生産管理に重要なIE(インダストリアル・エンジニアリング)とは 具体的な分析手法や改善方法を解説
公開日:2023年07月05日
最終更新日:2024年12月05日
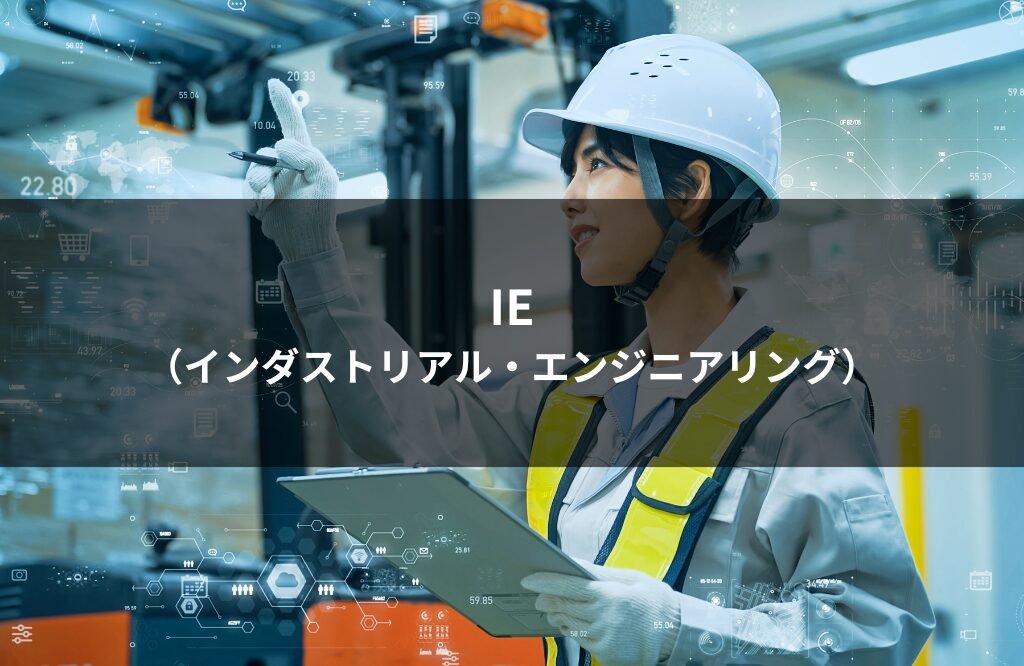
生産管理においてIE(インダストリアル・エンジニアリング/Industrial Engineering)の活用は、生産効率向上やコスト削減に非常に有効です。IEとは、生産現場の業務改善の手法の一つであり、客観的な分析に基づきムダの排除や人材育成を行うことができます。
本記事では、IEの基本概念や導入の目的、具体的な分析手法から導入手順まで解説します。また、導入を成功させるコツや具体的事例についても紹介します。
IEとは
IE(Industrial Engineering)は、生産活動の効率化や品質改善のために、作業工程や作業手順、運搬経路などを科学的かつ工学的に分析し、改善する手法です。生産工学、産業工学、管理工学、経営工学などと訳されることもありますが、どれも最適なものはなく、一般的に「IE」の略称で呼ばれています。
IEを活用することにより、生産活動を数値や表で表すことができます。経験則や勘、イメージだけでなく、数字を用いた客観的視点での分析が可能となります。特に、生産性向上に深く関わる生産管理においては、IE活用のメリットが多いといえます(詳しくは後述)。
近年IEは、企業の生産性向上や品質の安定化、コスト削減を目的として、製造業やサービス業で幅広く活用されています。
IEを導入する目的
企業がIEを導入する主な目的は、次の通りです。
- 生産性向上
- コスト削減
- 品質改善
- 人材育成
- 作業環境の改善
- スペースや資源の有効活用
生産現場において、IEを活用することで作業の標準化や効率的な作業方法が構築でき、リードタイム短縮や無駄の削減が可能です。また、IEを導入することで改善活動の効果を数値で表せるようになり、他工場への展開なども容易になります。
生産活動を数値に落とし込み教育を行うことで、IEを意識した改善活動を行える人材を育成することもIEを導入する目的の一つです。
IE手法の種類:IE 7つ道具
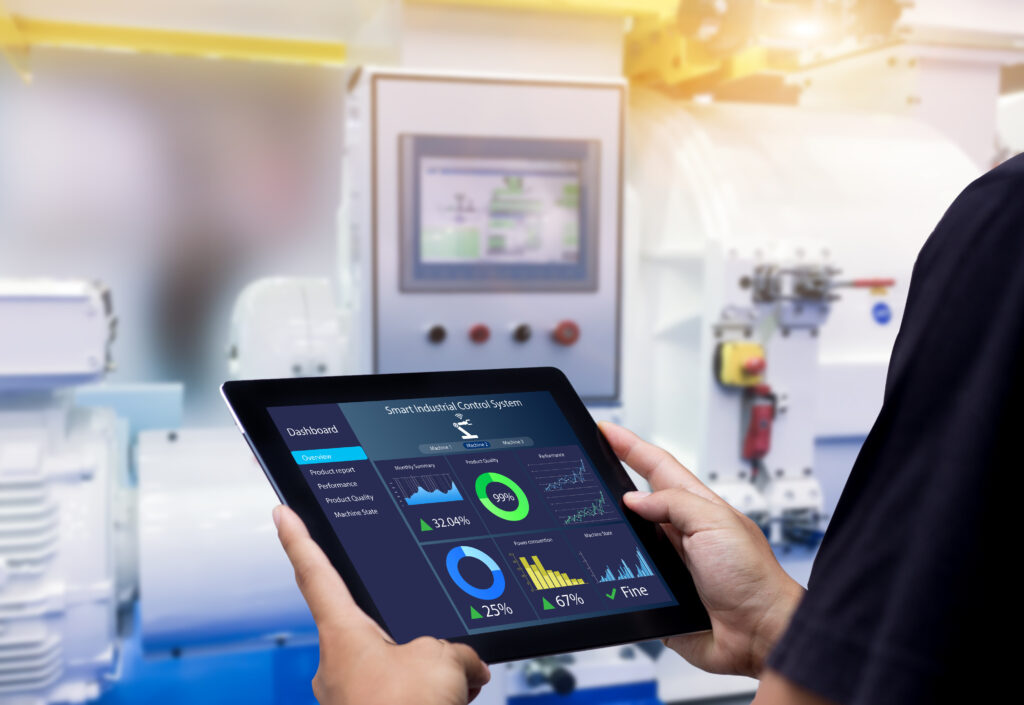
IEには多くの手法があり、用途や目的に応じて使い分けます。代表的な手法は以下の通りです。
IE手法 | 具体的な方法 | 用途・目的 |
方法研究 | ・工程分析・動作分析・運搬分析(マテハン分析) | 製造の流れや動作のムダ取り・改善 |
作業測定 | ・時間分析・稼働分析 | 作業時間やを測定し、生産計画や工程の改善、製造原価に基づく見積もりに活用 |
組み合わせ手法 | ・ラインバランス分析・連合作業分析・レイアウト分析 | 生産ライン内の負荷均等化、複数人や人と設備の連合作業の効率化、工場レイアウト効率化 |
上記のうち、工程分析・動作分析・運搬分析・時間分析・稼動分析・ラインバランス分析・連合作業分析の7つの手法を「IE 7つ道具」と呼びます。
方法研究
方法研究は、最も良い方法を追及するための手法で、仕事全体の流れや個別の動作を改善する際に活用します。
方法研究では、仕事や作業の各ステップを細かく分解し、不要な作業や動作を排除することで、無駄を削減します。方法研究に含まれる分析手法の例として、工程分析、動作分析、運搬分析があります。
工程分析
工程分析は、製品や部品の製造工程や作業工程を詳しく調査し、一定の記号で図表化することで各工程での無駄や問題点を発見する手法です。工程分析を行うことで、作業全体の流れや手順の全体像を明確にすることができます。
例えば、重複する工程の統合や不要な工程の削減により、効率的な生産ラインを構築できます。工程分析は、さらに単純工程分析、詳細工程分析、運搬経路分析などに分けられます。
工程分析の具体的手法
- 単純工程分析:各工程を大まかに把握し、作業の流れや順序を視覚化する手法
- 詳細工程分析:単純工程分析よりもさらに細かいレベルで各作業を分析する手法
- 運搬経路分析:材料や製品の運搬経路を最適化するための手法
動作分析
動作分析は、作業者の動きや姿勢、使用する道具などを詳細に観察・分析し、無駄な動作を省くための手法です。効率的な作業方法や動作の改善を行い、作業者の負担を軽減すると同時に、生産性の向上を図ります。動作研究では、動きのムダ、楽な作業への変更、動作の違いによる時間の差という観点で作業改善を行います。
動作分析は、大きく両手作業分析と微動作分析に分かれます。
動作分析の具体的手法
- 両手作業分析:作業者が両手をどのように使っているかを観察・記録し、効率的に動作しているかを確認する手法
- 微動作分析:作業者の小さな動作や動きの細部までを記録し、より詳細に分析する手法
運搬分析
運搬分析は、資材や製品の移動や保管の過程を検討し、付加価値を生まない無駄な運搬を削減するために行う分析です。マテリアル・ハンドリング分析、またはマテハン分析とも呼びます。
運搬分析により、工程内、工程間での運搬距離の短縮や効率的なレイアウトの提案が可能となり、作業効率が向上します。特に、大規模な製造現場においては、運搬にかかる時間やコストの削減が生産全体の効率に大きく影響します。
運搬分析は運搬工程分析、運搬活性分析、空運搬分析、運搬稼働分析、運搬重量比率分析、運搬原価分析などに分けられます。
運搬分析の具体的手法
- 運搬工程分析:物や材料が運搬される工程全体を分析し、運搬の流れや効率を把握する手法
- 運搬活性分析:運搬活動の頻度や稼働時間を分析する手法
- 空運搬分析:荷物を運ばない「空運搬」の頻度や時間を分析し、無駄な運搬を減らすための手法
- 運搬稼働分析:運搬機器や作業者の稼働状況を分析し、どの程度の稼働率で作業しているかを把握する手法
- 運搬重量比率分析:運搬物の重量の比率を分析する手法
- 運搬原価分析:運搬にかかるコストを分析する手法
作業測定
作業測定は、作業時間を定量的に測定するための手法です。作業の標準時間を明確にすることで、生産計画の立案や工程の改善、見積の作成などに役立ちます。
また、作業者の負担を適切に評価し、過度な労働を防ぐための基準としても有効です。作業測定に含まれる分析手法の例として、時間分析と稼働分析があります。
時間分析
時間分析は、作業の各ステップにかかる時間を計測・分析し、効率化の余地を探る手法です。具体的には、ストップウォッチや動画などを用いて各工程の所要時間を細かく記録し、無駄な時間や改善点を特定します。手軽に導入しやすいことから、実践したことがある企業が多い分析方法の一つです。
時間分析より、適切な標準時間を設定し、作業のばらつきを抑えることが可能になります。時間分析には大きく分けてストップウォッチ法とVTR法があります。
時間分析の具体的な手法
- ストップウォッチ法:作業時間を計測するためにストップウォッチを使用し、各作業の所要時間を測定する手法
- VTR法:ビデオカメラを使って作業の様子を撮影し、後で再生しながら分析する手法
稼働分析
稼働分析は、作業者や機械の稼働状況を観察し、稼働率や非稼働時間を把握する手法です。この分析では、作業時間と休憩時間、待機時間を詳細に記録し、効率的な稼働計画を立案します。
稼働分析によりコスト削減にも繋がり、リソースを有効活用できます。稼働分析には連続観測法、ワークサンプリング法、セルフタイムスタディ法があります。
稼働分析の具体的な手法
- 連続観測法:作業を連続して観察しながら記録する手法
- ワークサンプリング法:一定の時間間隔でランダムに観測することで、作業の稼働率や無駄の割合を推定する手法
- セルフタイムスタディ法:作業者自身が自分の作業時間を記録し、効率や無駄を分析する手法
組み合わせ手法
組み合わせ手法は、方法研究と作業測定を組み合わせた手法です。組み合わせ手法の例として、ラインバランス分析、連合作業分析、レイアウト分析があります。
ラインバランス分析
ラインバランス分析は、生産ライン内での作業負荷を均等化するための手法です。
各作業ステーションの処理時間を調整し、ボトルネックを解消することで、全体の生産効率を向上させます。作業者や機械の稼働率を最大限に高め、待機時間や無駄を削減することが目的です。生産性向上とコスト削減の両方を実現する重要な分析方法です。
連合作業分析
連合作業分析は、複数の作業者や機械が共同で行う作業(=連合作業)の効率を向上させるための手法です。各作業の連携やタイミングを最適化し、作業者同士や機械間の無駄を削減します。
連合作業分析により、作業の重複や待機時間を防ぎ、よりスムーズな生産フローを構築します。特にチームでの作業効率向上や生産ラインの調整に役立つ手法です。
レイアウト分析
レイアウト分析は、生産現場や設備の配置を最適化することで、作業効率を高める手法です。設備や作業スペースの位置を工夫し、運搬距離を短縮し、作業者の動線を効率化します。
レイアウト分析により、無駄な移動時間や労力を削減し、全体の作業効率を向上させることが可能です。適切なレイアウトは、生産性向上に大きな影響を与えます。
IEの導入手順
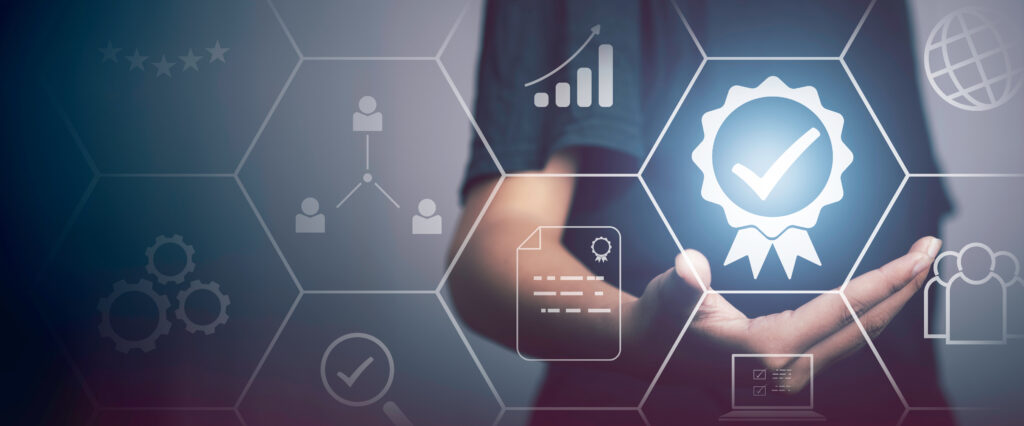
IEの導入には、計画的かつ段階的なアプローチが必要です。現場の現状を正確に把握し、目標を設定したうえで具体的な改善計画を策定し、実際の導入を進めることが重要です。
ここでは、IEの導入手順について解説します。
現状分析と目標設定
IE導入の最初のステップは、現状の作業プロセスや設備の稼働状況を詳細に分析することです。作業時間、工程の流れ、不良率などの定量データの収集や、現場の課題やボトルネックを明確にし、IE導入によって達成したい目標を設定します。
目標は具体的で測定可能なものであることが望ましく、例えば「特定の製品の生産効率を10%向上させる」などの具体的な数値目標が適しています。
改善計画の策定
目標が定まった後は、具体的な改善計画を策定します。改善計画は、IEの各種手法(標準時間の設定、レイアウト変更、作業動作の改善など)を活用し、段階的に実施できるように分割して進行します。
また、関係者間での意見交換やフィードバックを通じて、計画の現実性や実行可能性を確認します。計画段階での課題抽出とリスク評価を行い、計画に柔軟性を持たせることで、導入をスムーズに進行できます。
実施と導入
改善計画に基づき、実際の現場でIE手法の導入を行います。新しい工程や作業方法が現場に馴染むまでには、一定の時間がかかるため、従業員のトレーニングも含めた準備が必要です。さらに、導入後の進捗状況をモニタリングし、問題が生じた場合はすぐに対応する体制を整えることが重要です。
導入を段階的に進めることで、現場への負担を軽減しながら効率的な改善が期待できます。
導入後の効果検証
IEの導入が完了した後は、計画通りの効果が得られているかを検証します。導入前に設定した目標と実際の成果を比較し、達成度を測定します。
さらに、必要に応じて改善が効果を発揮している部分と、さらなる改善が必要な部分を分析することで、継続的な改善活動の土台を築くことができます。効果検証は、IE導入の成果を関係者に示すために非常に重要です。
継続的な改善活動の推進
IEは導入すれば完了ではなく、継続的な改善活動を行うことが重要です。改善活動を継続することで、作業効率の維持・向上が可能となります。
PDCAサイクルを回し、定期的な見直しを行いながら、現場と経営層の協力体制を確立することが重要です。継続的な改善文化が定着すれば、IE導入の効果を長期的に維持できます。
生産管理におけるIE導入のメリット
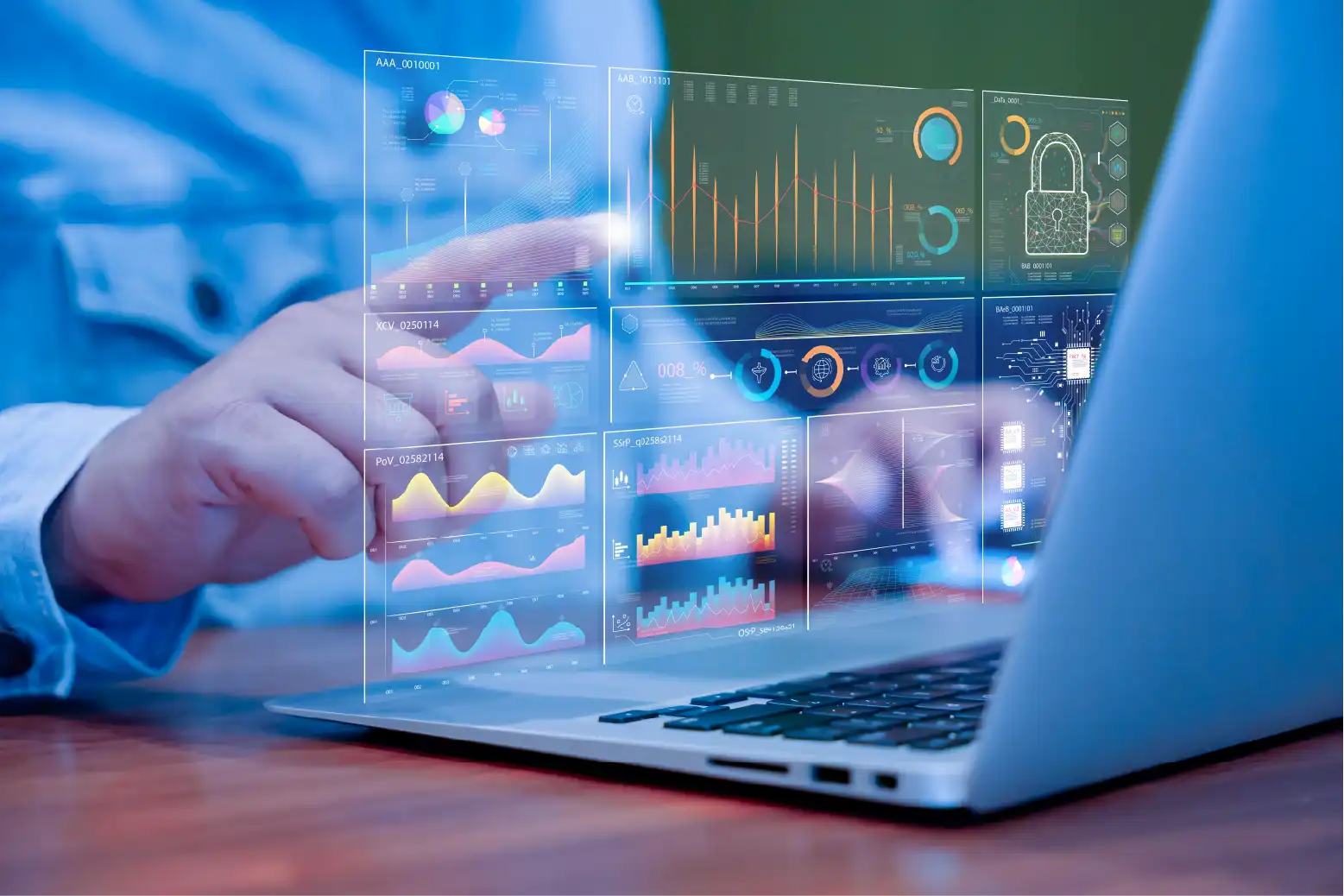
生産管理においてIEを導入することでさまざまなメリットが得られます。生産管理の主な目的は、効率的な生産計画の策定と生産工程の管理ですが、IEの導入により、作業の無駄を減らし、リソースを効率的に使用するための基盤が整います。
従来の生産管理においては、単純な生産計画や工程管理が主流でした。しかし、20世紀初頭の産業革命から「生産性向上」や品質管理の重要性が高まり、解決策の一つとしてIEが注目されるようになりました。近年は、生産管理においてIEを活用し、生産効率向上を追求する企業が多くなっています。
また、IEは品質管理や在庫管理、設備保全の分野でも活用されています。これらもIE活用で効率化することで、生産全体の業務改善が期待できます。
生産管理においてIEを導入する、具体的なメリットは以下5点です。
生産性が向上する
IEを導入することで、作業手順の見直しや工程の効率化が可能となり、生産性が向上します。例えば、ストップウォッチ法やワークサンプリング法を用いて作業時間を正確に測定し、無駄な動作を削減することで、作業のスピードアップが図れます。
また、両手作業分析を通じて、作業者の動作が効率よく行われるように設計し直すことで、全体の生産性が改善されます。これにより、製品の納期短縮やコスト削減が実現でき、顧客満足度向上にもつながります。
品質が安定化する
IE導入により品質の安定化も図れます。例えば、VTR法を用いて作業の動作を録画・分析することで、標準的な作業手順を確立できます。標準化により作業者ごとのバラつきが減り、不良品の発生を抑制することができます。
また、運搬経路分析を用いて製品や部品を正しく保管し、丁寧に運ばれるように管理することでも、品質の安定が実現します。
労働環境が改善する
IEの導入は、労働環境の改善にも役立ちます。例えば、動作分析を用いることで、作業者の動作や姿勢を改善し、身体的負担を軽減できます。両手作業分析により、両手を効率的に使えるように作業場を整えることで、自然な姿勢で作業でき、疲労が軽減されます。
また、運搬経路分析で無駄な移動を省くことで、作業者の負担を減らし、より快適な作業環境を実現できます。こうした環境改善は従業員の士気を高め、結果的に生産性向上にもつながります。
柔軟な生産体制が構築できる
IE導入で生産工程の見える化が実現すると、柔軟な生産体制の構築にも役立ちます。例えば、連合作業分析を用いることで複数の作業者が効率的に連携できる作業工程を設計し、急な生産量の増加にも対応可能な体制が整えられます。
また、稼働分析を用いて設備や作業者の稼働率を把握することで、生産ラインの調整がしやすくなります。これにより、季節的な需要変動や予期せぬ生産計画の変更にも即応できる生産体制が構築できます。
データに基づいた意思決定ができるようになる
IEの導入により、データに基づく意思決定が可能になります。たとえば、ワークサンプリング法や稼働分析で得られたデータをもとに、生産工程のボトルネックや改善点を客観的に評価できます。
これにより、経験や直感だけでなく、データに基づいた精度の高い意思決定が可能になります。また、改善計画の効果を数値で把握し、適切な判断を下すことで、生産現場全体の効率化や品質向上を実現できます。
IEを導入する際の課題
IEの導入には多くの利点がある一方で、多くの企業が抱える課題もあります。事前に課題を認識し、対応策を講じることが重要です。ここではIEを導入する際の課題について解説します。
現場からの抵抗がある
IEの導入は、現場の従業員にとって新しい作業方法やプロセスを伴うため、抵抗が生じることが少なくありません。従業員が現場の変化に対して不安を感じないよう、導入前にIEのメリットや目的を丁寧に説明し、納得を得るプロセスが重要です。
特に、現場リーダーや中間管理職との信頼関係の構築が、現場からの抵抗を軽減するための有効な手段となります。
費用対効果が見えにくい
IE導入に伴うコストや労力が明確である一方で、その効果がすぐに目に見えないケースもあります。特に短期的な視点では効果を測定しにくいため、長期的な視野での費用対効果の把握が重要です。
コスト管理システムやKPIの設定により、導入による具体的な効果を視覚化し、関係者にその価値を伝えることが重要です。
スキルや知識が必要になる
IEを効果的に活用するには、一定の知識や経験が必要となります。特に、人的リソースが少ない中小企業では、導入段階でこれらのスキル不足が課題となる場合があります。その場合、外部コンサルタントの導入や従業員教育を行うことが有効です。
最終的には、社内においてIEに関する知識を持った担当者を育成し、各部門で活用できる体制を整えると、長期的な視点での課題解決に繋がります。
正確なデータ収集が必要になる
IE導入には、現場の詳細なデータが必要となり、正確で信頼性のあるデータの収集が求められます。データが不十分な場合、分析や改善計画に偏りが生じ、期待する効果を得られない可能性があります。
データの収集方法や頻度を計画的に設計し、継続的にデータの正確性を保つための体制を構築することが重要です。
継続的な改善文化の定着が重要
IEは一度の導入で完了するものではなく、持続的な改善を目指すためのフレームワークです。そのため、改善活動が継続的に行われる文化を社内に定着させることが重要です。
従業員一人ひとりが改善活動に積極的に参加できる環境を整備することで、IE導入を長期的に成功させることができます。
IE導入を成功させる方法
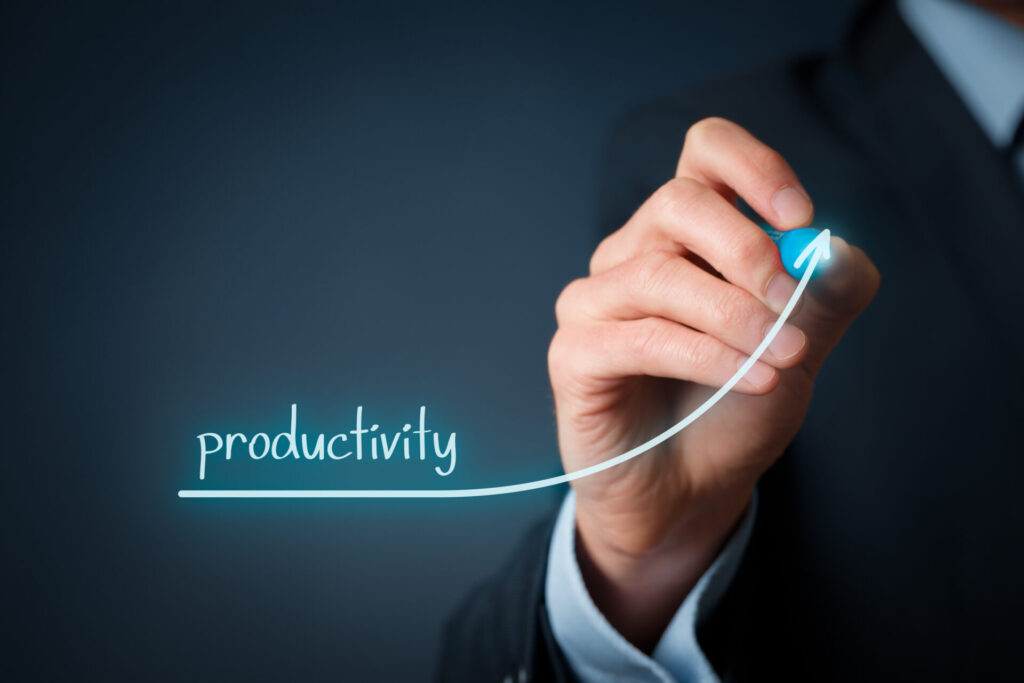
IE導入を成功させるためには、現場と経営層の協力が不可欠です。現場とのコミュニケーションを密にし、段階的に導入を進め、投資対効果を明確化しながら、スキル向上のための教育を行うことで、円滑に導入を進めることが可能です。
現場とのコミュニケーション強化
現場の従業員がIE導入に対して理解を深め、協力的な姿勢を持つことが重要です。導入の目的やメリットを丁寧に説明し、現場の意見を積極的に取り入れることで、信頼関係を築きます。
定期的なミーティングやフィードバックの場を設け、現場とのコミュニケーションを強化することで、導入プロセスがスムーズに進みます。
段階的な導入
IEの導入は一度に大きな変化を求めるのではなく、小規模な改善から段階的に進めることが望ましいです。現場に過度な負担をかけずに改善を進められ、成功事例を積み重ねられるため、従業員の理解と納得を得やすくなります。
また、段階的な導入により、導入の効果を検証しながら進めることが可能です。
投資対効果の明確化
IE導入に伴う投資と、それによって得られる効果を明確にすることで、経営層や現場の理解を得やすくなります。費用対効果を具体的な数値で示し、期待される効果を可視化することで、関係者の協力を得ることが容易になります。
ROI(投資収益率)やKPIを設定し、導入効果を定量的に示すことが重要です。
スキル向上のための教育
IEの導入には、従業員のスキルや知識が重要な要素となります。現場でのIE手法の活用には、専門的な知識や技術が求められるため、必要に応じて研修や教育プログラムを提供し、スキル向上を支援することが重要です。
IEに関する教育を通じて、全従業員が改善活動に積極的に参加できるようにしましょう。
データ収集のシステム化
正確で効率的なデータ収集は、IEの導入において不可欠です。現場のデータを自動的に収集・管理するシステムを導入することで、改善活動の効果を正確に把握できます。
データ収集のシステム化により、データの信頼性が向上し、改善計画の精度も高まります。
改善効果の可視化
IE導入によって得られた改善効果を視覚化することで、関係者が成果を共有しやすくなります。改善活動によってどのような効果が得られたかを具体的に示すことで、現場のモチベーションが向上し、継続的な改善活動が推進されやすくなります。
改善の成果を数値化し、報告書やグラフなどで表現することが効果的です。
IE分析と業務改善に生産管理システムが役立つ
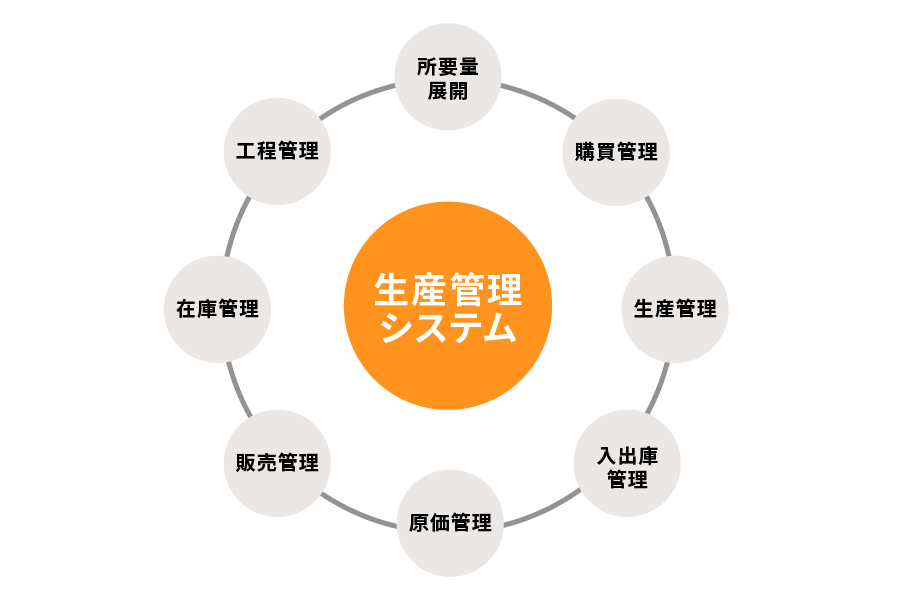
IEは数値を用いて工学的に改善活動を行うことを目的としていますが、そのためには現状を正しく把握することが最も重要です。日々の受発注情報や在庫状況、設備の稼働状況などをデータとして把握するためには、生産管理システムの導入がおすすめです。
製造業において、紙やエクセル手入力などで生産管理を行っている企業が少なくありません。これらのアナログな管理には、以下のデメリットがあり、IE活用を難しくするケースが多くあります。
- ヒューマンエラーが起きやすく、正確なデータが取りにくい
- 分析のためのデータ集計が別途必要
中小・中堅企業でよくある例が、紙の作業日報から工数集計するケースです。日々記録する作業日報をまとめると、各工程ごとの工数を把握できますが、そのためには紙の作業日報をエクセルなどに手入力する必要があります。入力ミスが起きやすいうえに、入力の手間が膨大となり、担当者へ大きな負荷がかかります。
生産管理システムを活用すると、システム上で作業開始・終了を登録するだけで、作業時間を自動集計できます。作業者ごとや工程ごとの工数データも簡単に参照できるため、わざわざIE分析のためにデータを集計する手間を大幅に削減できます。製造現場の各作業者も、作業開始・終了時に簡単な登録作業をするだけでよくなるので、手書きの手間が減らせます。結果的に、生産管理システムの導入そのものが、業務改善につながると言えます。
参考事例:手書き&エクセル入力がゼロに。1人の省人効果+迅速な生産調整で生産性向上
22種類の生産管理システムをランキングで比較
初期費用相場や選び方のポイントをチェック
生産管理システムをそれぞれの特徴や初期費用相場などで比較したい場合は、「生産管理システムランキング」も是非ご覧ください。生産管理システムは、自社の製品・生産方式・企業規模などに適したものを導入しないと、得られるメリットが限定されてしまいます。事前適合性チェックや生産管理システムを選ぶ前に押さえておきたいポイントも解説していますので、製品選びの参考にしてみてください。