歩留まりとは 歩留まり率を改善する具体的方法、良品率との違い、重要性まで解説
公開日:2024年08月22日
最終更新日:2024年09月26日

製造業における「歩留まり」とは、投入された素材や部品が最終的に製品として使用可能な割合を示す指標です。歩留まり率が高ければ、無駄が少なく効率的な生産が行われていることを意味し、逆に低ければコスト増加や品質低下の原因となります。本記事では、歩留まりの基本概念から、類似する用語との違い、歩留まり改善の具体的な方法までを解説します。
歩留まりとは
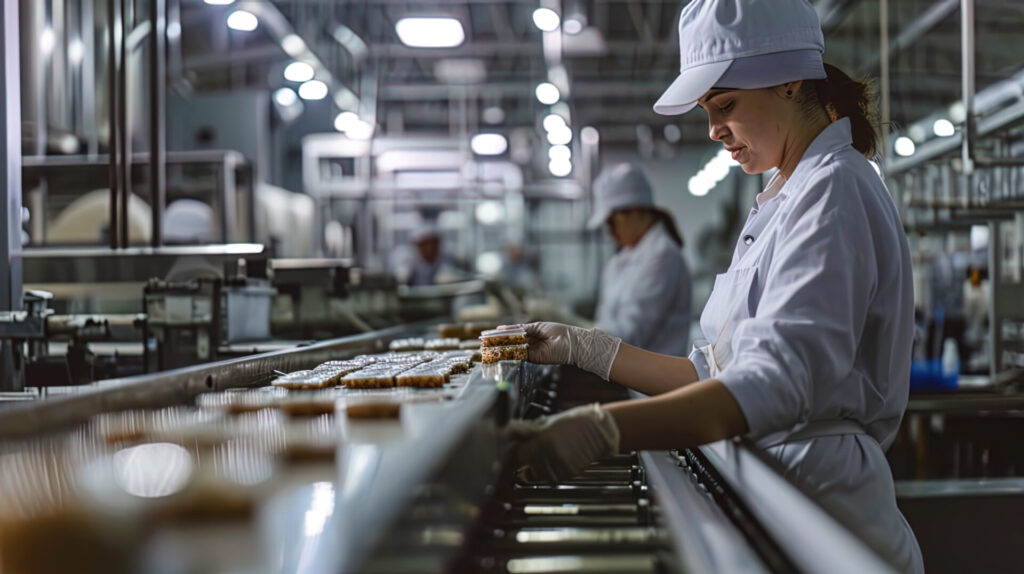
製造業における歩留まり(読み方:ぶどまり)とは、製造工程で投入された素材や部品のうち、最終的に使用可能な製品として出荷される割合を示します。製造業において生産効率を評価するための重要な指標の一つです。歩留まりは、製品の品質管理やコスト管理の面で、重要な役割を果たします。
歩留まりの語源
歩留まりという言葉は、日本語の「歩(ぶ)」と「留まり(とどまり)」に由来しています。「歩」は「歩合」から来ており、歩合とは割合を表す言葉です。ここでは完成品の割合を示し、完成品が「留まる」割合、つまり、製造の成果を評価する概念として用いられるようになりました。元々は漁業や農業の分野で使用されていた言葉が、製造業でも適用されるようになり、現在では製造業だけでなく幅広い業界で使われています。
歩留まり率の使い方
歩留まり率を使うシーンは、大きく分けて2通りあります。
製造の効率や品質を把握する
歩留まりを計算することで、効率よく製造できているかどうかを把握できます。歩留まり率が高いということは、製造ロスが少なく、製造工程が効率的であることを意味します。逆に、歩留まり率が低い場合は、材料のロスが多く、コストが増大する可能性があるため、改善が必要となります。
原材料費や数量を試算する
歩留まりを事前に把握しておくと、必要な材料費や数量が計算できます。歩留まり率は100%に近い方が望ましい、つまり材料をちょうど使い切れるのが理想ですが、実際には歩留まり率が100%になることはほぼありません。つまり、原材料の発注時に歩留まりを考慮した数量に調整することが、現実的な原材料コストを抑える方法となります。
歩留まり率と似た用語との違い
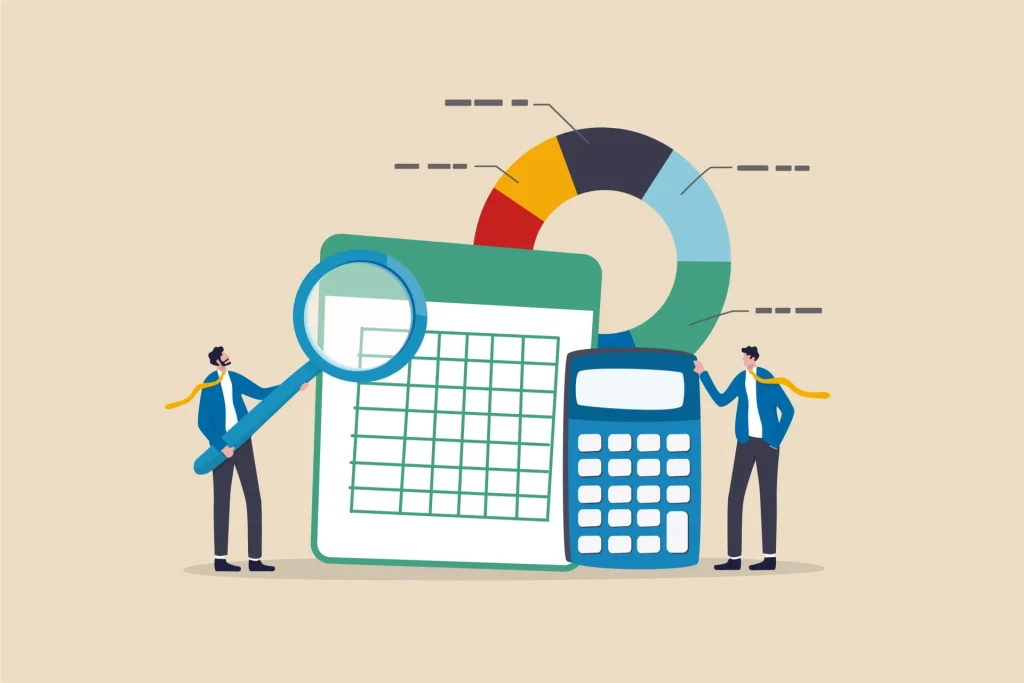
歩留まり率に似た用語には、良品率や直行率などさまざまあり、それぞれ異なる側面から生産効率や品質を評価します。これらの用語を正しく理解することで、製造プロセスの改善に向けた具体的な対策が可能になります。
良品率
良品率とは、製造過程で生産された製品のうち、基準を満たして良品と認められた製品の割合を指します。歩留まり率と同義で使う場合もありますが、良品率はあくまで「完成品」の品質に焦点を当てています。一方、歩留まり率は「原材料」の使用効率を示します。
良品率と合わせて、よく使われる言葉は「直行率」「手直し率」「不良率」です。
直行率・手直し率・不良率
「直行率」は、製造工程で一度も手直しや再加工を行わずに、最終的に出荷できる製品の割合を示します。直行率が高ければ、製造ラインは効率的で無駄が少なく、手直しに伴う追加コストが抑えられていることを意味します。
一方、製造過程で不良品となったものの、再加工などの手直しにより良品となる製品もあるかと思います。この手直しにて良品になる割合を「手直し率」と呼びます。「良品率」は、この手直し品も含みますが、直行率は手直しなしに完成した製品のみをカウントします。
例:ある製品を100個製造し、90個が手直しなしで完成+5個が手直しにより良品となった場合
- 直行率:90%
- 手直し率:5%
- 良品率:95%(歩留まり95%ともいえる)
上記の場合、不良品となった割合を示す「不良率」の考え方は2通りあります。手直しが発生した製品も不良品とみなす場合は、不良率は10%となります。最終的に良品とならなかった製品のみを不良品とすると、不良率は5%となります。
転用率
転用率は、不良品や余剰生産品を、別の用途や製品に再利用できる割合を指します。転用率が高い場合、製造プロセスで発生する無駄をうまく活用できていることを示します。歩留まり率と転用率を合わせて考慮することで、製造プロセス全体の資源効率をより詳細に分析することが可能になります。
歩留まり改善の重要性:2大メリット
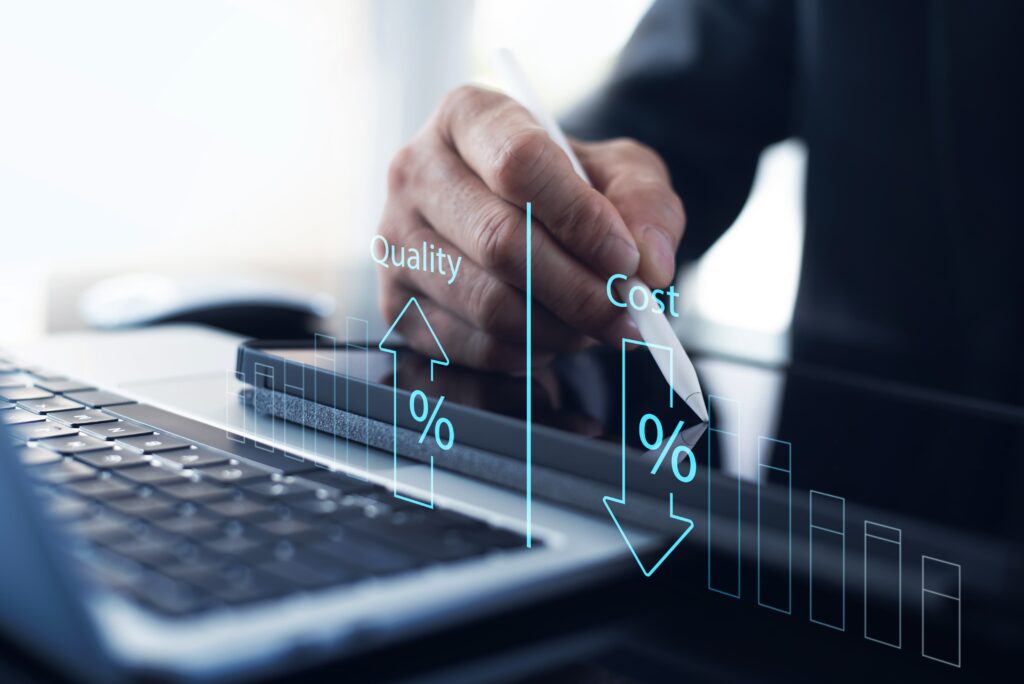
歩留まり改善は、製造業において極めて重要な課題であり、その成功はコスト削減や品質向上に直結します。ここでは、歩留まり改善の二つの大きなメリットについて詳しく説明します。
コスト削減による利益率向上
歩留まりを改善することで、原材料の無駄を削減し、製造コストを低減することができます。これにより、製品あたりの利益率が向上し、企業全体の収益性が改善されます。
品質向上
歩留まりの改善は、製品品質の向上にも寄与します。歩留まり率が改善されると、不良率も下がるため、不良品数も減少します。結果として、顧客に提供される製品の品質が安定し、顧客満足度やブランドの信頼性の向上にもつながります。
歩留まり率の計算方法
歩留まり率の計算は、製造において投入された素材や部品のうち、最終的に使用可能な製品として完成した割合を百分率で表します。計算式は次の通りです。
歩留まり率(%)=(良品数 ÷ 使用した原材料数)✕ 100
この計算により、製造ラインの効率や無駄を定量的に評価することができ、改善の必要性を明確にすることができます。
なぜ歩留まり改善は難しいのか
歩留まりの改善は、製造業において重要であると同時に、実際には非常に難しい課題です。その理由の一つは、歩留まり低下の要因が多岐に渡るからです。例えば、機械の性能、材料の品質、作業者の技術レベル、環境条件など、さまざまな要因が歩留まりに影響を与えます。さらに、これらの要因が常に変動するため、問題の根本原因を特定し、安定的に改善することが困難です。
逆に、原因さえわかれば、歩留まり改善のための方法は明確になります。機械の性能が悪いのであれば修理をすべきですし、材料の品質に問題があるのであれば入荷検品強化・サプライヤー再選定などが可能です。
歩留まり率が悪い原因を見つける方法
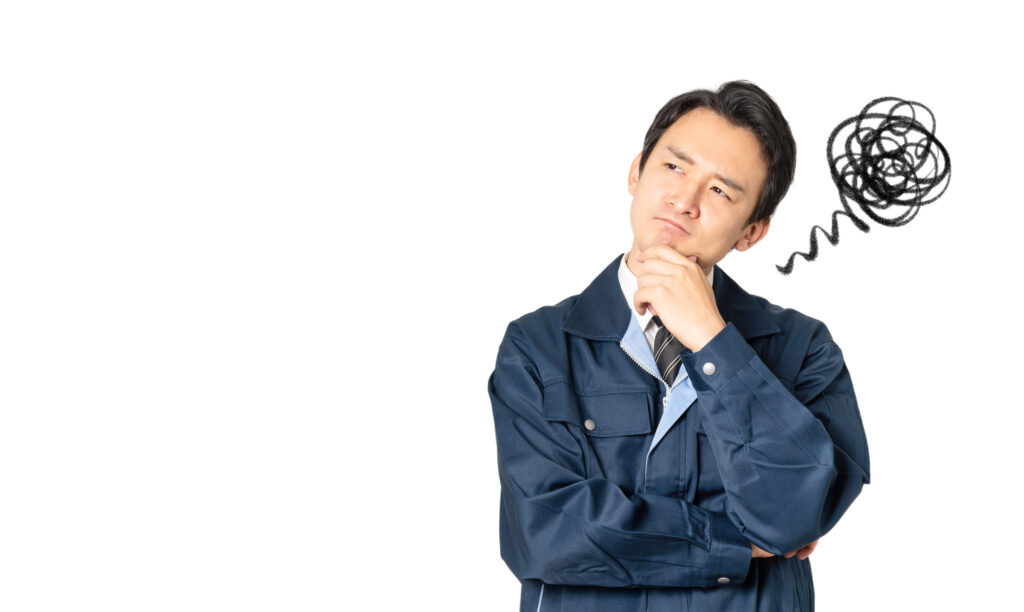
歩留まり率が低下した場合、その原因を迅速に特定することが重要です。具体的な方法は主に3つあります。
不良発生を記録する
不良品が発生した際には、その都度、不良実績をすることが重要です。不良品の種類、発生時点、発生場所、作業者などの情報を記録することで、後に分析する際の基礎データとなります。不良データを蓄積することで初めて、頻発する不良品のパターンや傾向を分析できるようになります。
不良データ集計
記録された不良データを集計し、統計的に分析することで、問題の根本原因を特定する手がかりを得られます。例えば、どの工程で不良が多発しているか、特定の材料や機械に問題が集中していないかを確認することができます。不良データを視覚化することで、問題点がより明確になり、改善策を立案しやすくなります。
「5M + 1E」に基づく分析
「5M + 1E」とは、製造業でよく用いられる問題分析のカテゴリです。以下の5M+1Eの要素に分解して、不良を分析することで、原因を突き止めやすくなります。
■5M
- Man(人)
- Machine(機械)
- Material(材料)
- Method(方法)
- Measurement(測定)
■1E
- Environment(環境)
上記のどこに原因があるか分析する際は、なぜなぜ分析などのフレームワークを活用すると、真因を見つけやすくなります。
歩留まり率の具体的な改善方法
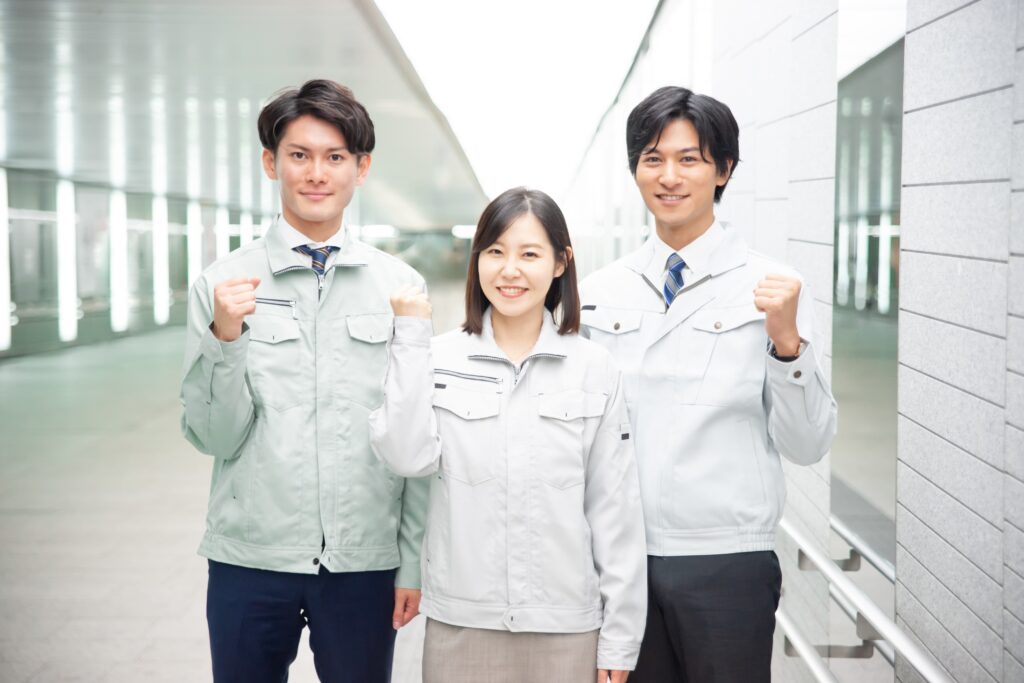
歩留まり率を改善するための具体的な対策は以下のとおりです。
機械・設備の最適化
設備が劣化すると不良品の発生率が上昇するため、機械の点検や更新が必要です。機械や設備のメンテナンスを定期的に行い、最適な状態で運用することで、歩留まり率の向上につながります。また、新しい技術や機械を導入することで、生産性や品質を向上させることも可能です。
入荷検品・品質検査体制の強化
原材料の時点で不良が発生している場合は、原材料の入荷検品や品質検査の強化が必要です。そのうえで、サプライヤーに不良対策を求めたり、場合によっては原材料の調達先を変更したりといった対策を検討します。
不良原材料を次工程に回さない体制を作ることで、製造に取り掛かってからの不良発覚により作り直しの手間が発生する事態を防止できます。
作業の標準化
作業手順を標準化することで、作業者によるバラツキを減少させることができます。標準作業手順書(SOP)を作成し、それに基づいて作業者を訓練することで、作業ミスの発生を抑え、品質の一貫性を保つことができます。また、作業標準化は、新人教育や作業者のスキルアップにも役立ちます。
作業者の教育
作業者のスキルや知識を向上させるための教育・訓練は、歩留まり率の改善において重要な役割を果たします。特に、新しい設備や技術の導入時には、作業者がその使用方法をしっかりと理解することが求められます。定期的なトレーニングや勉強会を通じて、作業者の能力を向上させることが重要です。
直行率向上に取り組む
直行率向上の施策を打つことで、手直しや再加工の手間を減らすと、全体的な品質向上や歩留まり改善につなげることができます。直行率を向上させるためには、製造工程の見直しや、作業手順の改善、さらに品質管理の強化が必要です。
製品設計の見直し
製品の設計段階で、製造工程の効率を考慮することも重要です。例えば、製品の設計をシンプルにすることで、製造が容易になり、歩留まり率の向上につながります。また、製造に適した材料の選定や、部品の設計変更も歩留まり率に大きな影響を与えることがあります。
不良データ分析には生産管理システムが役立つ
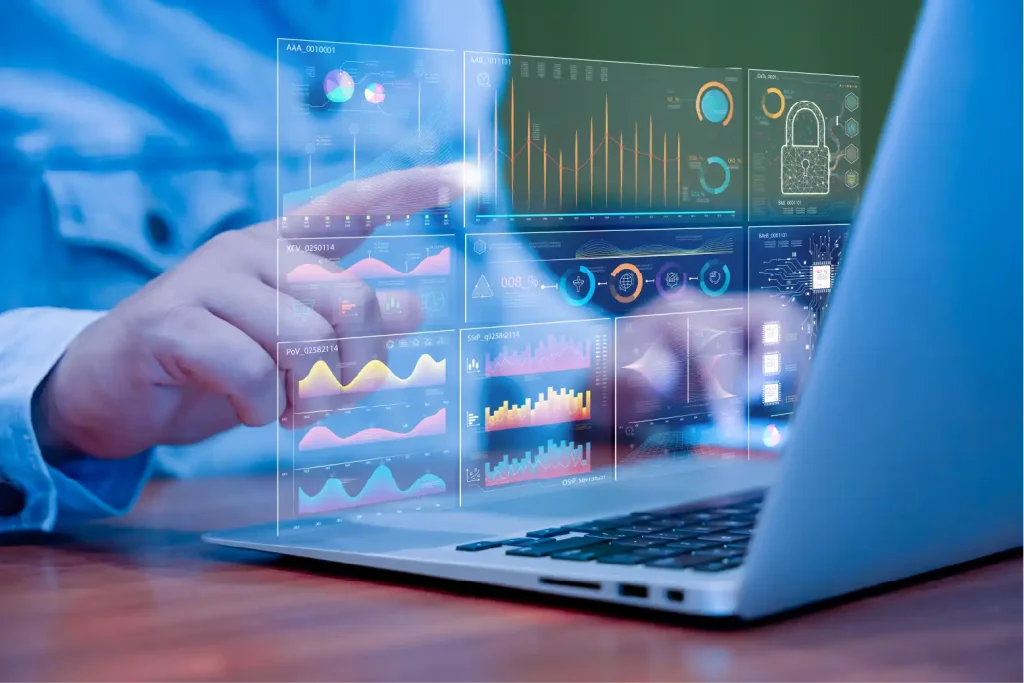
不良データを効率的に分析するためには、生産管理システムの活用が効果的です。生産工程を一元管理できる生産管理システムで、検査データもあわせて管理することで、工程ごとの不良データ収集が簡単にできるようになります。リアルタイムでのデータ分析も行うと、手書きやエクセル管理よりも早期の問題発見と迅速な対応が可能です。
例えば、作業日報を生産管理システム上で記録し、不良データもシステム内に蓄積していくと、直近で発生した不良がどの工程、どの設備、どの作業者のもとで発生したかを簡単に参照できます。また、発注管理も行うことで、どのサプライヤーからの原材料で不良が起きやすいかも見える化できます。
生産管理システムで品質傾向の分析を効率化した事例
あるロボット関連機器の製造企業は、従来手書きやエクセルで管理していた工程管理や検査管理を、生産管理システムに置き換えました。それにより、品質分析の手間を減らし、効率的な管理を実現しました。
同社は従来、紙の検査表からエクセルに情報を手入力し、傾向分析を行っていました。しかし、紙から各情報を拾い上げて転記する作業は、担当者の負担が大きいという課題がありました。生産管理システムを導入し、検査管理をデジタル化したことで、分析データをCSVダウンロードするだけで簡単に分析できるようになった。
詳細はこちら:
生産情報・検査情報を一元管理!手書き・エクセル作業をシステム化し、生産拡大時の品質リスク対策に成功
22種類の生産管理システムをランキングで比較
初期費用相場や選び方のポイントをチェック
生産管理システムをそれぞれの特徴や初期費用相場などで比較したい場合は、「生産管理システムランキング」も是非ご覧ください。生産管理システムは、自社の製品・生産方式・企業規模などに適したものを導入しないと、得られるメリットが限定されてしまいます。事前適合性チェックや生産管理システムを選ぶ前に押さえておきたいポイントも解説していますので、製品選びの参考にしてみてください。