小さなDXから大きな変革へ。ボトムアップ型DXの成功プロセス
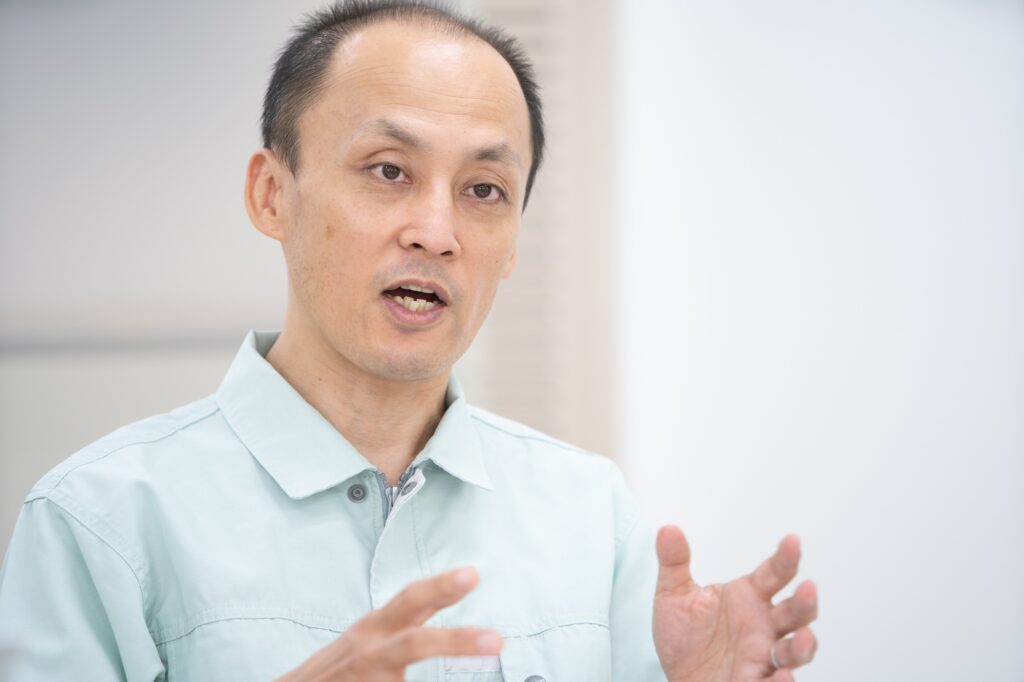
Vol.2 宮川化成工業株式会社
業界:プラスチック・ファインセラミックス射出成形品製造 / 従業員:444名(2022年3月現在)
プラスチックやファインセラミックスの射出成形のパイオニアとして、自動車をはじめとした日本の産業を下支えする宮川化成工業株式会社。近年、ボトムアップによって急速に進むDXについて、代表取締役社長 宮川 愼吾氏、執行役員 大阪事業部長 山下 英樹氏、大阪事業部製造グループ主任 仲本 篤徳氏に話を伺いました。
【目 次】
- 第一章 会社紹介 「まじめを文化に、お客様との信頼関係を構築」
- 第二章 DX化の取り組み-1 「DXによって人と組織も変わる」
- 第三章 DX化の取り組み-2 「IT素人たちの小さな成功が、DXの大きな波を生む」
- 第四章 DX化推進の鍵 「トップの意識と地道な文化づくりで成功体験を積み上げる」
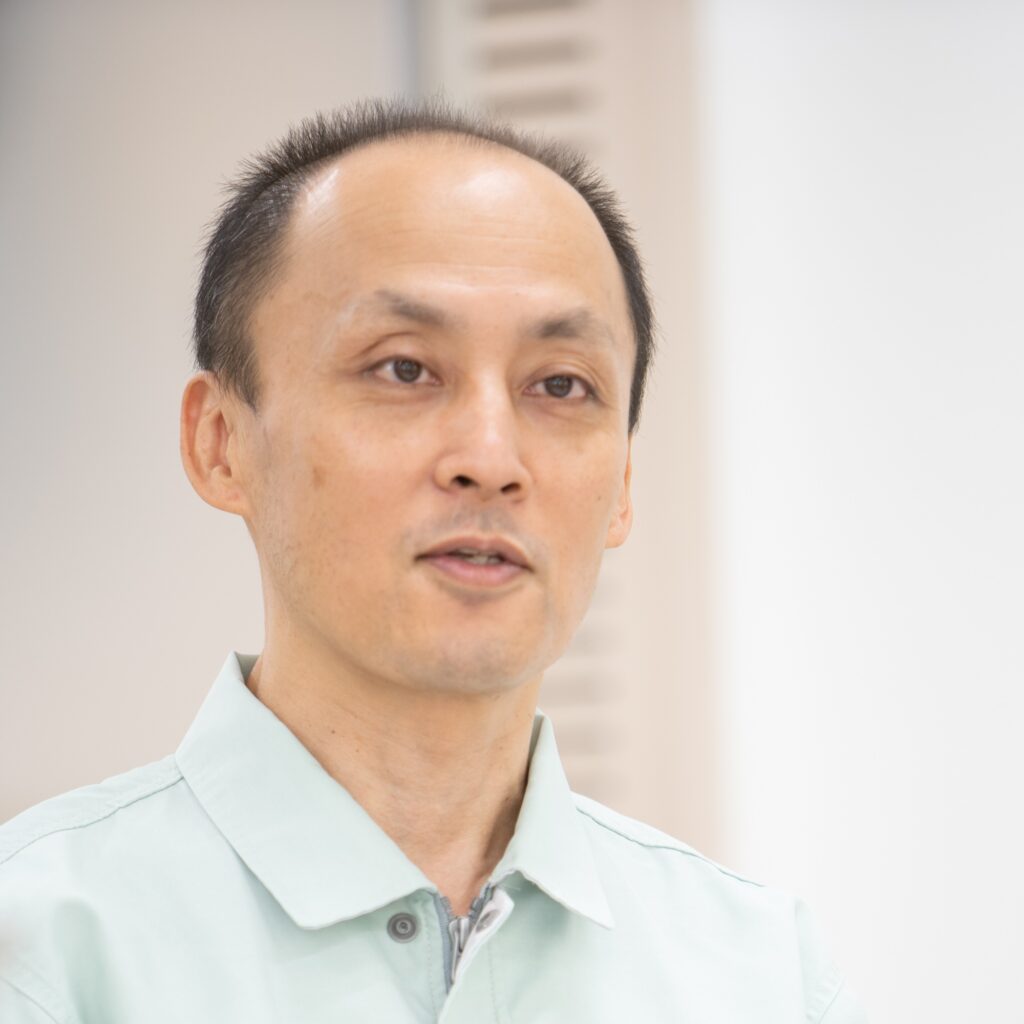
代表取締役社長 宮川 愼吾 (みやがわ しんご ) 氏
大学卒業後、二代目の父から「組織を下から見たらどう見えるか見てこい」と言われ、取引先の会社で営業や労務業務を経験し、1996年に宮川化成工業株式会社に入社。2008年に三代目社長に就任。社員を主体とするデジタル化の取り組みを推進している。
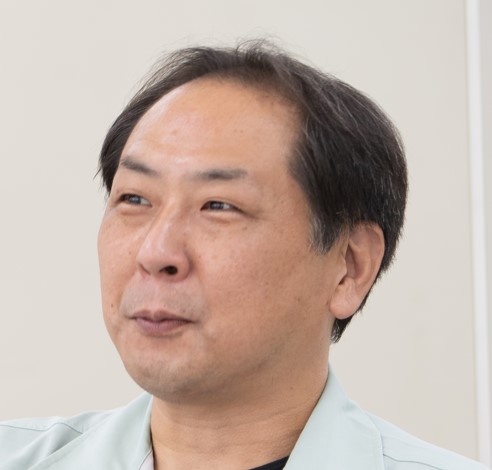
執行役員 大阪事業部長 山下 英樹 (やました ひでき) 氏
セラミックス製造部門と金型製作部門のマネージャー職を兼任し、2022年5月から大阪事業部長に就任。2つの生産部門での業務管理の経験を活かし、身近なところからのデジタル化を推進することで、DXに向けての体制づくり構築に尽力している。
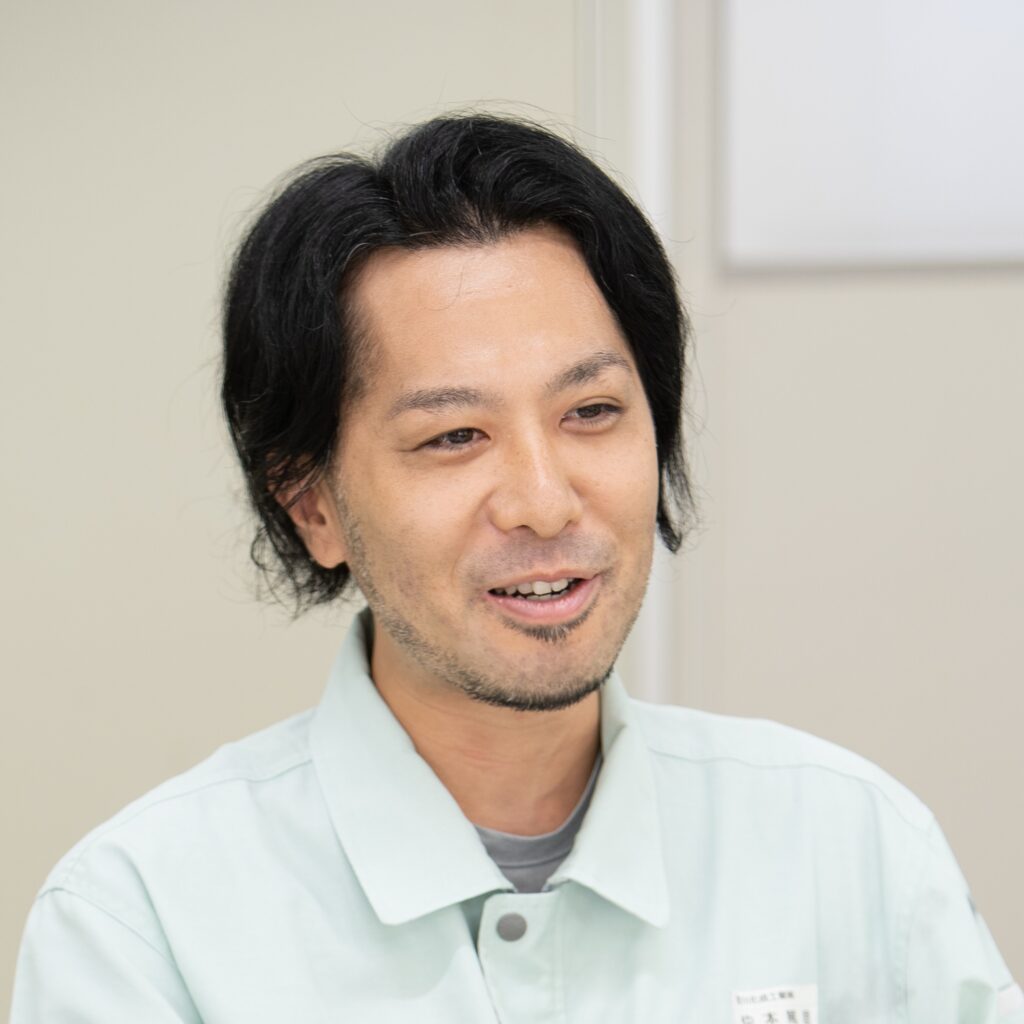
大阪事業部製造グループ主任 仲本 篤徳 (なかもと あつのり) 氏
製造グループで、全製品の生産・工程管理を一手に担い、手書きのアナログシステムからITを活用したシステム運用管理責任者として「現場がやり易い環境作り」を進めている。スマートFを活用し、タイムリーなデータ集計から不良改善活動へ繋げている。
第一章 会社紹介「まじめを文化に、お客様との信頼関係を構築」
——―― 御社の会社紹介をしていただけますでしょうか。
宮川 愼吾氏(以下、宮川):当社は、戦前に祖父がセルロイド板を手加工して蓄電池部品を製作していたことに始まります。戦後すぐに、祖父は「素材のプラスチック化を成し遂げなければならない」という強い信念から、他社に先駆けてプラスチック射出成形機を導入しました。その後着実に技術を確立し、蓄電池部品だけでなく、家電部品、さらには自動車部品の製造へと拡大していきました。1980年代の半ばにはファインセラミックスの射出成形技術確立に取り組み、複雑形状も含めた様々な工業部品も製造しています。現在の事業構成は、自動車部品が過半数を占め、蓄電池部品が1/4、そしてファインセラミックスを加工した部品関係となっています。
同じ業界でも、自動車メーカーから直接受注している企業は多くはありませんが、当社は直接お取引できています。長きにわたって自動車メーカーとお取引できている理由は、製品企画から量産まで一貫して行えることと、製品品質を高く評価いただいているからだと思います。射出成形の技術向上を追求し、製品設計や金型製作、品質管理体制などにおいてお客様のニーズに的確に応えてきたからこそ、繰り返しご用命頂けているのだと思います。

——―― お客様からは具体的にどんな評価をいただいているのでしょうか。
宮川:お客様とお会いした際に言われるのは「頼んだらきちんとやってくれるから安心」というお言葉です。手前味噌ではありますが、当社のみんなが、愚直に業務をこなしてくれているからこそのお言葉だと解釈しております。それを可能にしている理由のひとつに当社の文化があります。
創業時から変わらず、当社を表現する言葉としてぴったりなのが「まじめ」。モノづくりやお客様に対して一直線で、良いものを提供することに徹底的にこだわります。そんなDNAが昔からずっと受け継がれ、社内の隅々にまで浸透しているように感じます。
山下 英樹氏(以下、山下):先日も「まじめ」を象徴するような出来事がありました。ある不具合に対しての解決方法を、現場担当者が中心になって考えていました。その内容が「そこまで追究するのか」というぐらい驚くものだったのです。普通だったら時間やコストなどもふまえて、どこかで妥協すると思うのですが、当社は良いものを追究したら止まらない。上司が何も言わずに、深いところまで自主的に考えていくわけです。
宮川:おそらく歴代の先輩たちの背中を見て、各々が自分を高めてきた。その積み重ねから当社の風土が出来上がってきた。結果だけでなく「まじめで、ひたむきであること」を評価してきた歴史があるから、現場から改善の声があがり、自ら課題解決に向けて動く社員が多いのだと思います。当社がDXに取り組んだのも、やはり現場の声がきっかけでした。
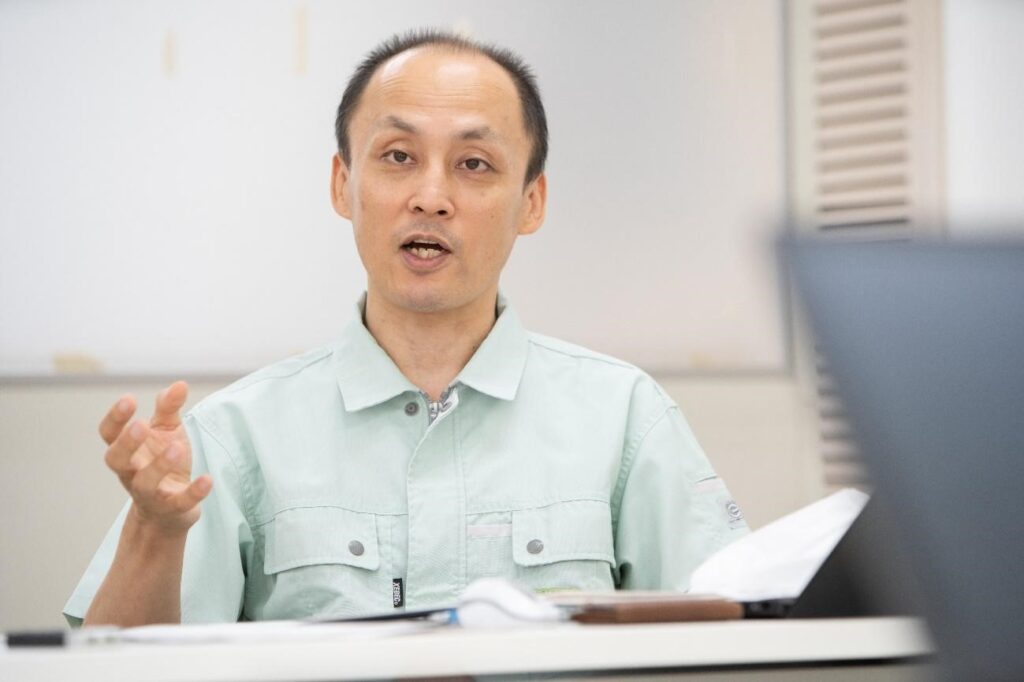
第二章 DX化の取り組み-1「DXによって人と組織も変わる」
——―― 御社のDXの取り組みはいつ頃からどのように進められていますか。
宮川:まだDXという言葉がない20年ほど前に遡ります。ある日を境に、出荷に際して梱包ケースに貼り付けていたお客様支給のラベルに、バーコードが入るようになりました。それまでは、お客様ラベルと当社ラベルを貼り付け、双方を目視照合して出荷していたのですが、どうしても品違いが発生していました。品違い防止策として、当社ラベルにもバーコードを付与し、お客様ラベルと当社ラベルをバーコードで照合すればいいのではないか、という提案が担当事業部からありました。「本当にバーコードによる検品が有効なのか」とは思いましたが、現場の担当者が良いものとして発案しているのだから止める理由はありません。ところがいざ実装してみると、出荷検品ミスが大幅に減り、担当者の顔つきがどんどん柔らかくなっていくのがわかりました。出荷作業に対する検品保証度が上がり、担当者から緊張やストレスが消えていきました。ひとつの事業部で成果が見えると、さらに別の部署でも「やってみよう」となり、社内全体で改善の波が立ちはじめていくのを感じました。
——―― そんな中、大阪での展開のきっかけはどのようなものだったのでしょうか。
宮川:当社は広島、滋賀、大阪の3拠点があり、それぞれ事業が異なります。広島や滋賀では出荷管理を中心にDX化が進んでいましたが、大阪では何も手をつけられずにいました。
そんな中、大阪の月次会議で他拠点の事例を紹介すると、少し経ってから「スマートF」で工程管理の改善をしたいという稟議があがってきました。大阪の現場では工程が非常に多くリードタイムが長いため、手書きで記入していた作業日報を何十枚も集めて集計する必要があり、エクセルへの入力だけで毎日何時間もかかっていました。このようなアナログの象徴のような業務をなくしたいと思い、システム導入を決めました。
仲本 篤徳氏(以下、仲本):難易度が高い工程管理のDX化に取組むことになったので、スモールスタートできる点と価格面で「スマートF」に決めました。展示会でいくつかの生産管理システムを見ていたのですが、「スマートFは使いやすそうだな」と思ったのも印象的でした。
——―― 導入されて、現場の反応はいかがでしたか。
仲本:現場作業者にはデジタルに慣れていない年配の方も多く、はじめは抵抗感がありました。
しかし、どんな方でも実際に使ってみるとその使いやすさから不安も抵抗もすぐに消え、手書き作業が不要になったことで後戻りできないようになっています。
紙で管理していたころは作業実績が翌日以降にしか反映できないので、急ぎで部品や製品が必要になったときには、都度作業者が別担当者に直接確認しに行っていました。導入後はデータでリアルタイムに管理でき、データを見れば状況が分かるようになったことで、現場作業者もいつの間にかデータで管理する取り組みに対して抵抗がなくなりました。
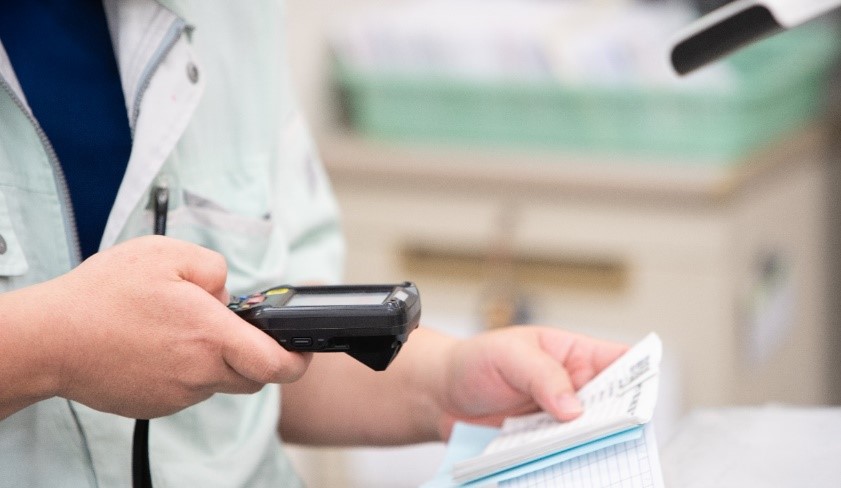
——―― 導入する上で、どんな苦労がありましたでしょうか。
仲本:導入当初は精度確認をするため、従来の手書き&エクセル管理と、「スマートF」のデータ管理を2ヵ月間並行で実施しました。手間はかかりましたが、「スマートF」の精度に全く問題がないことがはっきりしたことで安心して利用できるようになりました。また、機種や分類ごとに精度確認を行い、安心を積み上げていったことも良かったと思います。
——―― 導入によって、特に良かった点は何ですか。
仲本:導入前は作業者の手書き日報を、翌日に半日かけてエクセルに入力し実績データを管理していました。それが「スマートF」なら5分で終わるのですから、管理者として感動は大きいです。
また、主要製品は遅れが発生すると影響が大きいので、仕掛品や完成品などの在庫を毎朝私が確認していました。それもリアルタイムで見える化でき、毎朝の30分程度の時間ですが、当日の作業計画作成に集中できるようになりました。
データは鮮度が重要だと考えています。問題を解決するためには瞬時にデータにアクセスし、分析する必要があるのですが、「スマートF」ではそのタイムラグがなくなり、すぐに改善のための行動ができます。これは「スマートF」の最大のメリットだと思います。
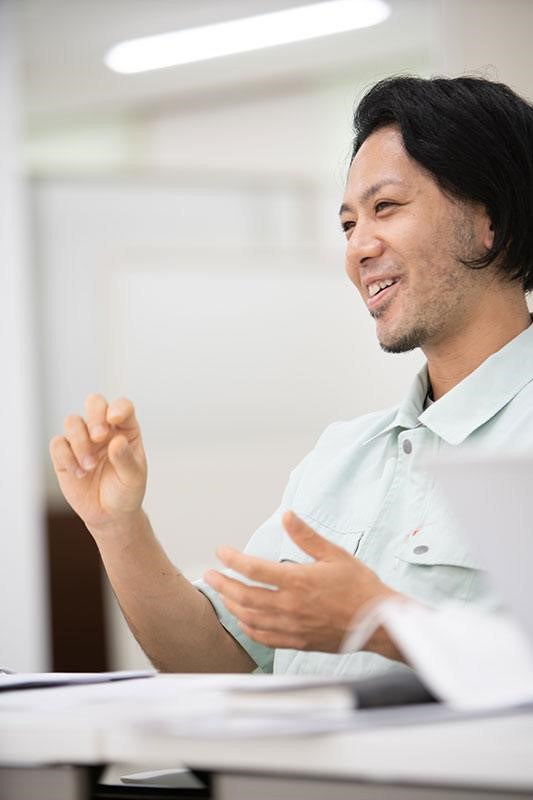
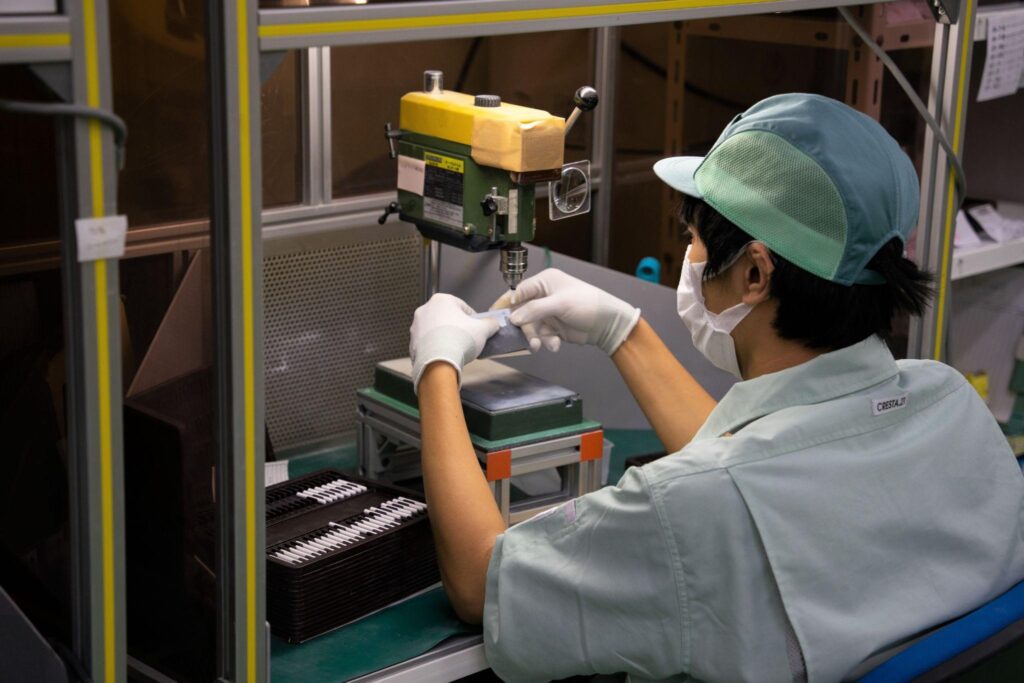
自分の出来栄えに対するフィードバックがリアルタイムで確認できることも、成長につながり、励みに
なります。「スマートF」はひとつひとつの作業に対する当事者意識を醸成してくれます。
システム導入して仕組みを変えると、人も組織も変わっていくのだと感じています。
第三章 DX化の取り組み-2「IT素人たちの小さな成功が、DXの大きな波を生む」
——―― 早い時期からDXを進めておられますが、他にも最近のDXの取り組みはありますか。
宮川:まだまだ理想のDXとはほど遠いです。ですが新型コロナウイルスの流行をきっかけに、会社全体のデジタル化が大きく進みました。
稟議書のワークフローのデジタル化は20年前から着手しており、それ以外の書類もデジタル化できる状態ではありましたが、なかなか進んでいませんでした。それが、新型コロナウイルスの流行によって人の動きが止まり、そのタイミングでほとんどの申請関係を紙からデジタルにシフトしました。給与明細や、社内で回っている44種類の申請書類をデジタル化しました。以前までは私のデスクに毎日書類が届けられたのですが、それもほぼ全てなくなり、非常にスムーズな申請・承認が実現するようになりました。
また、大きく働き方が変わった取り組みもあります。ある事業部で「外部社員用に活用し始めた勤怠管理システムが、非常に便利である」という発信がありました。それまでは、タイムカードでの出退勤管理を行っていましたが、締め日毎の集計業務が非常に繁雑でした。その負荷が減っているというのです。「それならば、一層のこと、社員向けにも使えばどうか」となり、全事業部の総務担当者たちが主体となって、管理部と共に、非常に短期間でカメラとカラーコードによる出退勤管理システムを導入し、運用を始めました。誰がどれくらい残業しているかがリアルタイムで共有されることと、コロナ禍での働き方マインドの変化もあり、残業が大幅に少なくなりました。締め日後の集計作業も大きく簡素化されました。
——―― 現場発信のDXで大きな成果が上げられたのですね。他にも現場発信でDX化が進んだことはありますでしょうか。
宮川:はい、当社では、ほとんどが現場からの発信で、最近も少しずつ増えています。
一つは、出荷検査成績書のデジタル化です。あるお客様から「製品の納品と同時に出荷検査成績書を届けてほしい」というご要望がありました。出荷検査業務では、出荷待ちの製品を抜き取って測定・検査し、その結果を一つずつ手書きします。測定結果を、各基準、公差と比較して合否を判定します。そして測定結果をエクセルに入力し、成績書に仕上げ、印刷したものを製品に同封します。この業務を出荷トラックが出発するまでに仕上げなければならず、担当者には非常に大きなプレッシャーになっていました。
これをなんとか改善したいという思いで、担当事業部から「タブレットから出荷検査成績書を作成できるシステム導入」の提案がありました。まず、Bluetoothを搭載した測定器とタブレットを連結することで、測定結果が自動的にタブレットに入力できるようにしました。併せて、その結果が規格内かどうかの判定を、即座に自動で行うようにしました。万が一、不合格が出た場合は、管理者に連絡がいきますので、不測の事態への対応も速やかに行えます。また、タブレットのカメラから簡単に現物を撮影できますので、これも品質保証度の向上に役立ちました。検査担当者のストレス軽減と同時に、効率化や品質向上を実現でき、お客様にも喜んでいただけました。今後、適用範囲を拡大していく予定です。
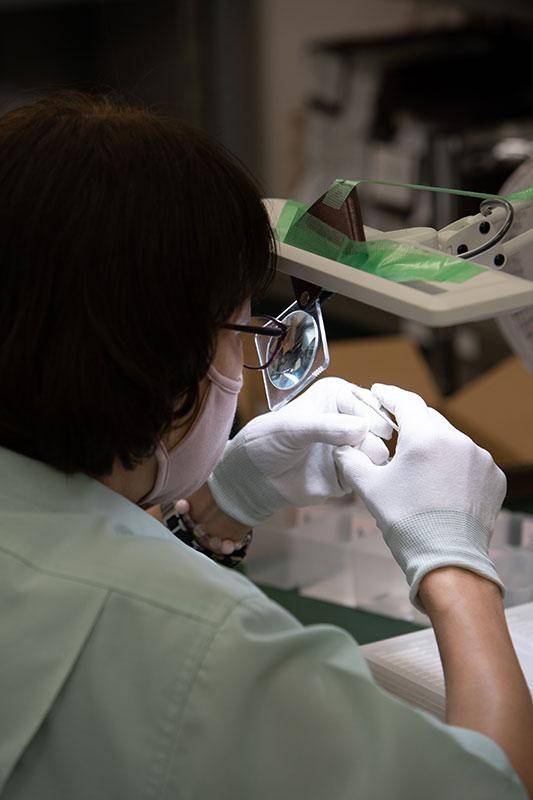
——―― 社内だけでなく、お客様にも喜んでもらえると効果を感じますね。
宮川:お客様にご迷惑をおかけしたことをきっかけに、改善に取り組んだものもあります。
ある製品の製造で、仕様変更手続きを誤り、お客様にご迷惑をおかけしたことがありました。もちろんそれまでもできるだけミスを減らす取り組みの努力はしていたのですが、どうしても人の作業なのでミスが発生してしまいます。そのための対策として、バーコードを活用し、仕様変更が正しいかをチェックできるシステムを社内で作成しました。それを設備まで連動し、もしエラーが出れば次工程の生産がスタートできないようにし、発生を完全に防止できる仕組みにまで作り上げました。
実はこのシステムもお客様にご迷惑をおかけした現場担当者たちが自発的に改善する意識をもち、かなり短い期間で作り上げ、お客様にご報告しました。
——―― 実際にはどのような方が主導されているのでしょうか。
宮川:ほとんどがITの素人です。PCが好きというぐらいのレベルや、まったくIT素養がないものも
います。
出荷検査成績書のデジタル化も、今までITに全く縁のなかった社員が一生懸命取り組んでくれました。DXだからといって、必ずしも高度なITスキルが必要なわけではありません。実際に大阪事業部はIT素人の集団です。それでもDXを実現できたわけです。その経験がモチベーションになりますし、別の部署や領域の担当者にも「できるんだ」という自信が波及していき、新たなDXの動きをつくっています。難しい技能や知識を持つよりも、「好きこそものの上手なれ」で、興味を持ってくれることがDX実現の一番の近道だと思っています。
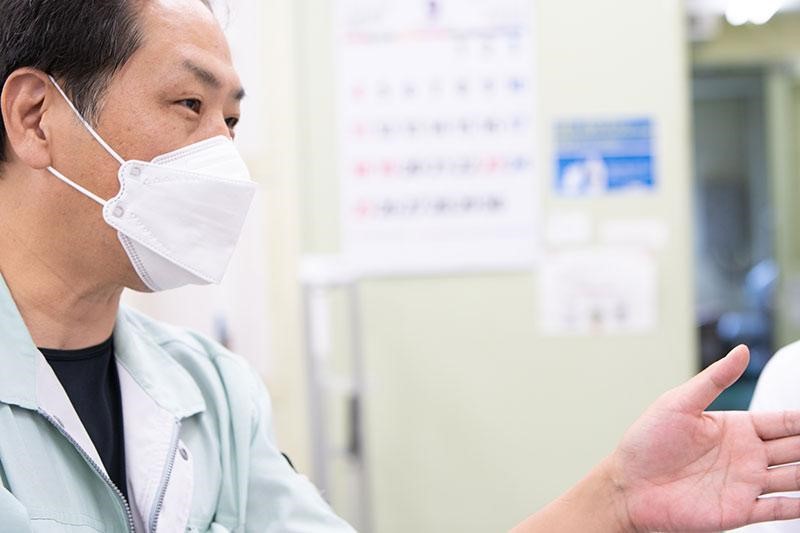
第四章 DX化推進の鍵「トップの意識と地道な文化づくりで成功体験を積み上げる」
——―― 御社は、どうして現場から自発的にDXが推進されているのでしょうか。
宮川:まず一番大事なことは、トップの意識だと思います。
現場では必ず課題を抱えています。それに対して、トップが頭ごなしに解決策を指示するのではなく、現状を聞いて相談に乗りながら、みんなに解決策を考えてもらうということを意識しています。
そうして現場から出てきた取り組みや稟議については、よほどでない限り承認することにしています。経営者の立場からすると、どうしても効果を求めたくなるのですが、そうなるとみんなは萎縮してしまい、自主的な取り組みはうまくいかないことが多いです。ですので、効果については、あまり厳しく追及せず、まずは実現してもらうことを大事にしています。
一方で、みんなが自ら発意したものであれば責任
を持ってやってくれます。みんながワイワイガヤガ
ヤと何かをやっている。「こんなんできたらいいな
あ」という声がどんどん上がってくる。それをムダ
なものではなく、成長のタネだと捉えられるかで、
会社の未来は大きく変わるように思います。遠回
りかもしれませんが、私がみんなの考えに共感で
きれば、背中を押して過度な期待をかけずにじっ
くり見守る。結果ではなく活動そのものを評価して
いくことが大切だと思います。
それが一度成功すると、次に繋がり、現場で自発
的にDXが推進されていく。当社も最近少しずつ
そんな会社になってまいりました。
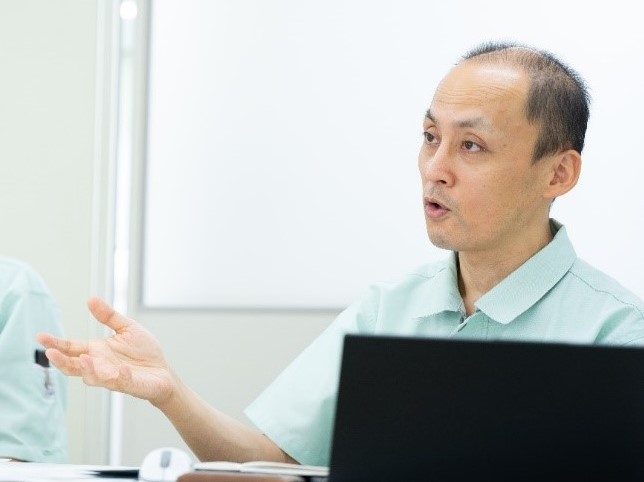
——――他に、社員の自主性を引き出すための取り組みはありますか。
宮川:1970年から続けているQCサークル活動は、そのひとつかもしれません。
半期にひとつのテーマを決め、各グループで要因解析から改善の取り組みまでを進め、その成果をみんなの前で発表する発表会まで行います。当社は、事務部門も含めて全社展開し、約30サークルが活動しています。各グループメンバーの中には、営業職もいれば技術職もいて、部署の枠を超えることで発想が広がり、議論の質も上がります。テーマの中にはDXに関わるものもあり、QC活動からスタートしたDXの取り組みもありました。
また、自分が何か悩みや課題を抱えているとき、QC活動があることでその悩みや課題を他者にぶつけることができます。QC活動を通してみんなは自分の思いや考えがカタチになる実感を得ることでき、それが日常業務での自主性や積極性につながっているのでないかと思います。
QC活動も長年続けていると形骸化していた時期もありました。しかし、どうしたら良いかを考え、トップが関心を持つようになると、みんなの取り組み方も変わりました。やはり地道な継続と工夫は必要不可欠だと思います。
——――最後に、宮川社長にとってDXとは何でしょうか。
宮川:DXとは、作業者の安心をつくることではないかと考えています。
デジタルを活用した仕組みをつくり、属人性をなるべく無くすことで、みんなは安心して作業に取り組めます。さらに品質が保証され、お客様にも安心を届けられます。
業務の効率化や省人化、工数削減など、デジタル化によって実現できることは数多くありますが、そのすべてが「安心づくり」に結びついていきます。DXは、やりがいと幸せをもたらすものだと感じています。
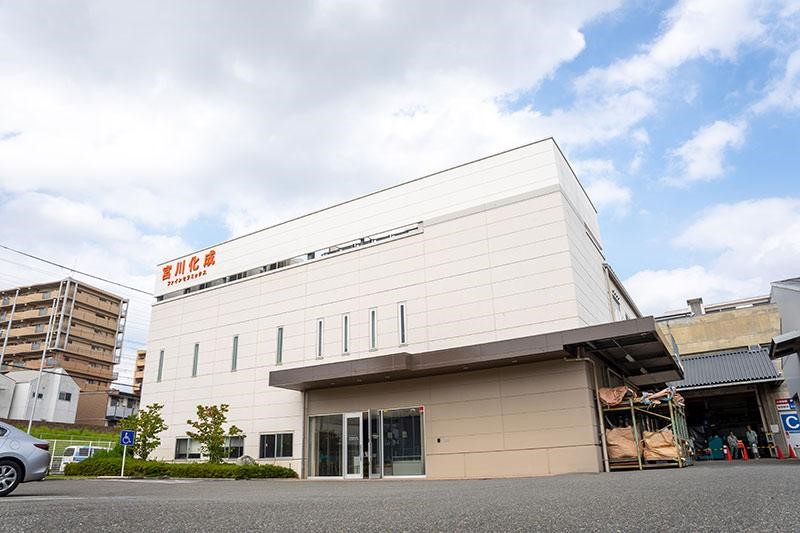
宮川化成工業株式会社
〒533-0004
大阪市東淀川区小松1-16-25
TEL 06-6328-4123(代)
FAX 06-6328-6641
https://www.miyagawa.co.jp/
22種類の生産管理システムをランキングで比較
初期費用相場や選び方のポイントをチェック
生産管理システムをそれぞれの特徴や初期費用相場などで比較したい場合は、「生産管理システムランキング」も是非ご覧ください。生産管理システムは、自社の製品・生産方式・企業規模などに適したものを導入しないと、得られるメリットが限定されてしまいます。事前適合性チェックや生産管理システムを選ぶ前に押さえておきたいポイントも解説していますので、製品選びの参考にしてみてください。