。
QCサークル活動の注意点
QCサークル活動を成功させるには、活動時間の確保や、メンバー間のモチベーション維持・向上、活動が形骸化しないような工夫が求められます。
活動時間の確保が難しい
QCサークル活動は、通常の業務時間外で行われることが多く、活動時間の確保が難しいことも少なくありません。特に繁忙期や納期が迫っている場合には、メンバー全員の業務スケジュールを調整することが現実的でない状況もあります。
そのため、QCサークルに参加していない従業員にも活動内容を周知し、職場全体の理解を深めることが重要です。これにより、業務中の活動時間を確保しやすくするため、職場全体で協力を求めやすい雰囲気を作ることができます。
メンバー内でのモチベーション格差が大きい
全メンバーが同じ熱意を持って参加することが難しい現実もあります。特にリーダーは推進する立場ですが、メンバーによっては目の前の業務以外に目を向けることが難しかったり、通常勤務時間外で行う場合には私用を優先したりすることも少なくありません。
メンバー内でモチベーションの差があると、全員参加型の議論にならず、狭い視野での取り組みに留まります。また、一部のメンバーに負担が集中することで、メンバー間での不平不満の温床となり、活動自体の停滞にもつながります。
このため、リーダーはメンバーの意欲・力量を踏まえ、適切に役割分担して進められるよう配慮することが求められます。
難しいテーマにチャレンジしにくい
QCサークル活動は、製造現場が中心になって進め、1年間の活動期間で取り組むことが多いです。このため、技術的にハードルの高いテーマ、部門外の調整が必要な重課題に取り組むことは現実的ではありません。
サークルメンバーだけで解決が難しいテーマは、成果報告まで到達が難しいことも多く、自力で達成可能なテーマに留まることも多いのが現実です。難しいテーマに取り組みたい場合には、事前にリーダーとアドバイザーで協議を進め、部署外の協力準備をするとよいでしょう。
活動が形骸化しやすい
QCサークル活動が長期継続すると、容易にできる改善テーマが枯渇してしまい、成果発表しやすい活動報告のための活動に終始することもあります。形式的な活動に陥ると、サークル活動のメリットは得られず、貴重な参加者のリソースを浪費することになります。それゆえ、QC活動は時代遅れの取り組みであると揶揄されることも少なくありません。
この場合は、難しい大テーマを小テーマに分割し、小テーマをQCサークル活動として取り組むことが有効です。より難易度・貢献度の高いテーマとすることで、マンネリ化したメンバーに対して動機付けをしやすくなります。リーダー・メンバーの力量によっては、単年での活動グループを限定した持ち回り制とし、数年周期で活動に取り組むという方法もあるでしょう。
QCサークル活動の具体的な進め方(事例付き)
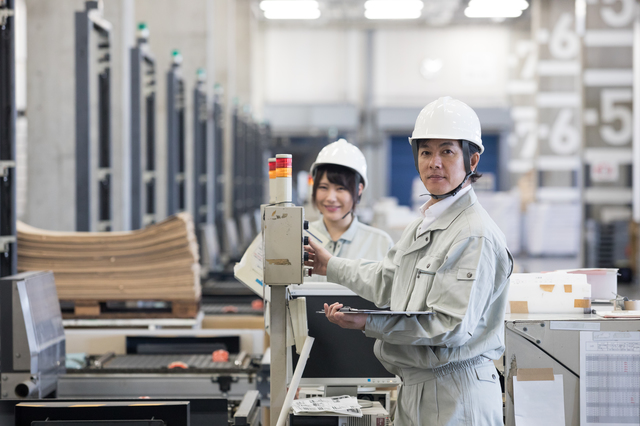
QCサークル活動を効果的に進めるためには、リーダーの選任や課題の設定、改善策の立案と実行、振り返りなどが重要です。これらのステップを着実に進めることで、活動で実用的な成果を生み出すことができます。
小グループ・リーダーの選任
QCサークル活動を効果的に進めるためには、適切なリーダーとメンバーを選定します。小グループを選任するための方法は様々ですが、一例として、以下のような構成で選任することができます。
- 単一部署のみ: 同じ部署・チームのメンバーで、共通の業務課題に取り組む
- 部門・職種横断: 異なる視点・専門知識を持つメンバーで、広い視野で課題解決を推進する
- 自発的な参加者: 意欲の高いメンバーで構成され、積極的な活動を進める
また、リーダーには、メンバーの意見を引き出し、活動の方向性を示し、成果報告の中心的役割を担うことに長けた人が望ましいです。リーダーに求められる役割は大きいため、リーダーの力量がチーム全体の成果・モチベーションに大きな影響を与えます。このため、適切な課題設定は、メンバー全員参加で活動に取り組み、成果を挙げるための大切なポイントの一つです。
テーマ・課題の設定
QCサークル活動としては、自力である程度の成果が見込め、具体的で定量的に達成度を確認しやすいテーマ・課題を設定します。
他者への協力要素が大きすぎたりすると、メンバーとして自ら実行する改善内容が少なくなりがちです。また、設定した課題が曖昧であったり、範囲が広すぎると、メンバーの関心・改善行動が発散してしまい、思うように進みません。このため、適切な課題設定は、メンバー全員参加で活動に取り組み、成果を挙げるための大切なポイントの一つです。
要因分析
取り組むテーマを決めた後は、要因分析をすることで、その課題の原因を特定して改善のための方向性を決めます。QCサークルでは、QC7つ道具を用いて実施することが多いです。
例えば、金属加工製品Xの品質不良低減というテーマに取り組む場合、下図のようにパレート図を用いて品質不良の発生原因を調査します。この場合は表面粗さ不良が製品Xの品質不良の40%を占めるため、これを改善することが最も費用対効果が大きいと結論付けられます。
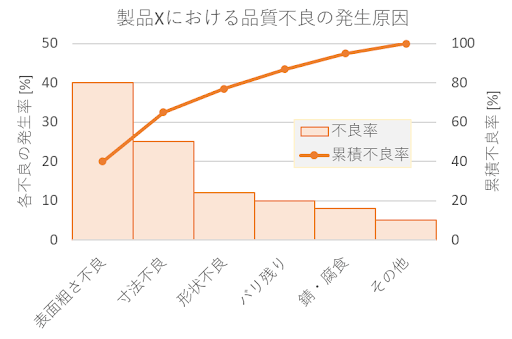
さらに、表面粗さ不良に関して、特性要因図を用いて要因分析を行い、不良発生の真因を特定します。実際には、それぞれの可能性について、工程データを実際に取って分析することで、想定した事象のうちどれが真因であるかを絞り込みます。この例では、表面粗さ不良に対して、研削工具の摩耗が深く関係していることまで特定できました。
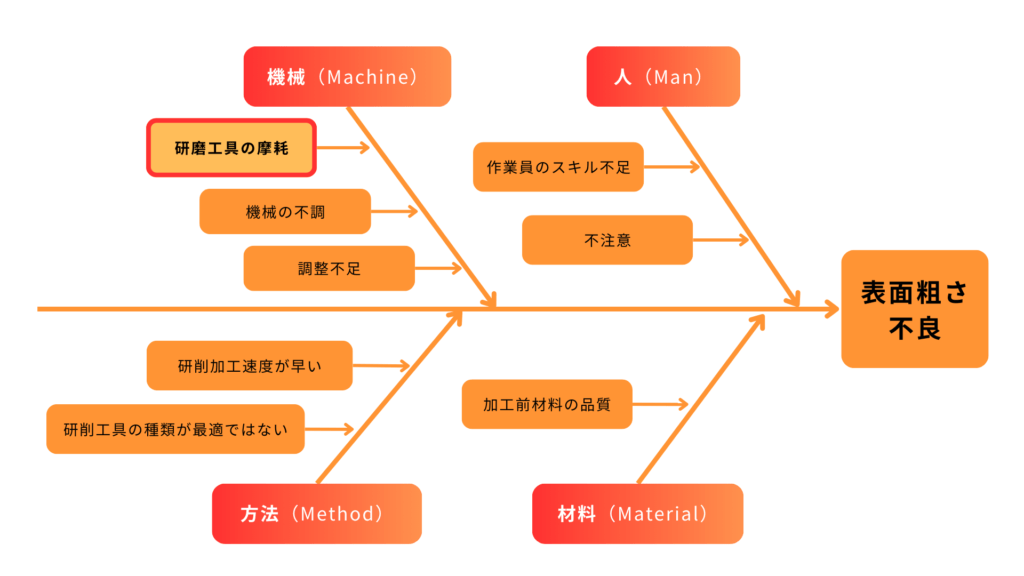
改善策の立案と比較検討
要因分析の結果に基づき、改善策を複数立案し、その中から最も効果的なものを選定します。上記の製品Xの品質不良の例において、研削工具の摩耗対策案とそれぞれの費用・装置停止時間は以下の表の通りでした。
対策案 | 製品1万個あたり | ||
研削工具代 | 労務費 | 装置停止時間 | |
研削工具の交換頻度を上げる | 1万円 | 5万円 | 10時間 |
摩耗しにくい研削工具を使う | 10万円 | 1万円 | 2時間 |
装置の稼働率がそれほど高くなければ、研削工具の頻度を上げるのがトータルコスト(研削工具代+労務費)で有利とわかります。
このように、改善策を複数比較検討することで、実行に移すべき最適な方法を見つけることができます。
改善策の実行
比較検討した改善策改善策を実行します。実行に移す際には予期せぬトラブルが発生する可能性もあるため、事前に上司とも十分相談の上計画的かつ慎重に進めます。
改善効果の確認
改善策を実行した後は、必ずその効果を見える化して改善策の有効性を評価します。
製品Xの例では、研削工具の交換頻度を上げることで、表面粗さ不良が〇〇%減り、製品ロス率が△△%改善した、と算出できます。対策に要した費用、製品ロス率改善によるコストダウン効果を合わせて、この取り組み全体としての改善効果を金額で表現できると尚良いでしょう。もし期待通りに改善できなかった場合、他の要因を再度検証する必要があります。
このように、振り返りを行うことで、成功した点や改善すべき点が明確になり、次回の改善活動に活かすことができます。
取り組みの発表
QCサークルの取り組みについて、他の職場や上層部に対して、活動報告を行います。
発表の場では他のサークル活動の取り組み・成果などを聞くことで、新たなアイデアや改善策のヒントが得られることも少なくありません。また、発表の中で優秀な活動に対する表彰があれば、従業員のモチベーションアップにも繋がります。
QCサークル活動を成功させる5つのポイント
QCサークル活動を成功させるためには、改善効果が確認できる課題を設定し、定期的にメンバー間で活動の場を持つことも大切です。また、要因分析・改善策の効果確認などでは、QC7つの道具などを活用し、データ・数値をもとに振り返るようにしましょう。
1年で改善効果が確認できる課題を設定する
QCサークル活動は1年単位で取り組む会社が多いので、この期間内で改善効果が確認できる課題を設定するのが良いでしょう。
難しすぎたり、実行に長期間を要したりする課題は、メンバーのモチベーション低下に繋がります。ゴールまでの道のりが長い取り組みの場合は、中間ゴールを設定する、課題を適切に分けて他の職場・小グループと分担する、などの工夫が必要です。
メンバー間で定期的な活動の場をもつ
QCサークル活動を効果的に進めるためには、メンバー間で定期的なミーティングや活動の場を設けることが欠かせません。定期的な進捗確認や意見交換を行うことで、負担が特定の個人に偏ったり、活動そのものが停滞することなく進められます。
定期的に職制チェックを受ける
QCサークルの活動内容や進捗状況は、定期的に職制からのチェックを受けることも大切です。
取り組みが経営的に有効な方向性となっているかを上位役職者目線でチェックし、修正のための助言を得るようにしましょう。行き詰っている場合には、技術的サポートや他部署の応援が必要となる場合もあります。
要因分析にはQC7つ道具を使う
QCサークル活動では、問題の本質を正しく把握するために、QC7つの道具を活用するとよいでしょう。これらの道具はシンプルなため、データの取り扱いになじみの薄い人でも比較的簡単に使うことができます。
客観的なデータから要因分析をすることで、思い込みによる偏った要因の絞り込み、改善効果の小さい取り組みに着手するリスクを減らせます。なお、QC7つの道具とは、以下の7つを指します。
- パレート図:問題の原因を重要度順に並べるためのグラフ
- 特性要因図(フィッシュボーン図):問題の原因を体系的に分析するための図
- ヒストグラム:データの分布状況を視覚的に表示するための棒グラフ
- チェックシート:データ収集や整理に使われる表
- グラフ:データを視覚化し、トレンドや変動を確認するためのツール
- 管理図:工程の安定性を見える化するための図
- 散布図:2つの変数間の関係を視覚的に確認するための図
成否に関わらず、しっかり振り返る
QCサークル活動は、成功・失敗に関わらず、しっかり振り返りを行うことが重要です。改善策についても、1つの実行案だけで解決することは珍しく、期間ギリギリまで試行錯誤するものです。
その中で上手くいった点、反省すべき点をしっかり見つめなおすことで、次回の活動への教訓を得ることができます。またこうした振り返りの大切さを学ぶことで、通常業務のレベルアップにもつながります。
22種類の生産管理システムをランキングで比較
初期費用相場や選び方のポイントをチェック
生産管理システムをそれぞれの特徴や初期費用相場などで比較したい場合は、「生産管理システムランキング」も是非ご覧ください。生産管理システムは、自社の製品・生産方式・企業規模などに適したものを導入しないと、得られるメリットが限定されてしまいます。事前適合性チェックや生産管理システムを選ぶ前に押さえておきたいポイントも解説していますので、製品選びの参考にしてみてください。