GMPにおけるバリデーションとは 医薬品や食品業界必須の品質管理の基本
公開日:2024年08月29日
最終更新日:2025年07月22日
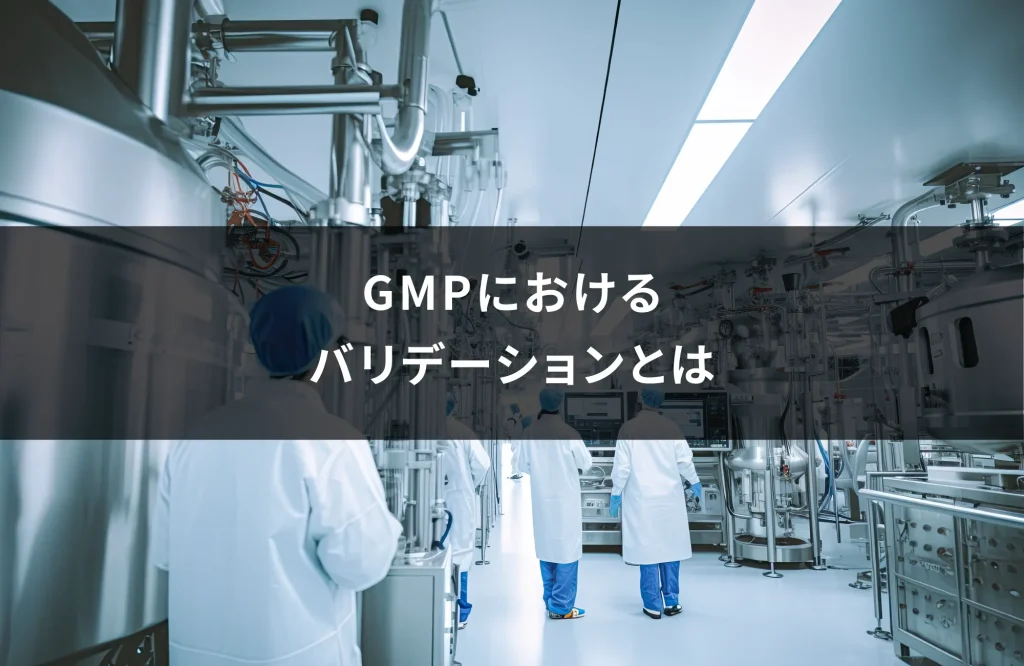
製造業における品質保証の観点から、バリデーションは非常に重要です。特に、医薬品や食品産業など、厳しい規制が求められる分野で重視されています。本記事では、GMPにおけるバリデーションとは何かについて詳しく解説します。
バリデーションとは
GMP(Good Manufacturing Practice)におけるバリデーションとは、製品やプロセスが一貫して所定の品質を確保できることを科学的に証明するための活動です。バリデーションは、製薬業界や食品業界など、製品の安全性や有効性が厳密に求められる分野で特に重要視されます。
製造プロセスの各ステップ、使用される設備やシステム、さらには洗浄や消毒の手順に至るまで、すべてが期待通りに機能し、規格を満たしていることを文書化し、再現性を担保します。
バリデーションには、プロセスバリデーション、設備バリデーション、システムバリデーションなど、さまざまな種類があります。バリデーションは一度行えば終わりではなく、プロセスや設備に変更が加えられた際には再度行われることが求められます。
これにより、製造環境の変化が製品品質に影響を与えないことを保証し、消費者に安全で信頼性の高い製品を提供するための基盤となります。
バリデーション誕生の背景
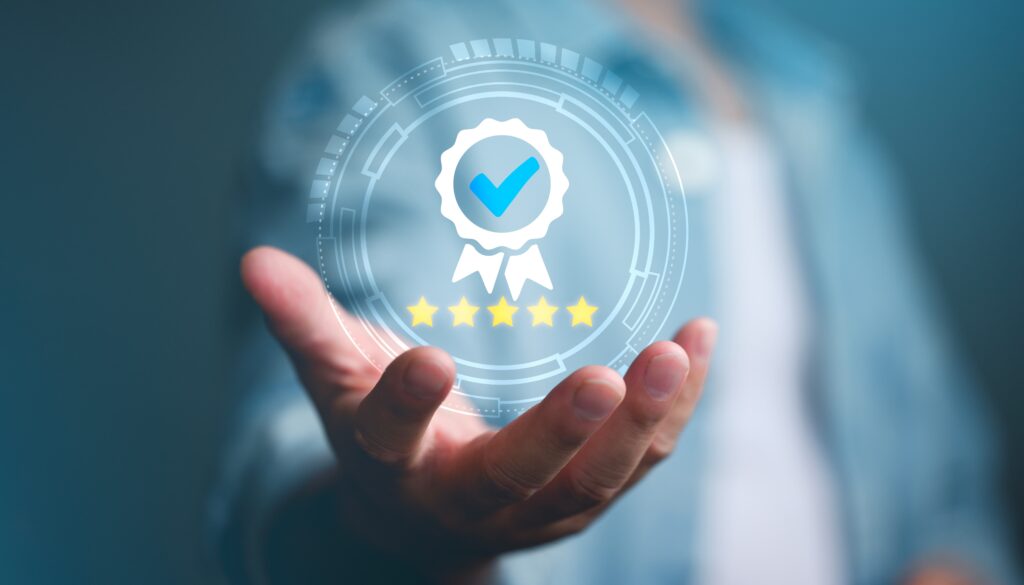
バリデーションの概念が生まれた背景には、1970年代に米国で発生した大容量注射剤による薬害死亡事故があります。この事故は、多数の人命が失われた重大な事件であり、医薬品の製造過程における品質管理の重要性が強く認識される契機となりました。
この出来事を受け、医薬品の製造過程におけるリスクを最小限に抑え、製品の安全性を確保するための体系的なアプローチとして、バリデーションが導入されました。このアプローチは、製造プロセスが常に安定し、予測可能な品質を維持できるようにするための基盤となっています。
バリデーションとベリフィケーションの違い
GMPには、バリデーションとベリフィケーションという言葉があります。いずれも製造業においてよく混同されがちですが、それぞれ異なる目的と手法を持っています。
バリデーションは、製造プロセスが将来的に設計された通りの品質を持つ製品を、恒常的に製造できることを証明するプロセスです。これは、製造過程全体の予測可能性と信頼性を確認し、最終製品が常に高い品質を維持できることを保証するために行われます。
一方、ベリフィケーションは、すでに製造された製品が設計品質どおりであることを確認するプロセスです。これは製品が設計通りに機能し、規格に適合しているかどうかを検証するもので、製品の最終的な品質を保証するための重要なステップとなります。
簡単に言うと、バリデーションは「再現性や妥当性を保証する」ためのもの、ベリフィケーションは「製造結果を確認する」ためのもの、ということになります。
バリデーションの種類
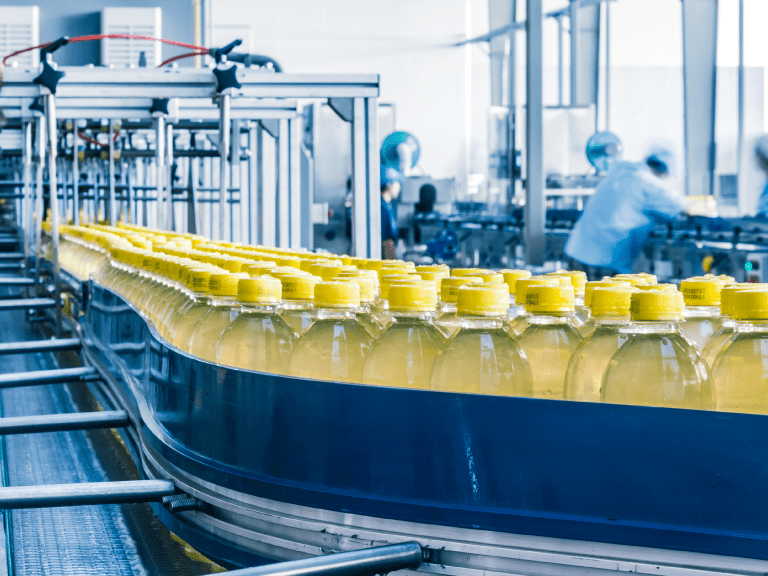
バリデーションには、製造プロセスの各段階で品質と安全性を保証するためのさまざまな種類があります。これらのバリデーションは、それぞれ異なる目的と対象を持ち、製品が一貫して高品質であることを確保する役割を果たします。以下に、代表的なバリデーションの種類について説明します。
- 適格性評価
- プロセスバリデーション
- 洗浄バリデーション
- 再バリデーション
- 変更時のバリデーション
適格性評価(クオリフィケーション)
適格性評価(Qualification)は製造設備や装置が設計通りに機能し、製造プロセスを通じて安定した品質を維持できることを確認するためのバリデーションです。
これは、特にハードウェアに対するバリデーションとして実施され、装置やシステムが設計通りに動作し、製品の品質に悪影響を与えないことを確認します。また、ソフトウェアで制御されているハードウェアに対しても適用され、コンピュータ化システムを含む一連のプロセスが正確に機能しているかを検証します。
この評価を通じて、製造設備の信頼性と再現性が保証され、製品の一貫性を維持するための基盤が確立されます。
プロセスバリデーション
プロセスバリデーションは、製造プロセス全体が一貫して高品質の製品を生産できることを確認するためのバリデーションです。このプロセスでは、適格性評価に加え、各種基準書、手順書、操作マニュアルなどのGMPソフトを含めた評価が行われます。製造が安定し、予測可能な品質を維持できることを証明するために不可欠なバリデーションといえます。
プロセスバリデーションには、新製品や新プロセスの導入前に行われる予測的バリデーションと、製品製造と同時に行われるコンカレントバリデーションの2種類があります。これらのバリデーションは、製造プロセスが設計通りに進行し、品質を確保できることを保証するための重要なステップです。
洗浄バリデーション
洗浄バリデーションは、製造装置や器具が適切に洗浄され、次の製造サイクルにおいて製品に悪影響を及ぼす残留物が残っていないことを確認するためのバリデーションです。このバリデーションは、特に製品間でのクロスコンタミネーション(交差汚染:別の工程や製品が汚染源となり、他の製品にも汚染が拡大してしまうこと)を防ぐために重要であり、医薬品や食品産業など、厳格な衛生基準が求められる業界で頻繁に実施されます。
洗浄バリデーションは、製造工程全体の安全性を確保し、製品の品質を維持するために不可欠なプロセスであり、その結果は文書化され、規制当局への報告や内部監査に使用されます。
再バリデーション
再バリデーションは、製造プロセスや装置の変更が行われた場合、または定期的な品質確認の一環として、既存のバリデーション結果を再確認するプロセスです。このバリデーションは、製造プロセスや装置が経年変化や技術の進歩によって影響を受けないかを確認するために行われます。
再バリデーションは、製品の品質と安全性が常に保たれていることを確認するための継続的な品質管理の一環であり、その結果は、製造プロセスの信頼性を向上させ、将来のリスクを軽減するために重要な役割を果たします。
変更時のバリデーション
変更時のバリデーションは、製造設備、プロセス、または材料に変更が加えられた際に、その変更が製品の品質や安全性にどのような影響を与えるかを評価するためのプロセスです。これは、変更後のプロセスが依然として規定の品質基準を満たしているかを確認するために実施されます。
変更時のバリデーションは、変更が製造プロセス全体に及ぼす影響を最小限に抑え、製品の一貫性と品質を確保するために重要です。このプロセスを通じて、製品が常に高い品質を維持し、消費者やユーザーに安全で信頼性の高い製品を提供することが可能になります。
適格性評価の手順
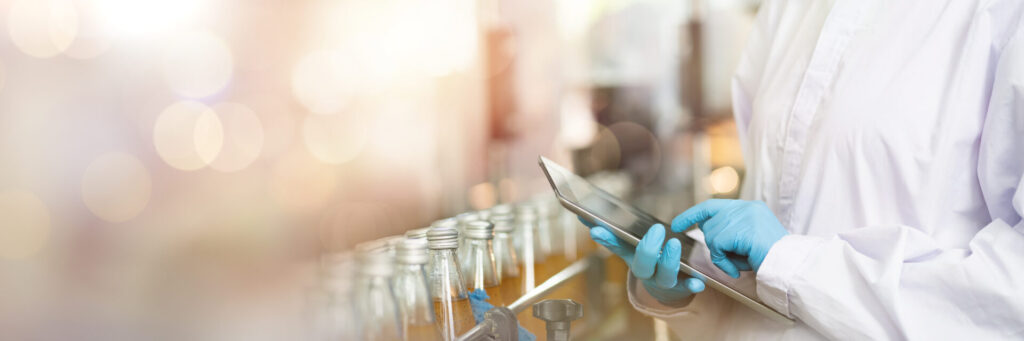
適格性評価(Qualification)は、製造設備や装置が設計通りに機能し、製造プロセスにおいて高い品質を維持できることを確認するための一連のプロセスです。この評価手順は、製造過程の各段階で実施され、それぞれのステップで異なる側面を確認します。ここでは、以下4つの適格性評価について詳しく説明します。
- 設計時適格性評価(DQ)
- 据付時適格性評価(IQ)
- 運転時適格性評価(OQ)
- 性能適格性評価(PQ)
設計時適格性評価(DQ)
設計時適格性評価(Design Qualification, DQ)は、製造設備やシステムの設計が、製品の品質と安全性を確保するために必要なすべての要件を満たしているかを確認する最初のステップです。
この段階では、設備やシステムの設計が規定された基準やガイドラインに適合しているかを評価します。設計仕様書、機能仕様書、リスク分析などの文書を基に、設計が適切であり、後の製造過程で期待される性能を発揮できることを確認します。
DQは、プロジェクトの初期段階で行われ、後の段階での問題発生を未然に防ぐために重要な役割を果たします。
据付時適格性評価(IQ)
据付時適格性評価(Installation Qualification, IQ)は、製造設備やシステムが設計通りに設置され、正確に稼働できる状態であることを確認するプロセスです。この段階では、設備やシステムの物理的な設置状況、配線、配管、接続の適切さを確認します。
また、すべてのコンポーネントが設計通りに配置され、適切な環境条件下で正常に機能することを確かめます。IQの実施により、設置の不備や初期段階でのトラブルを防ぎ、設備の稼働準備が整っていることを保証します。
運転時適格性評価(OQ)
運転時適格性評価(Operational Qualification, OQ)は、設置された設備やシステムが運転条件下で期待通りの性能を発揮できるかを確認するプロセスです。この段階では、製造設備やシステムが設計通りに動作し、すべての機能が正しく動作することを評価します。
具体的には、温度、圧力、速度などの運転パラメータが設定された範囲内で安定しているか、各種センサーや制御装置が正確に機能しているかを確認します。OQは、設備の運転開始前に問題を特定し、後の段階での製品不良やトラブルを未然に防ぐために重要です。
性能適格性評価(PQ)
性能適格性評価(Performance Qualification, PQ)は、実際の製造条件下で設備やシステムが設計された性能を発揮できるかを確認する最終段階です。この評価では、製造プロセス全体が一貫して設計通りの品質を維持できるかを検証します。
具体的には、実際の製造条件での稼働テストを通じて、設備やシステムが期待される生産量と品質基準を満たしているかを確認します。PQの実施により、製品が安定して高品質であることが保証され、製造プロセスの信頼性が確保されます。
バリデーションの対象
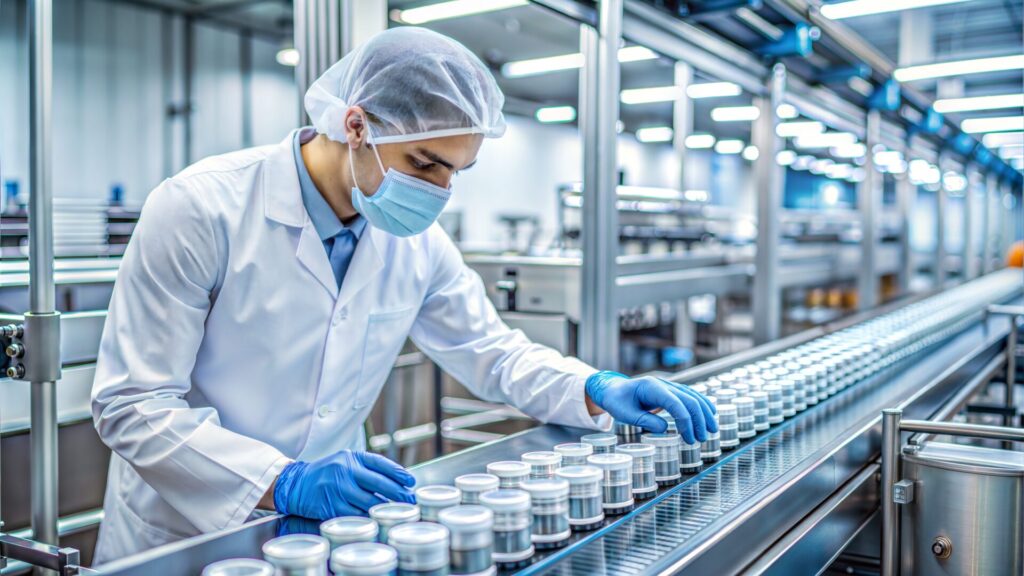
バリデーションは、製造業における品質と安全性を確保するための重要なプロセスであり、製造プロセスのさまざまな要素に対して適用されます。バリデーションの対象は多岐にわたり、設備、システム、装置、プロセス、ユーティリティなど、製品の品質に影響を与えるすべての要素が含まれます。以下では、それぞれのバリデーション対象について詳しく説明します。
設備(Facilities)
設備に対するバリデーションは、製品の製造が行われる施設そのものが適切に設計、建設、維持されているかを確認するプロセスです。これには、クリーンルームの設計、HVACシステム(暖房、換気、および空調)、照明、建物の構造やレイアウトが含まれます。
設備バリデーションの目的は、製造環境が製品の品質に影響を与えないようにし、適切な製造条件を維持できることを確保することです。また、設備の衛生状態や安全性も評価され、製品の一貫性と安全性を保証するために不可欠な要素となります。
システム(System)
システムに対するバリデーションは、製造プロセスを制御し、監視するためのシステムが設計通りに機能し、信頼性があることを確認するプロセスです。これには、製品の温度や圧力を管理するシステム、製造データを記録するシステム、さらには品質管理のためのソフトウェアシステムが含まれます。
システムバリデーションでは、これらのシステムが正確かつ一貫して機能することを確認し、製造プロセスが適切に管理されていることを保証します。特に、システム障害や不具合が製品の品質に影響を与えないよう、定期的なバリデーションが求められます。
装置(Equipment)
装置に対するバリデーションは、製造に使用される機械や器具が正確に機能し、製品の品質に影響を与えることなく使用できることを確認するプロセスです。これには、製品の製造、包装、保管に使用される装置や、測定器具、分析装置などが含まれます。
装置バリデーションでは、装置が設計通りに動作し、期待される性能を発揮できるかを評価します。さらに、定期的なメンテナンスやキャリブレーションが適切に行われているかも確認し、製品の品質に対するリスクを最小限に抑えます。
プロセス(Processes)
プロセスに対するバリデーションは、製造過程全体が一貫して高品質な製品を生産できることを確認するためのプロセスです。これには、原材料の受け入れから最終製品の出荷に至るまでのすべての工程が含まれます。
プロセスバリデーションでは、製造プロセスが安定しており、設計通りの品質基準を満たしていることを確認します。これは、新しいプロセスや製品の導入時、または既存プロセスの変更時に特に重要です。プロセスバリデーションを通じて、製造工程の一貫性と信頼性が保証され、製品の品質が維持されます。
ユーティリティ(Utility)
ユーティリティに対するバリデーションは、製造プロセスを支える水、空気、ガス、電力などのインフラが適切に機能し、製品の品質に影響を与えないことを確認するプロセスです。
これには、供給される水の純度や空気の清浄度、電力供給の安定性などが含まれます。ユーティリティバリデーションでは、これらのインフラが製造設備やプロセスにおいて安定して機能し、期待される品質基準を満たしていることを評価します。
ユーティリティの信頼性を確保することで、製品の品質と安全性が維持され、製造プロセス全体の安定性が保証されます。
まとめ
バリデーションは、製造業において製品の品質と安全性を保証するための重要なプロセスで、設備やシステム、装置、プロセス、ユーティリティといったさまざまな要素に対して適用されます。また、設計時、据付時、運転時、性能の各段階で行われ、特に厳密な品質管理が求められる医薬品や食品産業で重視されています。
バリデーションはGMPを構成する一つの要素として非常に重要な考え方であるため、医薬品の製造に関係する方は是非、知識として理解しておきましょう。GMPについての詳しい解説はこちらの記事で解説しているので、合わせてご参照ください。
→ GMPとは 運用の流れや認証プロセス、導入メリットをわかりやすく解説
22種類の生産管理システムをランキングで比較
初期費用相場や選び方のポイントをチェック
生産管理システムをそれぞれの特徴や初期費用相場などで比較したい場合は、「生産管理システムランキング」も是非ご覧ください。生産管理システムは、自社の製品・生産方式・企業規模などに適したものを導入しないと、得られるメリットが限定されてしまいます。事前適合性チェックや生産管理システムを選ぶ前に押さえておきたいポイントも解説していますので、製品選びの参考にしてみてください。