「なぜなぜ分析」のやり方解説!不良発生・流出の原因を根本から解決 生産管理システムの導入方法も紹介
公開日:2024年06月27日
最終更新日:2024年10月02日
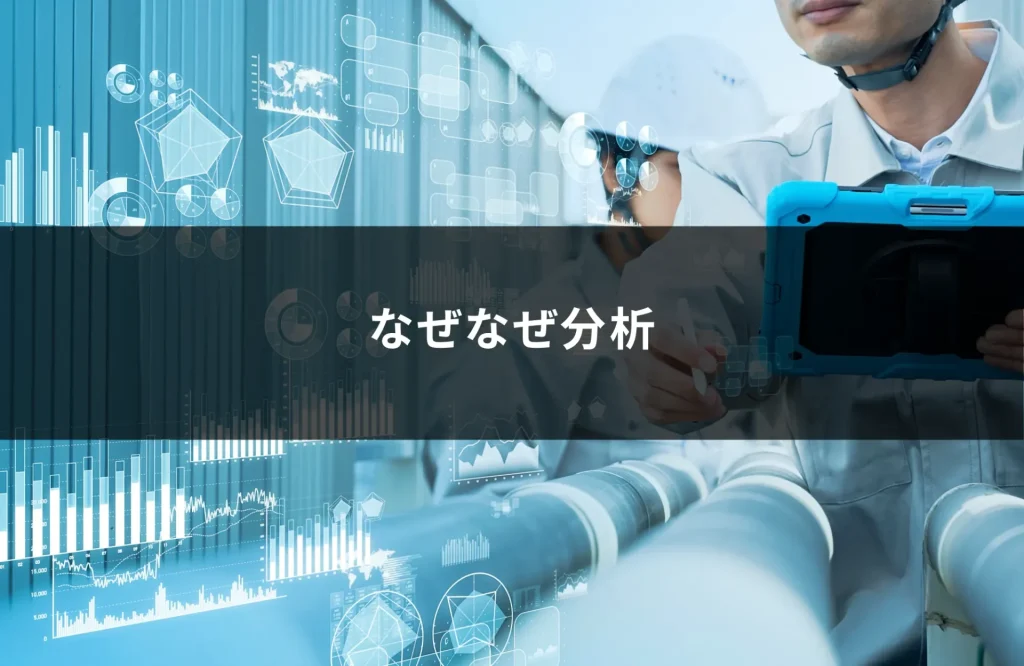
製造業における不良対策の手法である「なぜなぜ分析」。これは、問題の表面的な原因ではなく、根本的な原因を追求することで再発防止を図る分析方法です。この記事では、なぜなぜ分析の基本から具体的なやり方、不良発生時の活用方法、ポイントを解説します。また、なぜなぜ分析に必要な生産時の状況把握に役立つ、生産管理システムの導入方法や活用事例についても紹介します。
なぜなぜ分析とは
なぜなぜ分析は、不良発生時の根本的な原因を追求し、再発防止のために持続可能な解決策を見つける方法です。発生した不良に対し「なぜ」という質問を繰り返すフレームワークで、課題を深堀り、真因を突き止めます。これは製造業をはじめ、さまざまな業界で活用されています。
なぜなぜ分析の目的
なぜなぜ分析の目的は、問題の表面的な原因にとどまらず、根本的な原因を明らかにし、同じ問題が再発しないように持続可能な解決策を見つけることです。製造業では、不良品の発生原因を特定し、品質向上やコスト削減を可能にするためによく使われています。
なぜなぜ分析が重要な理由
なぜなぜ分析が重要な理由は、問題の根本原因を明らかにすることで、再発防止策に繋げられるからです。一般的に、なぜなぜ分析は「なぜ?」という問いかけを5回繰り返しますが、それだけ深掘りすることで、ようやく真因を突き止められると考えられています。
また、問題解決のためのコミュニケーションツールとして用いられることもあり、組織内の協力体制を強化することができます。チーム全体での問題解決能力と協力体制の強化が可能になります。
なぜなぜ分析の歴史と背景
なぜなぜ分析は、トヨタ自動車によるトヨタ生産方式(TPS)の一環として導入されました。トヨタ生産方式は、製造業における効率性と品質向上を目的としており、なぜなぜ分析はその中心的な手法として位置づけられています。TPSの成功により、なぜなぜ分析は他の業界や企業にも広がり、問題解決のための標準的な手法となりました。
なぜなぜ分析を不良発生時に活用する方法
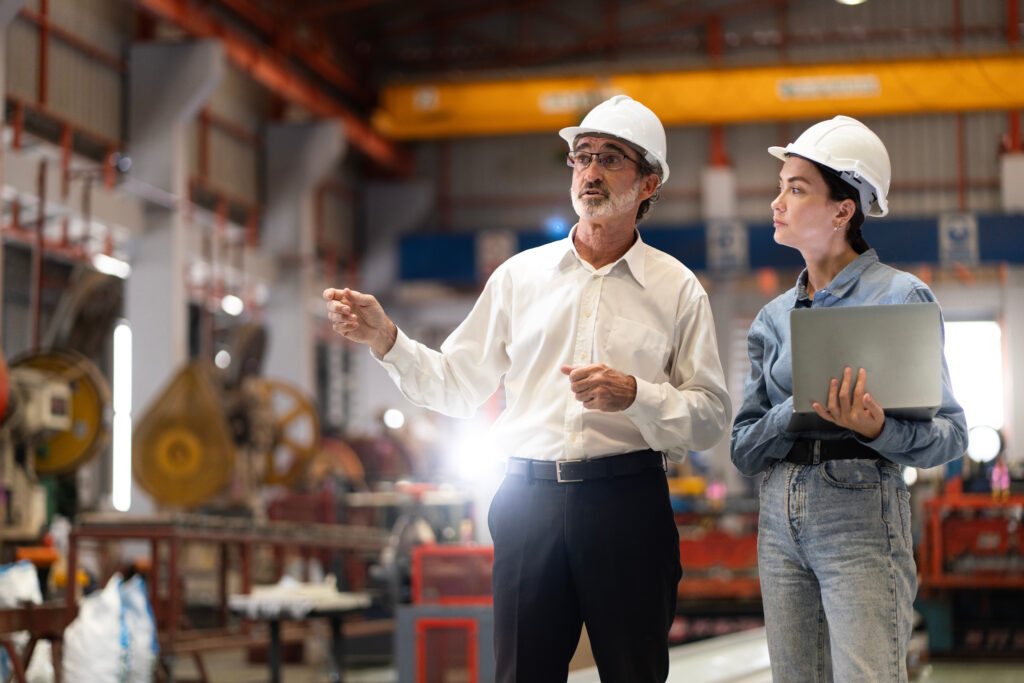
不良発生時には、なぜなぜ分析を活用して原因を徹底的に追求し、根本的な原因を突き止めることができます。これにより、同じ不良が再発することを防ぎ、製品の品質向上とコスト削減を図ります。不良の発生は、製品の信頼性やブランドイメージに直結するため、その原因を徹底的に追求することが求められます。
具体的な不良対策の手順
なぜなぜ分析を用いた、具体的な不良対策の手順は以下の通りです。
- 不良の発生状況の把握と問題定義
- 「なぜ?」を5回繰り返して原因を深掘る
- 具体的な解決策を検討・実行する
- 効果検証
なぜなぜ分析を効果的に行うためには、問題の定義から解決策の実行と検証までを適切に進めることが重要です。
不良の発生状況の把握と問題定義
まずは、不良の発生した場所、時間、作業者、詳しい状況などを把握し、問題を明確に定義することが必要です。初めに問題定義を明確に行うことで、その後のなぜなぜ分析がスムーズに進めやすくなります。
「なぜ?」を5回繰り返して原因を深掘る
上記で定義した不良の原因を「なぜ?」と繰り返して深掘りしていきます。「なぜこの不良が発生したのか?」という問いから始め、その答えに対してさらに「なぜ?」を繰り返すことで、本当の原因を把握することができます。トヨタ生産方式におけるなぜなぜ分析は、質問を5回繰り返します。
たとえば、期限切れの原料を使用してしまったという不良が発生したとします。期限切れ原料を使ってしまった理由がピッキングミスだとしたら、「なぜピッキングミスが起きた?」と問いかけます。ピッキングミスの原因が、期限切れの原料が倉庫に残っていたからなら、「なぜ期限切れ原料を破棄しなかった?」……のように、原因を深堀りし、真因を追求します。
具体的な解決策を検討・実行する
原因が特定できたら、その原因を解消するための具体的な解決策を考えます。この際、リソースや時間を考慮し、現実的で実行可能な方法を選ぶことが重要です。また、短期的な暫定対策だけでなく、長期的で持続的な恒久対策を考えることも重要です。
効果検証
考えた解決策を実行した後は、その効果を検証します。不良内容にもよりますが、対策後1〜3ヶ月後に効果検証するケースが多いです。必要に応じて、問題が再発しないよう追加の対策を考えることもあります。
なぜなぜ分析を行うコツ
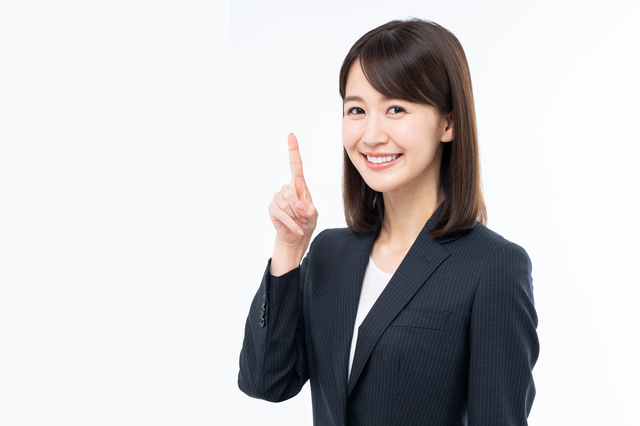
なぜなぜ分析を効果的に行うためには、いくつかのコツがあります。ここでは、問題の明確化から解決策の実行まで、成功するためのポイントを詳しく説明します。
問題の経緯や背景を把握する
問題が発生した背景や経緯などの詳細な情報を収集し、問題の発生状況を正確に把握することで、解決したい問題を具体的に特定します。問題が漠然としていると、分析が難しくなり、効果的な解決策を見つけることができません。
現場の状況を把握して分析する
現場の状況を正確に把握し、その上で分析を行うことが重要です。現場の状況を無視した分析は、実効性のある解決策を見つけることが難しくなります。現場での観察やデータ収集、現場の従業員からの意見を聞くことで、現場の状況を把握することができます。
客観的に分析する
感情に流されず、偏見や先入観を排除して客観的に問題を分析することが求められます。客観的な分析を行うためには、データや事実に基づいた情報を収集し、それに基づいて原因を特定することが重要です。
複数の要素をまとめない
一度に複数の要素を分析するのではなく、個々の要素をそれぞれ分析します。これにより、各要因の影響を正確に評価することができます。
連鎖的に分析する
問題の原因が複数存在し、それぞれの原因に関連がある場合は、連鎖的に分析します。連鎖的に分析するためには、全体像を把握した上で各原因を個別に分析し、それぞれの関連性を明確にすることが重要です。
実行可能な解決策を考える
考えた解決策が実行可能であるかを検討します。解決策を実行するためのリソースや時間を考慮し、現実的な範囲で実行できる方法を選び、無理のない計画を立てることが重要です。
例えば、毎月1000個生産する製品にて、不良品が見つかったとします。不良品の流出対策としては、抜き取り検査の数を増やす、全数検査をするなどの方法がありますが、1000個全数を検査するのは現実的ではありません。製造中に不良品を発見する仕組みを作るなど、実行できる対策を別の角度から考える必要があります。
「なぜ」と深掘る回数を5回にする必要はない
なぜなぜ分析において、「なぜ?」を繰り返す回数にこだわる必要はありません。「なぜ?」の問いかけを5回行っても真因にたどり着けない場合は、6回、7回と深堀りする場合もあります。重要なのは、「なぜ?」を繰り返す際に、1つ1つの回答が納得できるものであるかを確認することです。
業務に関わる全員で分析する
分析には、業務に関わる全員が参加することが重要です。品質管理担当者だけでなく、実際の製造担当者や検査担当者なども原因分析することで、問題の本質を理解しやすくなります。さらに、組織全体の問題解決能力、チーム全体のパフォーマンスが向上します。
従業員全員が実行できる解決策を考える
解決策は、現場の全員が実行できるものである必要があります。従業員の意見を取り入れ、リソースや時間が考慮された現場の状況にあった方法を選ぶことで、問題の再発を防ぐことができます。
原因を特定の個人に押し付けない
原因を特定の個人に押し付けることは避けるべきです。例えば、不良発生の原因を「新人の〇〇の不注意」と考え、個人への指導に留まってしまうと、対策内容が属人化し、別の新人がまた同じミスをしてしまう場合があります。また、組織全体の問題解決能力が低下する可能性もあります。問題の本質を見失わないために、個人ではなく、システムやプロセスに焦点を当てて分析することが重要です。
因果関係を明確にする
原因と結果の因果関係が明確になっているかを確認します。データや事実に基づいた情報を収集し、それに基づいて分析を行うことで、曖昧な関係ではなく、明確な因果関係を特定することができます。
なぜなぜ分析が上手くいかない時の注意点
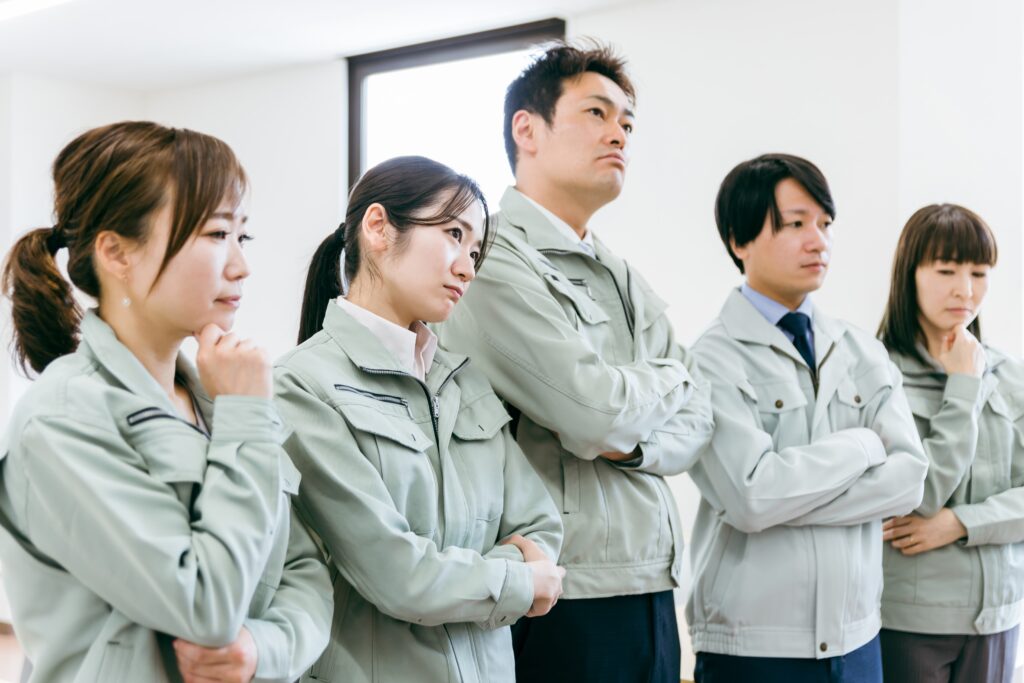
なぜなぜ分析が上手くいかない場合、以下の確認事項をチェックしてみてください。
- 解決したい問題が曖昧でないか
- 分析が感情的になっていないか
- 答えが曖昧になっていないか
- ただの推測になっていないか
- 個人の問題にしてしまっていないか
- 事実にもとづいているか
- 実行可能な解決策か
- 現場を想定しているか
「なぜなぜ分析」の使用事例
なぜなぜ分析は、さまざまな場面で効果的です。身近な場面から特定の業務に至るまで、実際の使用事例を紹介します。
身近な場面での使用例
日常生活や家庭内でも、なぜなぜ分析を活用することができます。例えば、子どもが宿題をしない理由を「なぜ?」と繰り返して追求し、根本原因を見つけて対策を考えることができます。
配送現場での使用例
配送業務において、不良品や遅延の原因をなぜなぜ分析で特定し、改善策を考えることができます。配送現場での使用例としては、遅延の原因を特定し、配送ルートの見直しや作業手順の改善を行うことで、遅延を防ぐことができます。
物流倉庫での使用例
物流倉庫では、在庫管理や出荷ミスの原因をなぜなぜ分析で追求します。物流倉庫での使用例としては、在庫の過不足やピッキングミスによる誤出荷の原因を特定し、在庫管理システムの導入や作業手順の見直しを行うことで、ミスを防ぐことができます。
業界別:製造業のなぜなぜ分析事例
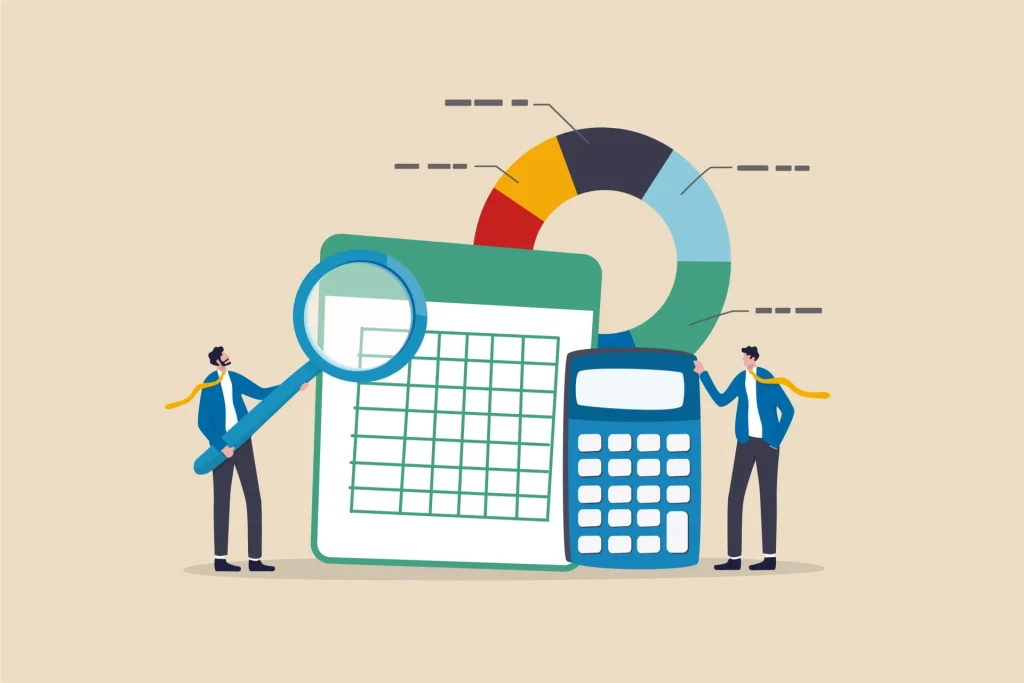
製造業向けのなぜなぜ分析を、業界別に紹介します。
金属加工:加工品の寸法不良
- なぜ寸法不良が起きた?→工作機械が寸法通りに加工できない状態だった
- なぜ寸法通り加工できなかった?→工作機械の校正不足で、誤差が生じていた
- なぜ校正ができていなかった?→校正が定期的に行われていなかった
- なぜ定期的な校正が行われていなかった?→校正スケジュールが明確に決まっていなかった
- なぜ校正スケジュールが決まっていなかった?→今まで加工不良が起きたことがなく、校正の重要性が認識されていなかった
ここから考えられる対策としては、工作機械の校正スケジュールの策定、それらを忘れずに実施するための設備管理システムの導入などが考えられます。
食品・医薬品・化粧品など:原料の誤使用
- なぜ原料を誤使用した?→類似原料と見間違って使用してしまった
- なぜ類似原料と見間違った?→見た目がほぼ同じ、かつ品番が1桁違いのため、目視確認で見誤った
- なぜ目視確認で見誤った?→新人作業者が類似原料の存在を知らず、似た品番と見た目のものを当該原料と思い込んでしまった
- なぜ思い込んでしまった?→見た目が酷似した類似原料があるにも関わらず識別の工夫がなく、類似原料の存在を知らないと見間違いやすい環境だった
- なぜ識別の工夫がなかった?→今まではベテラン従業員のみが当該原料を扱っており、誤使用したことがなかった
この場合、当該原料と類似原料を識別しやすくする対策が必要となります。すぐにできる措置としては、ラベルの色を変える、棚に「類似品あり・要注意」という表記を出すなどが挙げられます。
長期的にヒューマンエラーをなくし、誰でもミスを防止する方法としては、バーコード管理の導入が効果的です。原料使用時にバーコードを読み取り、指定原料と異なる場合はアラートが出るようにすることで、作業者の経験に問わず誤使用を防げます。
生産管理システムの活用方法
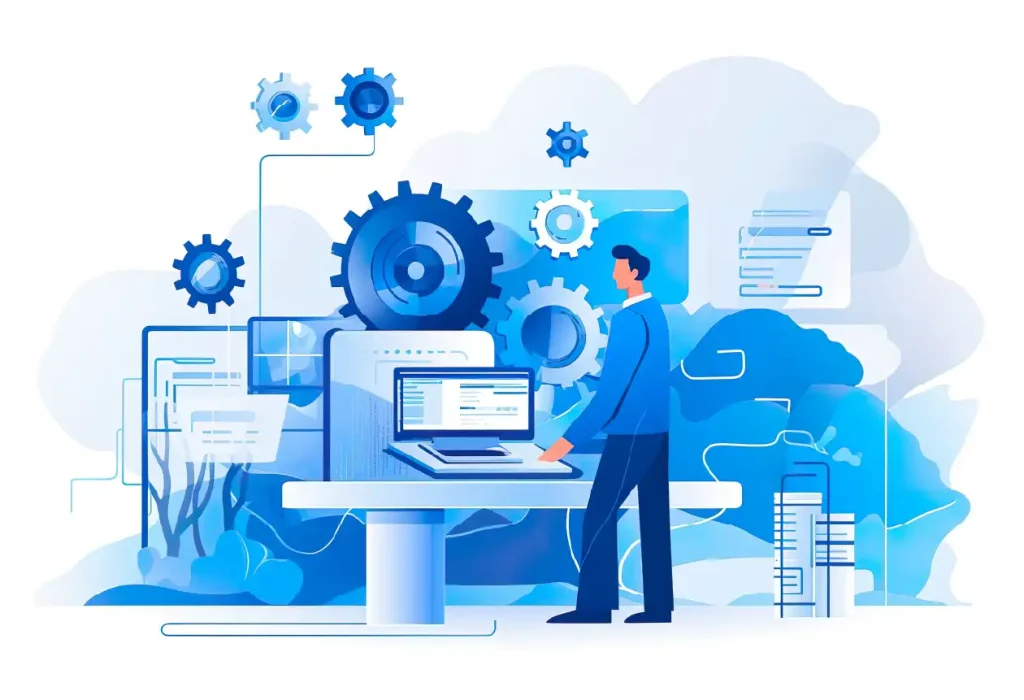
生産管理システムを活用することで、なぜなぜ分析を効率的に行うことができます。前述のバーコード管理と併用することで、ヒューマンエラー防止の効果も期待できます。
生産管理システムとは、生産プロセスを一元管理し、効率的な運用をサポートするツールです。在庫管理や工程管理、進捗管理、品質管理など、さまざまな機能があります。また、データ収集や分析の自動化により手間を省き、より正確な情報を得ることができます。
その1:生産プロセスの振り返り
なぜなぜ分析には、不良品が出た際の生産工程の把握が不可欠です。生産管理システムを活用することで、生産データの収集と分析が効率化できます。どの生産ラインで製造していたか、誰が作業していたかなど、生産データを一元管理することで、過去データの参照も容易になります。状況把握や作業の振り返りが効率的に行えるため、原因特定や有効な対策を迅速に考え、実行できます。
その2:バーコード管理によるヒューマンエラー防止
生産管理システムには、ハンディ端末などと連携することでバーコード管理ができるものがあります。バーコード管理により、製造時の工程飛ばしや原材料・部品の誤使用のエラーチェックをすることで、不良原因となったヒューマンエラーの防止が可能です。
22種類の生産管理システムをランキングで比較
初期費用相場や選び方のポイントをチェック
生産管理システムをそれぞれの特徴や初期費用相場などで比較したい場合は、「生産管理システムランキング」も是非ご覧ください。生産管理システムは、自社の製品・生産方式・企業規模などに適したものを導入しないと、得られるメリットが限定されてしまいます。事前適合性チェックや生産管理システムを選ぶ前に押さえておきたいポイントも解説していますので、製品選びの参考にしてみてください。