GMPとは 運用の流れや認証プロセス、導入メリットをわかりやすく解説
公開日:2024年07月31日
最終更新日:2025年07月22日
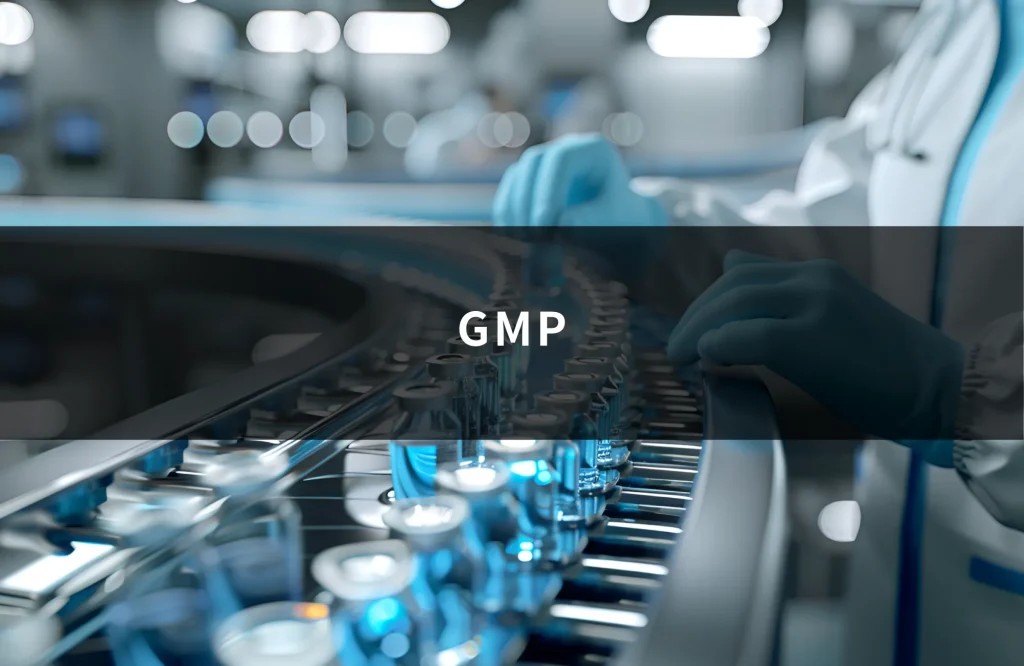
人の生命に関わる医薬品の製造業界において、製品の品質と安全性を保証するためには、厳格な規格が必要です。GMP(Good Manufacturing Practice)は、その中心となる国際的な基準で、医薬品が安全で効果的なものであることを保証するために設けられています。本記事では、GMPの基本概念、適用範囲、および製薬業界での運用方法について解説します。
GMPとは
GMPは「Good Manufacturing Practice」の略で、直訳すると「良好製造規範」となります。これは医薬品の製造において必要な規範や基準を定めたもので、安全で有効かつ品質の高い医薬品を製造するために非常に重要です。日本ではこれを「医薬品の製造管理及び品質管理の基準」と呼び、製薬会社が医薬品を製造する際に遵守しなければならない法的要件となっています。
GMPの基準には、原材料の調達から製品の製造、検査、出荷に至るまでの各プロセスにおける具体的な指針が含まれています。これにより、製品ごとの一貫した品質が保証され、患者が安心して使用できる医薬品の供給が可能となります。また、GMPは単なるガイドラインではなく、多くの国で法的に強制される規則であり、違反した場合には厳しい罰則が適用されることがあります。
この規範を遵守することで、製薬企業は製品の品質だけでなく、その信頼性と安全性を向上できます。GMPは医薬品業界における品質保証の根幹をなすものと言えます。
GMP、GQP、GVPの違い
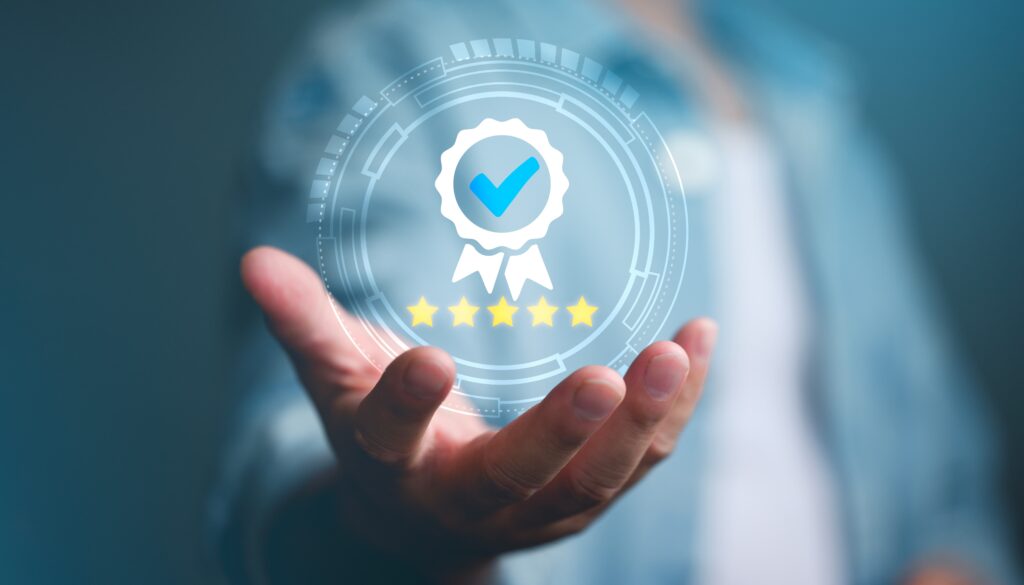
医薬品の製造業界において、製品の品質と安全性を保証するための規範としてGMP以外に「GQP(Good Quality Practice)」、「GVP(Good Vigilance Practice)」があります。それぞれの違いは次のようになります。
GQP
GQPは「Good Quality Practice」の略で、医薬品・医薬部外品だけでなく、化粧品も含む製造販売品質保証基準に関連します。GMPの適用範囲は製造業者(※製造販売業者は製造業者にGMPを遵守させる必要がある)なのに対し、GQPは製造販売業者が対象となります。
GQPは、製品の設計、開発、製造プロセスの監視、最終製品の検査に至るまで、品質管理のシステムを統合的に強化することを目的としています。GQPは、製品が設計された品質仕様を満たすことを保証し、それによって患者の安全と製品の品質を確保します。
GVP
GVPは「Good Vigilance Practice」の略で、市場に出た後の医薬品の安全性を監視するための基準です。これには、副作用や他の安全性に関する情報を収集、評価、理解するプロセスが含まれます。GVPの主な目的は、医薬品のリスクを評価し、必要に応じて適切な安全対策を講じることにあります。これにより、製品の全体的な安全性が向上し、患者に対する保護が強化されます。
GMP含め、これら三つの基準は、それぞれ異なる側面から医薬品の品質と安全性を保障し、製薬業界における規範として機能しています。それぞれの規範がしっかりと実施されることで、高品質で安全な医薬品の提供が可能となります。
GMPの歴史
GMPが制定された背景には、医薬品の安全性と品質を確保する必要性が問われた薬害事件が大きく関わっています。1960年代前半、特にアメリカで複数の医薬品関連の問題が発生し、製薬業界における品質管理の不備を浮き彫りにしました。これを機に、規制が求められることとなりました。
サリドマイド事件
1960年代初頭、催眠薬およびつわり防止薬として用いられたサリドマイドが、重大な副作用を引き起こすことが明らかになりました。この薬を服用した妊婦から生まれた多くの胎児が、四肢の欠損などの重篤な先天性障害を持って生まれました。この事件は、医薬品の安全性評価と市場への導入においてより厳格な規制が必要であることを世界中に示しました。
その他の品質管理問題の発生
サリドマイド事件以外にも、医薬品の不適切な製造プロセスが原因で、薬品の品質にばらつきがある事例が続出していました。これにより、製品の安全性と効能に対する信頼が低下し、患者の健康に重大なリスクが生じる可能性があったため、統一された製造基準の必要性が高まりました。
これらの事件と課題を受けて、アメリカ食品医薬品局(FDA)をはじめとする規制当局は、医薬品の製造過程における厳格な品質管理基準を定めることを決定しました。これが、GMPの制定へと繋がっています。
日本国内におけるGMP
日本では、アメリカでGMPが制定された後の1974年に、行政指導として通知され、1980年にGMP省令が施行されました。さらに2014年は、医薬品査察の国際組織「PIC/S」に加盟し、同組織のGMPガイドラインをもとにしたGMP省令の整備が進んでいます。
GMPの3原則
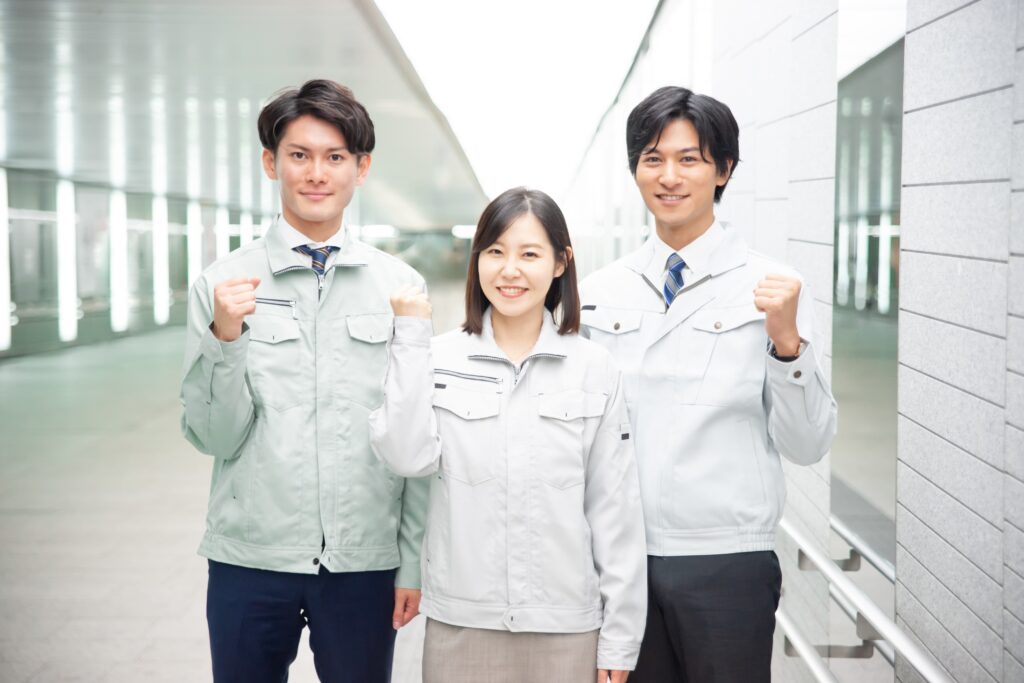
GMPには基本となる3つの原則があります。
人為的な誤りを最小限にすること
人為的な誤りは、操作ミスや手順の誤解により生じる可能性があります。これを防ぐため、GMPでは徹底的なトレーニングと明確な作業手順の作成が必要とされます。各スタッフがその責任と役割を正確に理解し、遵守することで、人為的な誤りを最小限に抑えることができます。また、自動化技術の導入により、人の手による介入を減らすことも有効です。
医薬品の汚染及び品質低下を防止すること
医薬品製造においては、製品の汚染や品質の低下が患者に重大な健康リスクをもたらす可能性があるため、これを防ぐことが極めて重要です。GMPでは、原材料の取り扱いから、製造設備の維持、製品の梱包まで、すべての段階で厳格な衛生管理と品質チェックが求められます。これにより、製品が外部からの汚染や環境因子による品質の劣化から保護されます。
高い品質を保証するシステムを設計すること
GMPの核心は、単に製品が基準を満たすことを確認するだけではなく、品質を保証するシステムを設計し、それを継続的に維持することにあります。これには、品質管理システムの実装が含まれ、定期的な監査、プロセスの評価、改善が必要です。このシステムにより、製造プロセス全体が常に監視され、必要に応じて迅速に対応することが可能となります。
これらの原則に基づき、GMPは医薬品製造業界全体で一貫した品質と安全性を保つための強力な基盤を提供しています。
GMPの要素
GMPは主に二つの大きなカテゴリー「GMPハード」と「GMPソフト」に分けられます。これらの要素は、製品の品質と安全性を保証するために相互に作用し、厳格に管理される必要があります。
GMPハード | GMPソフト | |
主な対象 | 製造設備や環境整備 | 組織運営や管理手順 |
具体例 | ・工場の建屋・空調設備・電気設備・生産設備 | ・品質管理体制の整備・SOP管理・製造記録の管理・品質監査 |
GMPハード
GMPハードは、医薬品製造施設の物理的な環境や設備を指します。これには製造機械、製造環境、設備配置、品質管理室などの具体的な設備が含まれます。これらの設備は、製品が汚染されるリスクを最小限に抑え、安定した品質を維持するために重要です。
例えば、空気浄化システムや特定の温度・湿度を維持する空調システムなどがこれに該当します。製造施設は定期的な保守が必要であり、すべての設備がGMP基準に適合していることが確認されなければなりません。
→ GMPハードとは 役割や対象設備、バリデーション・監査との関連性について解説
GMPソフト
GMPソフトは、製造プロセスの管理、品質保証手順、スタッフのトレーニング、文書管理など、より抽象的で管理的な要素を指します。このカテゴリーは、適切な製造プロセスの確立、品質管理の維持、従業員教育などを通じて、製品が一貫した品質で生産されることを保証します。
具体的には、作業手順書(SOP)の作成と更新、バッチ製造記録の正確な記録、品質監査の実施などが含まれます。これらのプロセスを通じて、GMPは製品の品質不良を事前に防ぎ、万が一の品質問題に迅速に対応できるようにします。
→ GMPソフトとは 求められる要件やGMPハードとの違いを解説
これら「GMPハード」と「GMPソフト」は互いに補完し合い、医薬品製造の全段階で高品質な製品が供給されることを保証します。各製薬企業は、これらの要件を遵守することで、患者の安全を守り、信頼される医薬品を提供する責任があります。
GMPの種類
GMPの適用範囲は広く、異なる製品カテゴリーに特化した複数のGMPが存在します。以下はその主要な種類です。
医薬品GMP
医薬品GMPは、人間用医薬品の製造における品質と安全性を確保するために最も厳格に規定されています。有効成分の安定性、製造プロセスの一貫性、製品の純度と効力を保証することに重点を置いています。医薬品GMPの遵守は、製品が臨床的に効果があり、安全であることを保証します。
医薬部外品GMP
医薬部外品GMPは、効能や効果が比較的穏やかである医薬部外品の製造に関する基準です。これには、肌に塗る薬やリスクが低い健康補助食品などが含まれます。医薬部外品のGMPは、これらの製品が適切な品質管理のもとで製造され、安全性が確保されるように設計されています。
原薬GMP
原薬GMPは、医薬品の有効成分や原材料の製造に特化した基準です。これは、原薬が製薬の品質と安全性の基盤を形成するため、特に重要です。原薬の品質が最終医薬品の効果と直結するため、厳密な規制が適用されます。
化粧品GMP
化粧品GMPは、化粧品の製造過程での品質保証を目的としています。これには、製品の安全性と一貫性を確保するための特定のガイドラインが含まれており、使用者の肌への影響を最小限に抑えることが求められます。
健康食品GMP
健康食品GMPは、栄養補助食品や健康補助食品の製造に適用される基準です。これは、製品がその表示通りの栄養成分を含んでいること、不純物や有害物質が含まれていないことを保証するために重要です。
これらのGMPはそれぞれ、特定の製品カテゴリーに対する厳格な品質基準を設けることで、消費者が安全で信頼性の高い製品を利用できるようにしています。それぞれのGMPは基本的な原則を共有しつつも、製品の特性に応じて異なる規定が設けられている点が特徴です。
GMPの運用の流れ
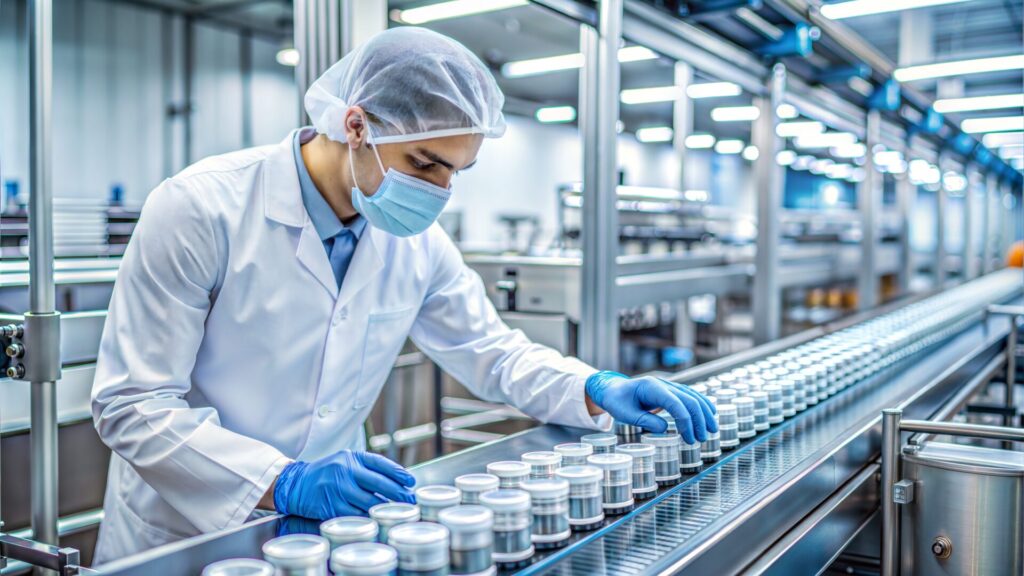
GMPの運用は、製品設計の初期段階から製品が市場に出るまで、さまざまな段階を経て行われます。以下は、GMPの運用が通常どのように進行するかの概要です。
品質基準の設定
最初のステップは、製品に必要な品質基準を設定することです。これには、製品の安全性、効能、そして純度を定義する詳細な仕様が含まれます。これらの基準は、製品開発の全過程でガイドとして機能し、最終製品が規制要件を満たしていることを保証します。
施設と設備の準備
適切な製造施設と設備が準備され、これらがGMP基準に準拠しているかどうかが確認されます。施設は清潔で整理されている必要があり、設備は定期的に保守され、適切に校正されていることが求められます。
製造プロセスの検証
製造プロセスは事前に厳格に検証され、すべての工程で品質が管理されていることが保証されます。この段階では、原料の検査、プロセス中の監視、および製品の最終検査が含まれます。
従業員のトレーニング
従業員は、彼らの担当する具体的な作業に関連するGMP基準を理解し、遵守するように訓教育されます。これには、適切な作業手順、衛生管理、および緊急時の対応が含まれます。
文書管理
全ての製造活動は詳細に文書化され、これには原料の入手から、製造、検査、製品のリリースに至るまでの記録が含まれます。文書管理は、適切な追跡と監査が行えるようにするために不可欠です。
継続的な監査と改善
GMPの運用には、定期的な内部および外部の監査が含まれており、遵守状況を評価し、必要に応じてプロセスの改善を行います。これにより、製造プロセスの健全性と製品の品質が維持されます。
これらのステップを通じて、GMPは医薬品の製造プロセス全体を通じて厳格な品質管理を実施し、消費者に安全で効果的な製品が提供されることを保証します。
GMPの工場認定
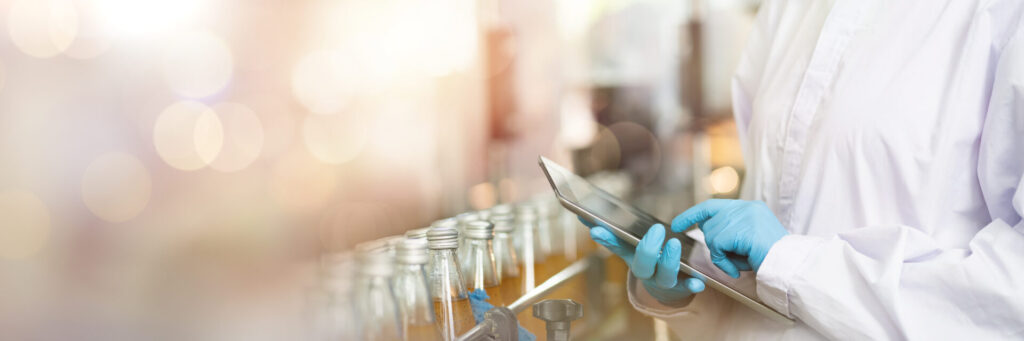
GMPは認定を通じて、製造工場が製品の品質、安全性を一貫して維持できていることが証明されます。GMPの認定プロセスは以下のようになります。
事前評価
製造施設は自己評価を行い、GMP基準に準拠しているかどうかを内部的に確認します。この評価は、施設の設計、設備、作業プロセス、従業員のトレーニングなど、多岐にわたる観点で行われます。
文書提出
GMP基準に準拠していることを示すために、運用手順、品質管理システム、従業員の訓練記録などの文書を規制当局に提出します。
現地調査
規制当局または第三者の監査機関が工場を訪問し、文書のレビューと現場の実態を確認します。この調査は、施設がGMPのガイドラインに適合しているかを評価するために行われます。
問題の特定と是正措置
調査で問題が発見された場合、工場は指摘された問題を是正するために改善計画を立て、実施します。
認定の取得
全ての基準が満たされたと評価された場合、工場はGMP認定を取得します。これにより、工場は国際市場での製品販売の資格を得ることができます。
GMP認定は、製品が世界各国の規制要件を満たしていることを保証するために不可欠です。認定を持つ工場は、高品質な製品を一貫して提供できるという信頼を市場から得ることができます。
GMPにおけるバリデーションとは
GMPには「バリデーション」という重要な概念があります。GMPにおけるバリデーションとは、決められた製造管理や品質管理を手順通りに行えば、期待通りの結果が出ることを検証・文書化し、目的とする品質での製造を恒常的に行えるようにすることです。
主なバリデーション対象は、以下4種です。
- 設備、システム、装置
- 製造工程
- 洗浄工程
- 品質試験・分析の方法
一例として、製造工程で完成品を抜き取り検査する場合、抜き取っていない残りの製品も問題がないことを示す必要があります。その際、製造設備や装置などの設定を計画・文書化したうえで検証・評価したうえで、均一な品質で製造できる条件を科学的に保証できれば、バリデーションに対応できたといえます。
バリデーションにおいて重要な点は、期待通りの結果が出ることを検証するだけでなく、文書化する点です。この文書は、正確かつ継続的に記録する必要があります。紙での記録だと、データを改ざんできない状態を作ることが難しいため、GMPの観点だと不正ができない仕組みのシステム活用などが望ましいと言えます。
→ GMPにおけるバリデーションとは 医薬品や食品業界必須の品質管理の基本
GMP導入のメリット
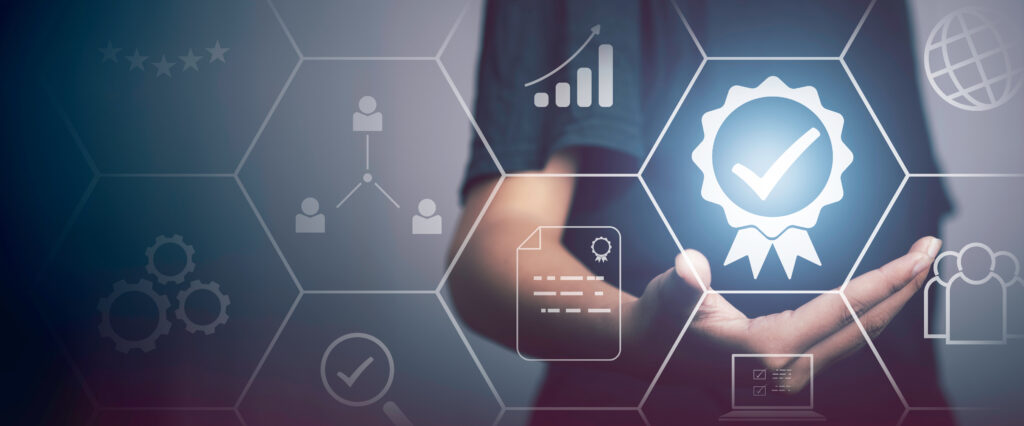
GMP導入は医薬品等製造に必須であるだけでなく、導入することによって以下3点のメリットがあります。
品質の担保
GMPを導入する最大のメリットは、製品の品質を一貫して担保できることです。GMPに準拠することにより、製造プロセスのすべての段階で厳格な品質管理が施され、製品の純度、安定性、効能が保証されます。
これにより、製品の不良率が低下し、リコールや品質問題による経済的損失のリスクを大幅に軽減できます。また、厳しい規制が設けられている市場へのアクセスが可能となり、グローバルな販売網を確立しやすくなります。
市場競争力の向上
GMP認証を取得した製品は、国際市場での信頼性が高まります。これにより、GMPを導入していない競合他社と比べて、市場での優位性を確保することができます。特に、厳格な品質基準を要求する欧米市場などでの販売が見込めるため、ビジネスの拡大に直結します。さらに、規制当局の承認プロセスがスムーズに進むため、市場への製品導入が早くなり、先行者利益を享受できる可能性が高まります。
ブランドイメージの向上
GMPは単に製品の品質だけでなく、企業イメージを向上させる要素ともなります。消費者や取引先は、GMP認証を受けた企業を信頼しやすく、その製品を安全で信頼性が高いと見なされるため、ブランドイメージの向上につながります。また、社会的責任を果たしている企業としての評価が高まり、新たなビジネスチャンスが生まれることも期待できます。
GMP導入の課題
GMPの導入にはいくつかの課題が伴います。これらの課題は、企業がGMPを効果的に運用し、維持する上での障壁となることがあります。
業務負荷が増える
GMP基準に準拠するためには、製造プロセスのすべての段階で厳格な品質管理と文書化が求められます。これにより、従業員の業務負荷が大幅に増加する可能性があります。
特に、小規模な製造業者にとっては、日々の作業に加えて、GMPに関連する監視、記録、報告業務が煩雑になることが課題となります。これらの追加的な責任は、従業員のストレス増加やミスの発生リスクを高める要因にもなり得ます。
GMPに精通した専門家がいない
GMPの効果的な導入と維持には、この分野に精通した専門家の存在が不可欠です。しかし、新たにGMPを導入しようとする企業にとって、適切な専門知識と経験を持つ人材を見つけることは大きな課題です。専門家不足は、GMPの基準に準拠したシステムの設計、実装、監視の難易度を上昇させます。
GMPに対応したシステムの整備が必要
GMPの基準を遵守するためには、製造施設や装備のアップグレード、適切な品質管理システムの導入が必要です。これには、初期投資としての高額な費用が伴うため、特に中小企業にとっては大きな負担となることがあります。また、既存の設備やシステムをGMP基準に合わせて改修する過程で、生産ラインの停止や業務の中断が発生する可能性もあります。
これらの課題を解消するためには、自社にあった適切な品質管理システムや生産管理システムの導入が有効です。
システム導入時に必要な「コンピュータ化システムバリデーション(CSV)」
GMP対応のためにシステムを導入する際は、コンピュータ化システムバリデーション(Computerized System Validation、以下CSV)が必要になります。CSVとは、医薬品等の製造に活用するシステムに欠陥がなく、期待通りの結果を得られることを検証・文書化するプロセスです。
CSVでのバリデート自体は、システムベンダーではなく導入企業が行う必要があります。CSVを少しでもスムーズに進めるためには、CSV支援が可能なベンダーを選定することをおすすめします。CSV支援の実績がないベンダーの場合は、別途CSV支援サービスなどを利用することも可能です。
GMPの導入には生産管理システムがおすすめ
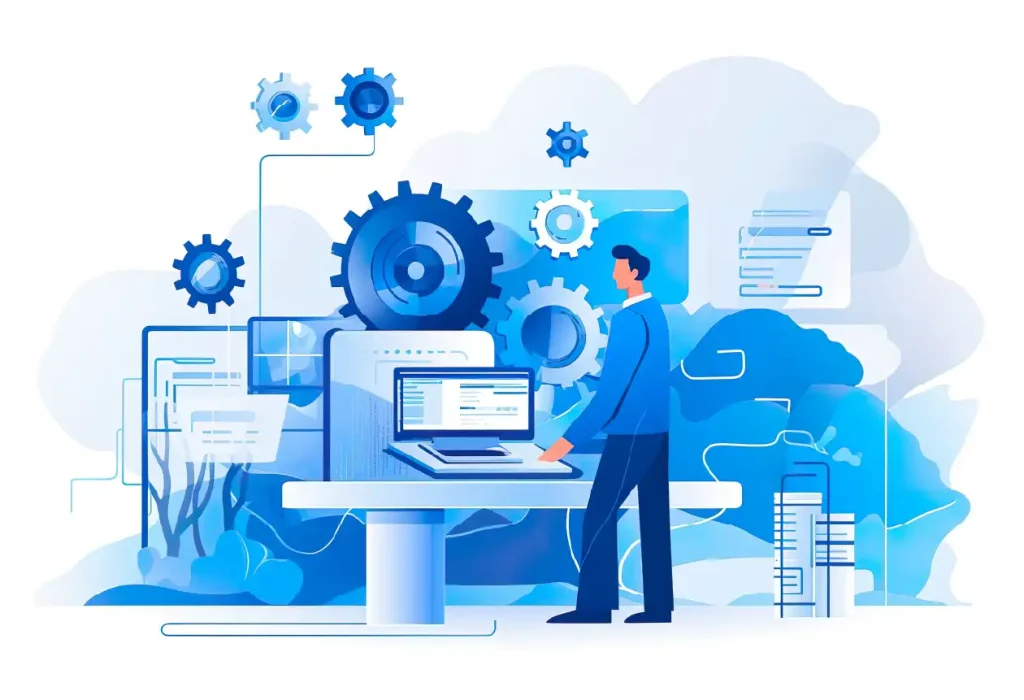
GMP基準の導入と維持において、生産管理システムの利用が非常に有効です。GMPでは、製品の品質保証を実現するために、製造過程のすべてのデータを正確に記録し、トレーサビリティを保持することが求められます。これには、原材料の調達から製品の出荷までの各ステップの詳細な記録が含まれます。
生産管理システムは、これらの要求を効率的に満たすための強力なツールです。システムを導入することで、データの自動収集と整理が可能となり、手動でのデータ入力に伴う人為的ミスを減少させることができます。さらに、生産管理システムは、リアルタイムでのプロセス監視を可能にし、品質管理の精度を向上させます。
また、GMP対応の生産管理システムは、監査時に必要とされる情報の迅速な提供が可能です。監査対応の迅速化は、製薬企業にとって大きな利点となり、コンプライアンス遵守に関する業務の負担を軽減します。
22種類の生産管理システムをランキングで比較
初期費用相場や選び方のポイントをチェック
生産管理システムをそれぞれの特徴や初期費用相場などで比較したい場合は、「生産管理システムランキング」も是非ご覧ください。生産管理システムは、自社の製品・生産方式・企業規模などに適したものを導入しないと、得られるメリットが限定されてしまいます。事前適合性チェックや生産管理システムを選ぶ前に押さえておきたいポイントも解説していますので、製品選びの参考にしてみてください。