原価低減とは?なぜ難しい?実践方法や注意点を具体例つきで解説
公開日:2025年04月24日
最終更新日:2025年04月24日
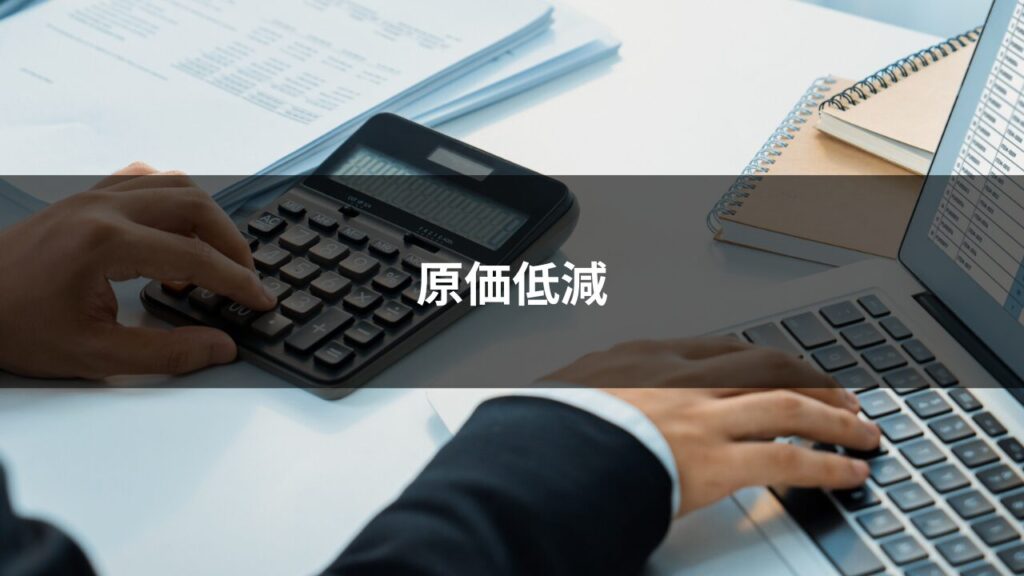
製造業における原価低減は、品質を維持または向上させながら、コストを削減する重要な取り組みです。原価を抑えられると企業の利益率が上がり、競争力強化に繋がります。
原価低減のためには、原価の現状把握やサプライヤーの配慮など、気をつけるべき点が多くあります。本記事では、原価を構成する要素や効率的な削減方法、原価低減の方法や注意すべきポイントを具体的に解説します。
原価低減とは
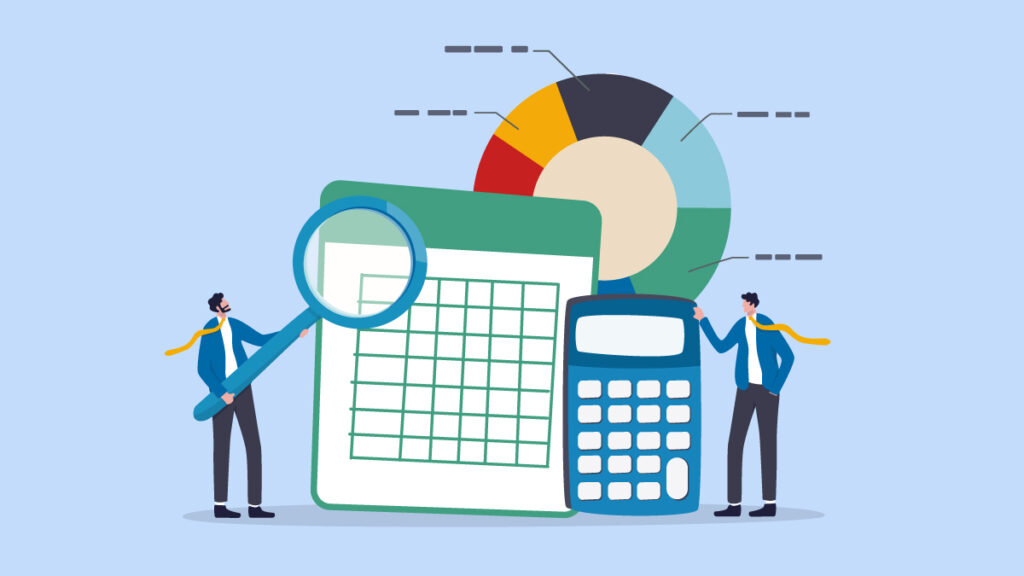
原価低減とは「製品の製造過程におけるコスト」を削減する取り組みです。製造業においては、原材料費、労務費、製造経費など、さまざまな要素が原価を構成しています。原価低減の目的は、これらのコストを低減し、企業の利益率を向上させることです。
得意先から「原価低減できないか」と相談された際は、調達や製造の工夫で値下げできないか、交渉を受けている状況と言えます。
原価の構成
製造業の場合、原価の構成は以下の3つに分けられます。
- 材料費:製品を作るために使用する原材料や部品などの費用
- 労務費:製品を作るために必要な労働力に対する費用
- 経費:製品の製造に直接かかわらないが、製造活動を支えるための費用
これらの原価はさらに特定の製品の製造に直接的にかかる「直接原価」と、製品の製造に直接かかわることなく、製造全体にかかる「間接原価」に分けることができます。原価低減を行う際には、削減すべきコストが原価構成のどれに当たるのかを把握し、効果的な施策を行うことが重要です。
コスト削減との違い
原価低減とコスト削減は一見似ていますが、目的が異なります。
コスト削減は、製造以外の経費も含む、企業全体でのコストカットを目指す活動を指します。製造原価と混同して使用するケースもありますが、一般的には製造原価にくわえ、販売管理費や研究開発費なども含みます。コスト削減では、単純に費用を減らすことを目的としており、場合によっては品質が犠牲になります。
例えば、労働力の削減や安価な原材料への変更などがコスト削減に当たります。コスト削減は短期的には効果があっても、長期的には企業の競争力や品質を低下させる可能性があります。
一方、原価低減は、製造に必要なコストを削減しつつ、品質や生産性の維持または向上を目的とします。原価低減では、無駄なコストの削減だけでなく、生産方法の見直しや新設備の導入により、全体のコストを最適化します。具体的には、生産ラインの自動化や、工程改善、サプライチェーンの見直しなどを行います。
原価低減のメリット
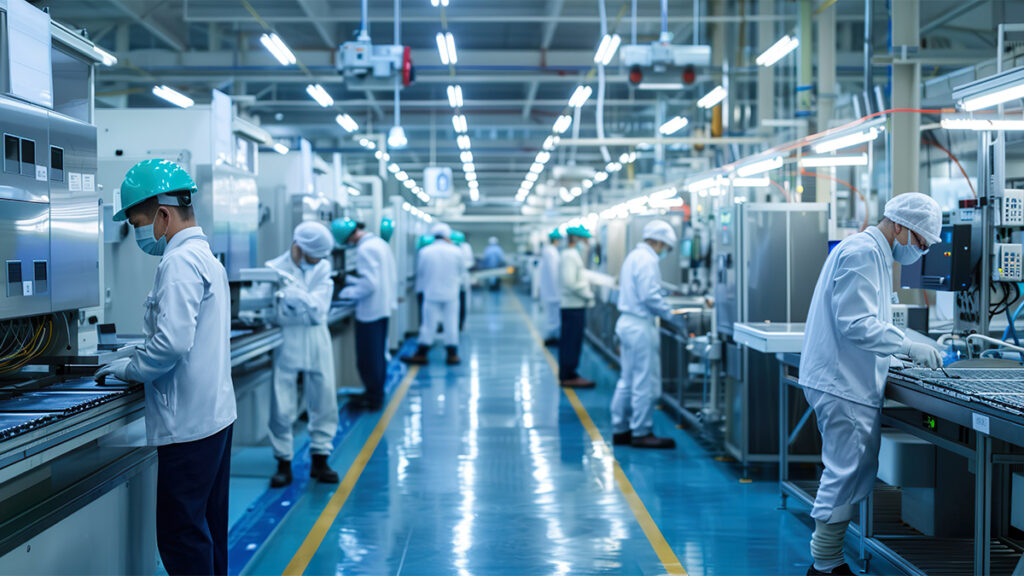
製造業における原価低減は、企業にさまざまなメリットをもたらします。具体例として以下が挙げられます。
- 利益の増加
- 競争力の強化
- 価格戦略の柔軟性の増加
- 設備投資や研究開発への資金確保
- 社員のモチベーション向上
- 持続可能な経営
製造業が原価低減を行うことで、利益率が向上し、競争力を強化できます。原価低減は、価格競争において有利に働き、販売価格を下げることなく利益を確保できるため、市場シェアの拡大にもつながります。また、効率的な資源管理により、無駄な支出を減らし、資金の効率的な運用ができるようになります。
原価低減の具体的な方法
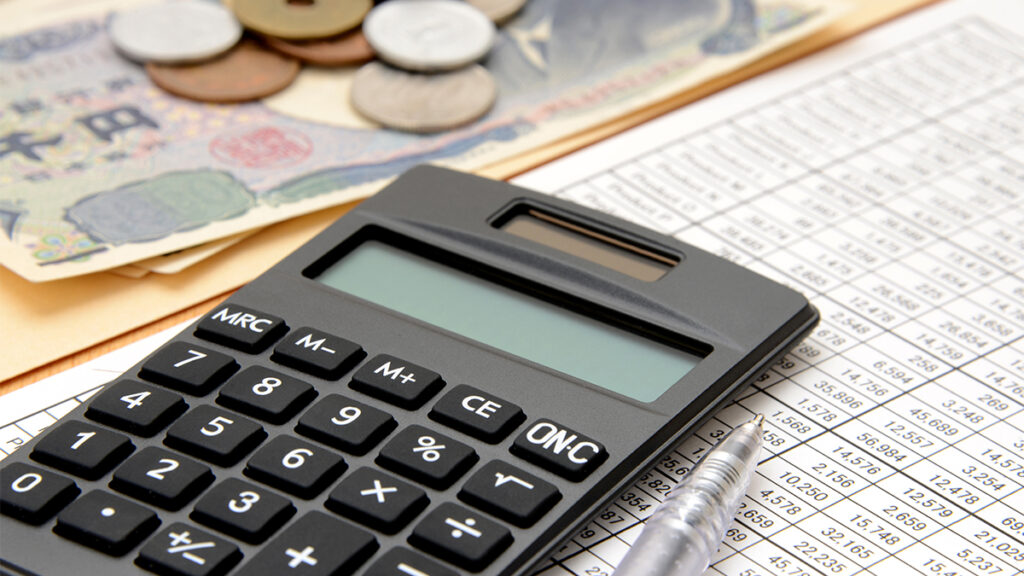
原価低減を行うための具体的な方法を紹介します。主要なコスト要素である材料費、労務費、経費を削減するための例を解説します。
材料費
材料費は製造業における原価の中で大きな割合を占めるため、削減効果が最も高い部分のひとつです。材料費を低減するためには、次のような方法があります。
直接材料費 | 間接材料費 | |
仕入れ先の見直し・交渉 | 購入価格交渉による 単価の引き下げ | 複数の製品で使用する材料の一括調達 |
原材料の一括購入 | 大量購入による 単価優遇を受ける | 不良品を減らすことで間接材料費を削減 |
材料の品質改善 | 製品品質を改善し、 無駄な材料を削減 | 材料管理システムの導入 |
材料の廃棄削減 | 不良品やロスを減らすための 管理強化 | 設備の保守や消耗品の管理徹底 |
物流コストの最適化 | 輸送ルートの最適化による コスト削減 | 工場内でのエネルギー効率を高める |
製造業では材料費の原価に占める割合が大きいので、複数の観点から削減余地がないか検討することが重要です。
労務費
労務費は製造業の原価において重要な要素です。労働力を効率的に活用することで労務費を低減できます。自動化なども含め、具体的には以下のような方法があります。
直接労務費 | 間接労務費 | |
生産工程の自動化 | 生産ラインの自動化により 作業時間を短縮し、 作業員の労働負担を軽減する | 生産工程の自動化により、 監視や調整などの管理作業が減少する |
作業標準化の推進 | 作業標準化により無駄な作業や 工程の重複を減らす | 業務の標準化により管理職の 負担を軽減する |
社員の多能工化 | 多能工化により一人の作業員が 複数の業務を担当できるようにし、 柔軟な人員配置が可能になる | 多能工化により、トレーニングに かかる時間やコストが削減される |
外注の活用 | 特定の業務を外部に発注し、 社員の労働負担を減らす | 外注により管理業務や監督作業の負担が 軽減される |
業務のデジタル化・IT化 | 業務のデジタル化やIT化を 進めることで作業の効率化を図る | デジタル化により、書類の管理や 事務作業の負担が軽減される |
労働時間の管理・改善 | 労働時間の適切な管理を行い、 過剰な残業を防ぐ | 効率的な労働時間管理により、 人事部門の負担を軽減する |
労務費の低減には新たなシステムの導入など、投資が必要な項目も多いので、長期的な観点から施策を検討することが重要です。
経費
製造業の経費には、施設維持費、エネルギー費、管理費などが含まれます。これらの経費を削減するためには、次のような方法が効果的です。
直接経費 | 間接経費 | |
施設維持費 | メンテナンス作業の効率化や 外注費の削減 | 施設の管理体制の見直し、 設備の運用方法の改善 |
エネルギー費 | エネルギー効率の高い設備の導入、 無駄な電力使用の削減 | 再生可能エネルギーの導入、 エネルギー使用のデータ管理 |
管理費 | 人件費の見直しや 作業プロセスの最適化 | 事務作業のデジタル化、 効率的な資源配分 |
これらの方法を適切に組み合わせることで、各費用項目を削減できます。
原価低減の進め方
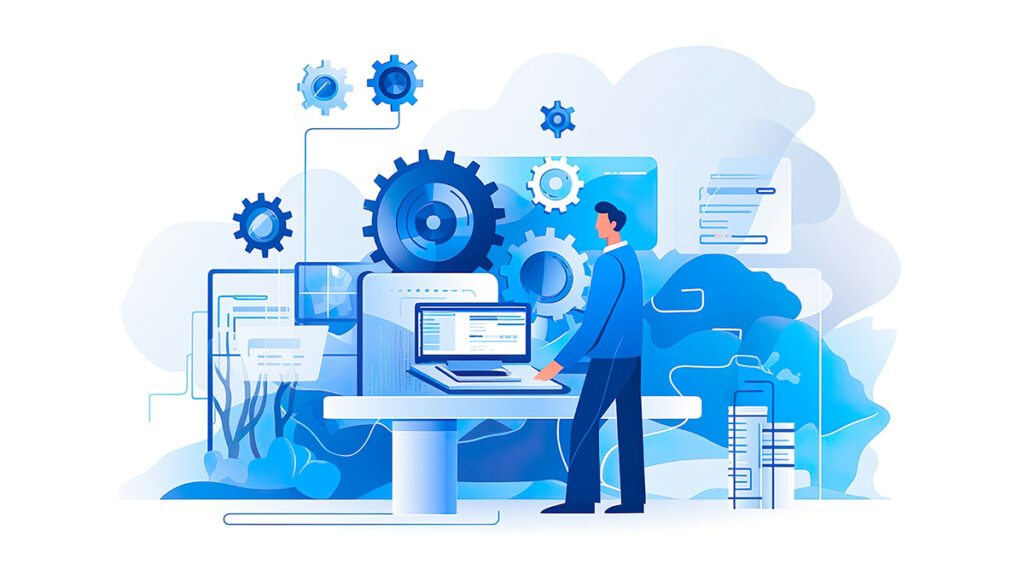
原価低減を進めるためには、まず現状を把握し、適切な目標を設定し、改善策を立案して実行するというプロセスが必要です。ここでは、原価低減を進める際の手順について解説します。
現状分析
まず、最初に行うことは現状分析です。現状分析では、予定原価と実際原価(実際の製造でかかった原価)を比較し、原価差異を確認します。さらに、実際に掛かった製造コストの各項目(材料費、労務費、経費)や過去の動向を詳細に把握し、それらの内訳を細かく分析します。
また、コストに影響を与えている内部の要因(生産プロセス、設備、人的資源など)や外部の要因(仕入れ先、物流費、規制の変更など)も分析します。この段階でのデータ収集と分析が、後の改善策立案の基盤となります。
目標設定
現状分析をもとに、原価低減の目標を設定します。目標設定は原価低減活動の効果測定のために必要です。目標は「原材料費を10%削減する」や「労務費を5%削減する」といった具体的な数値で表すことが重要です。
目標設定には、短期的な目標と長期的な目標の両方を設定します。短期的には即効性のある改善策を、長期的には持続可能なコスト削減を目指します。
改善策の立案
目標が決まったら、目標を達成するための具体的な改善策を立案します。改善策は、現状分析に基づき、最も効果的な方法を選定します。例えば、原材料費の削減には、仕入れ先の見直しや、在庫管理の改善、廃棄ロスの削減などがあります。
改善は企業全体に影響を及ぼすため、従業員の意識改革や教育訓練の実施も重要です。また、改善策の立案には、社内の各部門と連携し、現場の声を反映させることが効果的です。
実行
改善策が立案できたら、それを実行します。実行段階では、計画通りに進行するよう管理する必要があります。ここで重要なのは、改善策をスムーズに進めるための体制を整えることです。自部門だけではなく、各部門との調整や従業員の協力を得ながら実行を進めます。
結果の評価と調整
実行した改善策の結果を評価し、目標に対する達成度を測定します。ここで、実際にコスト削減が実現したかどうかを数値で確認することが重要です。目標達成度を評価することで、次に取るべき施策を決定します。もし目標に達していない場合、理由を分析し、改善策を検討します。
成功事例の共有
原価低減が上手く行けば、成功事例としてまとめ社内で共有します。成功事例をもとに、どのような改善策が効果的だったのか、どのようなプロセスで進めたのかを詳細に共有することで、他の部門が同様の方法を採用し、全社的に原価低減の意識が高まります。
また、成功事例を顧客や取引先にも紹介することで、企業の競争力向上をアピールできます。
原価低減を行う際の注意点
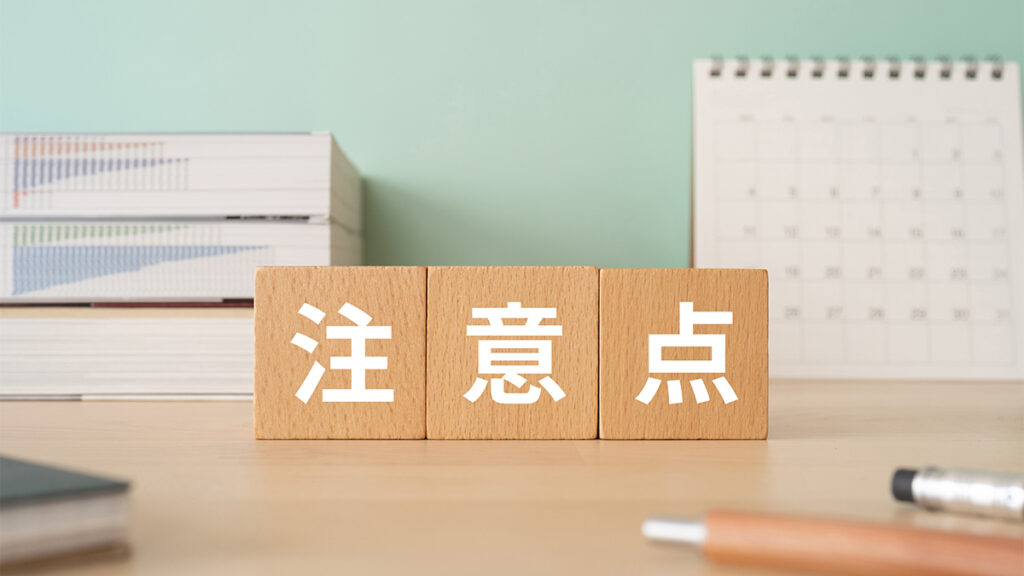
原価低減を実施する際にはいくつか注意が必要です。ここでは、原価低減を行う際に注意すべきポイントについて解説します。
品質の低下を避ける
原価低減を進める際に最も注意すべき点は、品質の低下を避けることです。コスト削減に注力するあまり、品質管理をおろそかにすると、顧客満足度の低下やブランドの信頼性の損失につながります。特に製造業では、製品の品質が企業の競争力となるため注意が必要です。
具体的には以下のような事例があります。
- 低コストな素材を使用した結果、耐久性や強度が不足し、製品の品質が低下する
- 生産工程の短縮を進めたことで、チェック機能が下がり不良品が増加する
- 作業員を減らしたことで、作業の精度が低下する
- 設備の更新を延期した結果、機械の精度が低下する
- 規格を変更したことで、他の部品との互換性が失われる
原価低減策を実施し、品質が低下した場合は、すぐに見直しできる体制にしておくことが重要です。
長期的な視点で取り組む
原価低減は短期的な利益追求だけでなく、長期的な視点で取り組むことが重要です。短期的にコストを削減するために行った方法が、後々の成長に悪影響を及ぼす可能性があります。例えば、以下のような事例があげられます。
- 設備のメンテナンスを後回しにすると、長期的には設備故障が頻発する
- 研修費用を削減したことで、従業員のスキルが低下し、品質が低下する
- 安価な部品に切り替えることで耐久性が下がり、長期的には不具合が増える
- 在庫を削減したことにより、急な需要の変動に対応できなくなる
サプライヤーへ過度な負荷をかけないよう考慮する
原価低減を進める際には、サプライヤーへの一定の配慮もが必要です。コスト削減のため、過度に安価な材料を選定したり、仕入れ先を変更したりすることは、サプライヤーとの関係に影響を及ぼす可能性があります。
特に、サプライヤーが自社にとって重要なパートナーである場合、その関係を損なうことは長期的に企業にとって不利益になります。また、不当な値下げ交渉は、下請法や独占禁止法に違反するリスクもあり、注意が必要です。
原価低減に役立つ分析手法
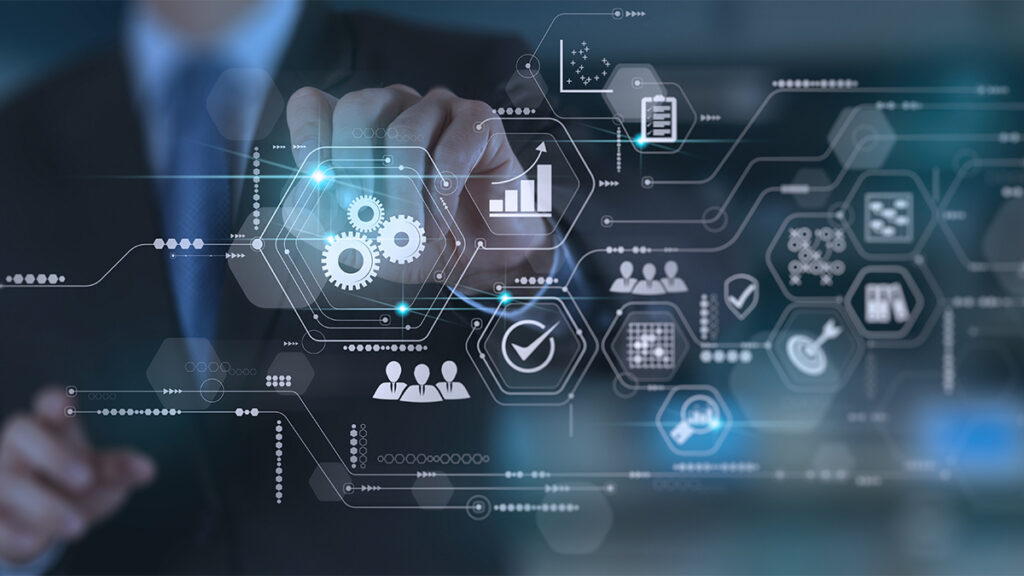
原価低減を効果的に実現するためには、適切な分析手法を活用することが不可欠です。ここでは原価低減に役立つ主要な分析手法を紹介します。
バリューエンジニアリング(VE)
バリューエンジニアリング(VE)は、製品の機能を維持しながら、そのコストを削減するための方法論です。原価低減においては、製品開発や設計段階での改善に役立ちます。
例えば、ある部品に高価な材料を使っている場合、その材料を他の、同じ機能を持つ材料に置き換えることを検討します。また、ある製造工程が過剰なコストを発生させている場合、その工程を効率化する方法を考えます。これらの改善は図面や仕様書の変更が伴うため、設計段階からの改善が必要です。
インダストリアル・エンジニアリング(IE)
IEとは、製造の作業工程を工学的に分析し、改善する手法です。IE 7つ道具と呼ばれる分析手法(工程分析・動作分析・運搬分析など)を用いることで、経験則に頼らない原価低減に繋がります。製造工程にボトルネックがあると想定し、現場改善を試みる際に活用できます。
→ 生産管理に重要なIE(インダストリアル・エンジニアリング)とは 具体的な分析手法や改善方法を解説
ABC分析
ABC分析は、コストを製品やサービスの重要性に基づいて分類する手法です。特に在庫管理や製品別のコスト分析に役立ちます。ABC分析では、アイテムを「A、B、C」の3つのカテゴリーに分け、コストや在庫の管理を効率化します。
- Aグループ: 最も重要で通常は全体のコストの70〜80%を占める
- Bグループ: 中程度の重要性で、全体のコストの15〜20%を占める。
- Cグループ: 最も重要性が低く、全体のコストの5〜10%程度を占める。
ABC分析を用いることで、リソースを効率的に配分し、コストが高い製品に対して改善策を実施できます。
→ ABC分析とは 製造業の在庫管理への具体的な活用方法、注意点や方法まで解説
設備効率分析 (OEE)
OEE(Overall Equipment Efficiency)は、生産設備の効率を測定するための指標で、設備の稼働率、性能、品質を総合的に評価します。OEEは、設備の稼働時間、作業効率、製品品質などを組み合わせて算出されるため、どの部分で設備の効率が落ちているのかを明確にできます。
多くの企業が抱える課題:そもそも原価を把握できていない
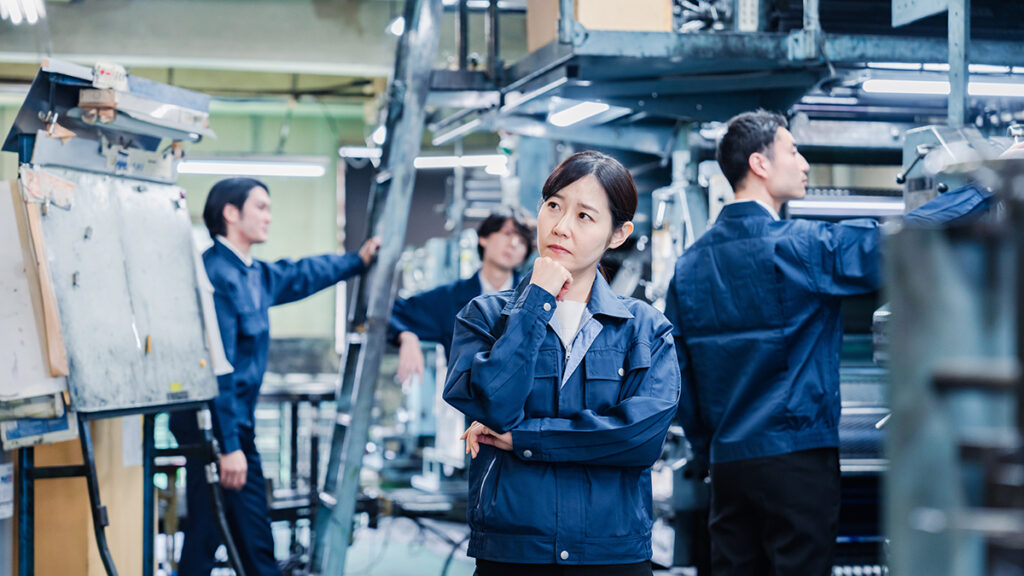
これらの原価低減の取り組みの起点となるのは、原価の現状分析です。実際の製造時に発生した原価(実際原価)が把握できていると、予定原価との差異分析が可能となります。この「原価の予実管理」ができて初めて、原価に課題がある製品を特定できます。
しかし、多くの企業では、「そもそも日頃の原価管理ができておらず、実際原価を把握できていない」という課題を抱えています。原価の予実や原価構造を知らずに、一律で原価低減を試みると、無理が生じ品質への悪影響が出るリスクが高まります。
製造原価を正確に把握するには、使用原材料の仕入単価や、どの作業員がどれだけ時間をかけて作業したか記録する必要があります。システムでの原価管理を行っていない状態で原価分析を試みると、例えば以下のような作業が発生し、非常に煩雑です。
- 紙の仕入伝票や作業日報を遡る
- 仕入伝票の日付を確認し、どの製造に使ったか確認
- 当該仕入単価と作業工数をエクセルに集計
多忙な中でも正確な予実管理を行うには、原価管理システムが不可欠と言えます。
→ 製造業向け原価管理システム9選!機能や特徴、導入メリット、選び方をまとめて紹介
また、製造業における原価管理では、生産管理システムによる予実管理も選択肢として検討できます。
生産管理システムも原価低減に役立つツールの一つ
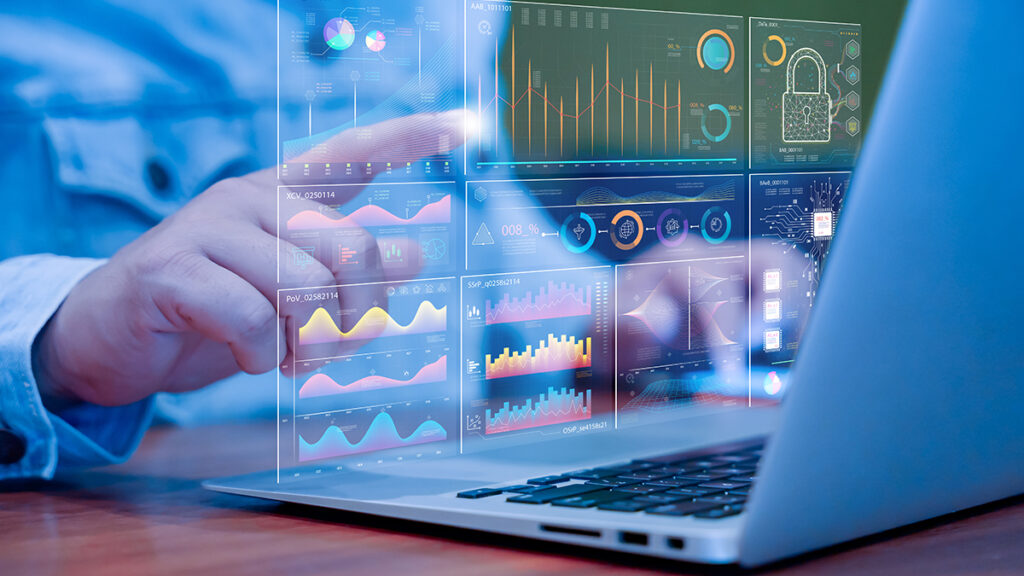
製造業での原価低減を効率的に進めるためには、生産管理システムの導入も非常に有効です。生産管理システムを活用することで、以下のような利点が得られます。
- コストの可視化:材料費、労務費、経費などの各コストをリアルタイムで把握。
- 工程の最適化:無駄な時間や作業を削減し、労務費や設備の稼働率を向上できる。
- 在庫管理の効率化:過剰在庫の削減や欠品を防止できる。
- 生産計画の精度向上:余分な生産や過剰な材料購入を避け、無駄を減らせる。
生産管理システムを活用するとコストの可視化、工程の最適化、在庫管理の効率化、そして品質向上のためのデータ分析を一元的に行えます。
また、ハンディ端末やRFIDを連携活用すると、さらに正確な原価管理が可能となります。例えば、ハンディ端末を使ったQRコードで作業の開始・終了登録を行えば、作業工数を自動集計できるシステムもあります。生産データ収集を通して原価データもリアルタイムに集計できるのは、生産管理システムならではのメリットと言えます。
生産管理システムで原価管理を実現した企業事例:
【生産管理システム】製品別原価管理・粗利分析が可能に!商品開発の予算化による開発スピード向上もできる体制に
22種類の生産管理システムをランキングで比較
初期費用相場や選び方のポイントをチェック
生産管理システムをそれぞれの特徴や初期費用相場などで比較したい場合は、「生産管理システムランキング」も是非ご覧ください。生産管理システムは、自社の製品・生産方式・企業規模などに適したものを導入しないと、得られるメリットが限定されてしまいます。事前適合性チェックや生産管理システムを選ぶ前に押さえておきたいポイントも解説していますので、製品選びの参考にしてみてください。