2025年01月23日
【在庫管理システム】紙・エクセル管理をやめて年間3000時間以上の工数削減!先入先出・期限管理の精緻化で品質管理体制の強化まで実現
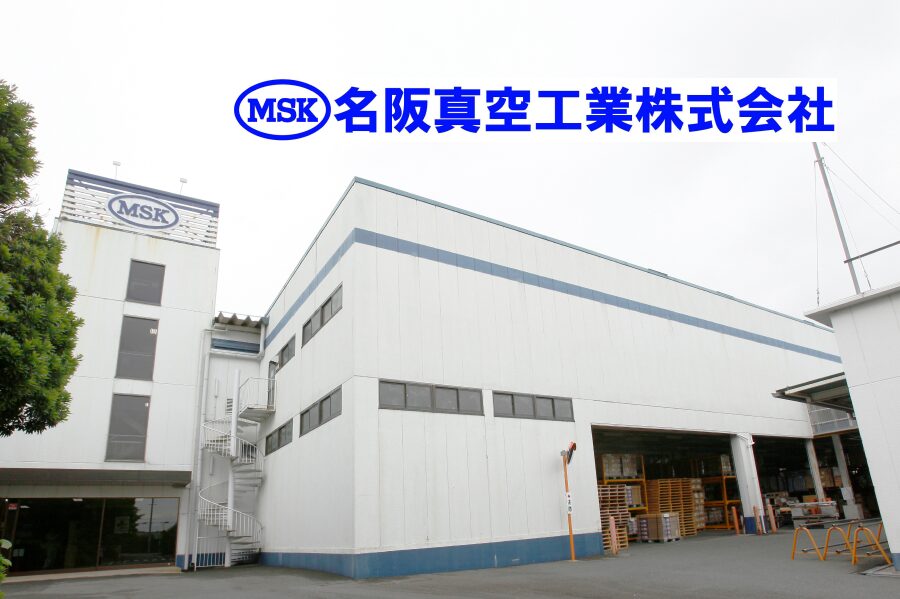
名阪真空工業株式会社
業界 | 化学品業界 |
---|---|
会社規模 | 100~299人 |
機能 | 在庫管理 |
システム概要
課題
- 先入先出の管理が属人的で、取引先からの監査対応においても課題感があった
- 毎日の入荷作業後、エクセルの在庫管理表に入荷数を手入力
- 在庫移動もエクセルの在庫管理表に手入力、リアルタイムに製造現場の在庫状況が確認できなかった
- 棚卸しは棚札を用いて丸1日、その後の棚卸データは手入力で5営業日かかっていた
- 正確な在庫を知るため、現場に実在庫数の確認を毎日依頼していた
解決策
- スマートFの在庫管理機能を導入
- スマートFと連動するハンディーターミナルを運用開始
- QRコード付きラベルで在庫情報を管理
効果
- QRコード照合で正確な先入先出と期限管理まで実現
- エクセル在庫管理表の運用をなくし、手入力の工数を年間2400時間削減
- 在庫移動のエクセル管理もなくなり、年間360時間の工数削減
- 紙の棚札運用・棚卸しデータ入力が不要になり、約100時間の棚卸工数削減&約300万円の経費削減
- スマートFで正確な在庫情報を照会できるようになり、現場問い合わせの工数を年間約100時間圧縮
削減時間を換算すると?
年間3000時間の工数削減 = 年間で6人分x2時間の残業を削減
(例:製造業の平均営業日数約240日に対し、1日1人2時間残業がある場合 2h×240日×6人=約3000時間)
導入の背景
アナログな品質管理ではミスを防ぎきれず、取引先からの監査対策も難しかった
名阪真空工業株式会社様は、プラスチックやガラスの表面処理・塗装にて高い技術力を持ち、「MSK」ブランドで知られています。
従来、紙やエクセルで在庫管理を行ってきたものの、アナログ管理だと先入先出の徹底に限界を感じていらっしゃいました。手作業での管理ではヒューマンエラーを減らすことが難しいため、取引先からの監査における品質管理体制の説明にも課題感がありました。
同社は15年以上前に一度、この課題を解決すべく、在庫管理システムの検討をされたことがあります。しかし、その際は現場の要望を出すほど見積金額が膨らみ、最終的には数千万円ほどの案件になってしまいました。このコストの問題で、システム導入を断念された背景があります。
今回のシステム導入の再検討では、取引先からの紹介などで情報収集を行い、最終的には4〜5社の中から比較検討されました。そして約半年の検討を経て、スマートFをお選びいただきました。
SmartF(スマートF)に決めた理由
まずは小さく部分導入し、後から機能拡張が可能。システムの要件定義の負荷も最小限に抑えられた
スマートFを選んでいただいた理由は、部分導入でスモールスタートし、後から機能追加による拡張が可能だったからです。導入コストはもちろん、システム導入前の要件整理の手間を最小限に抑えられる点にメリットを感じて頂けました。
従来型のカスタマイズ前提の生産管理システムだと、初めに自社の要件をすべて洗い出し、整理したうえでベンダーにオーダーする必要があります。しかし、要件定義のためには、自社のあらゆる製造情報をまとめなければなりません。同社は、膨大な情報を整理したうえで要望を出すことに、難しさを感じていました。
しかし、機能単位で導入可能なパッケージ型システム「スマートF」であれば、まずは在庫管理から導入し、後から工程管理の機能も追加する、といった段階的な導入が可能です。一部の業務からシステム化できるため、要件定義の工数を最小限に抑えられる点が魅力だったとのことです。
また、導入コストの低さも、システム検討の後押しになりました。過去に導入を断念したシステムと比較すると、スマートFは初期費用を含めても半額以下のコストで導入できました。
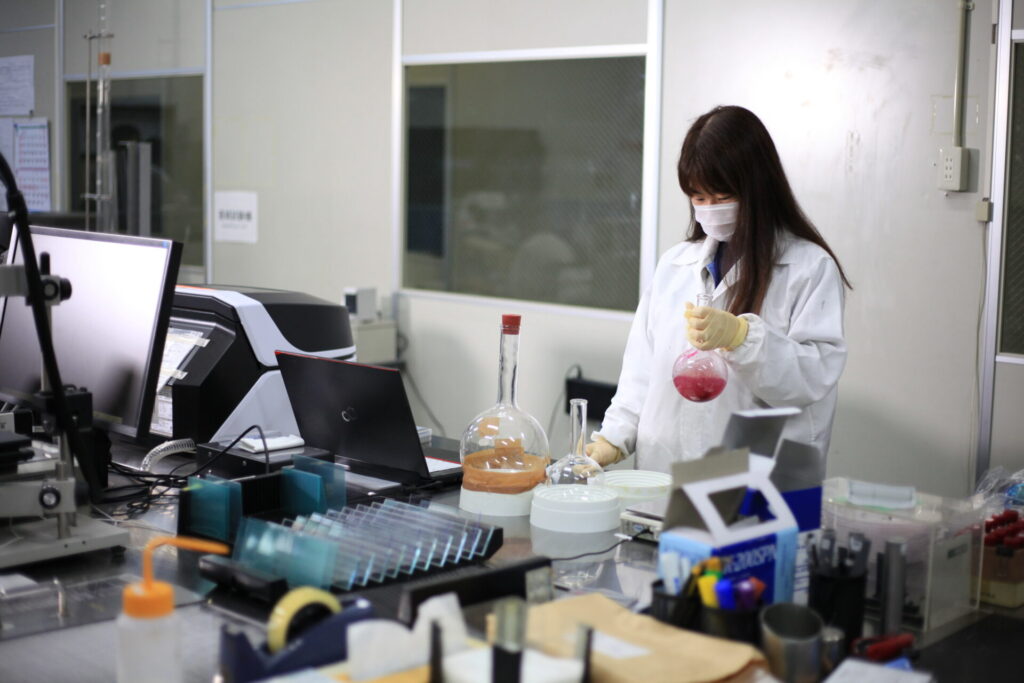
導入効果
先入先出の管理の精緻化で品質管理体制を強化
【導入前】先入先出の管理が属人的で、取引先からの監査対応においても課題感があった
原材料の先入先出は、新たに入荷した原材料は古い在庫の奥に置く、といった現場ルールによるもので、属人的な状態だった。例えば、倉庫担当者が不在だと原材料の保管場所がわからない場合もあり、代理の作業者が新しいロットの原料を出庫してしまうなどのミスが起きるリスクがあった。
同社は品質管理が厳しい塗料なども扱うため、監査において管理体制の指摘を受けることもあった。
【導入後】QRコード照合で正確な先入先出と期限管理まで実現
入荷処理をハンディーターミナルで行い、同時にQRコード付きラベルを発行・貼付する運用を導入。QRコードには入荷品のロットや期限情報などが含まれ、原料使用時に誤ったロットのラベルを読み取ると、エラーが出る。また、保管場所もスマートF上でわかるので、在庫が行方不明になることもなくなった。
これにより、先入先出や期限管理を徹底でき、監査においても品質管理体制を示しやすくなった。
【先入先出】スマートF導入前後の変化
新たな入荷品は古い在庫の奥に保管するルール、担当者以外が保管場所を把握することが難しい
↓
QRコード付きラベルで、ロット・期限・保管場所を管理(属人化の解消)
入荷のたびにエクセルの在庫管理へ手入力していた作業がゼロに
【導入前】毎日の入荷作業後、エクセルの在庫管理表に入荷数を手入力
入荷作業後、仕入先の納品書をもとに、エクセルの在庫管理表へ入荷数を手入力し、在庫数を更新していた。しかし、ヒューマンエラーをなくすことが難しく、理論在庫と実在庫の差異が度々発生していた。このため、あるはずの在庫がない、入荷品が見つからないなどのトラブルがあった。
入荷品は1日100品目を超える日もあり、エクセル手入力の作業負荷も大きかった。午前中に受け入れた入荷品の情報を、エクセルの在庫管理表に反映し終えるのは、午後以降になることもあった。このタイムラグのため、最新の在庫数を確認することが難しかった。
【導入後】エクセル在庫管理表の運用をなくし、手入力の工数を年間2400時間削減
スマートFと連動したハンディーターミナルで、リアルタイムに入荷登録を行う運用に変更。エクセルの在庫管理表への手入力作業は全拠点で不要になり、年間で約2400時間の工数削減に成功した。
さらに、在庫情報の更新にタイムラグがなくなったことで、全拠点で常に最新の在庫情報をスマートF上で確認できるようになった。在庫の保管場所まで見えるようになったので、在庫が行方不明になることもなくなった。
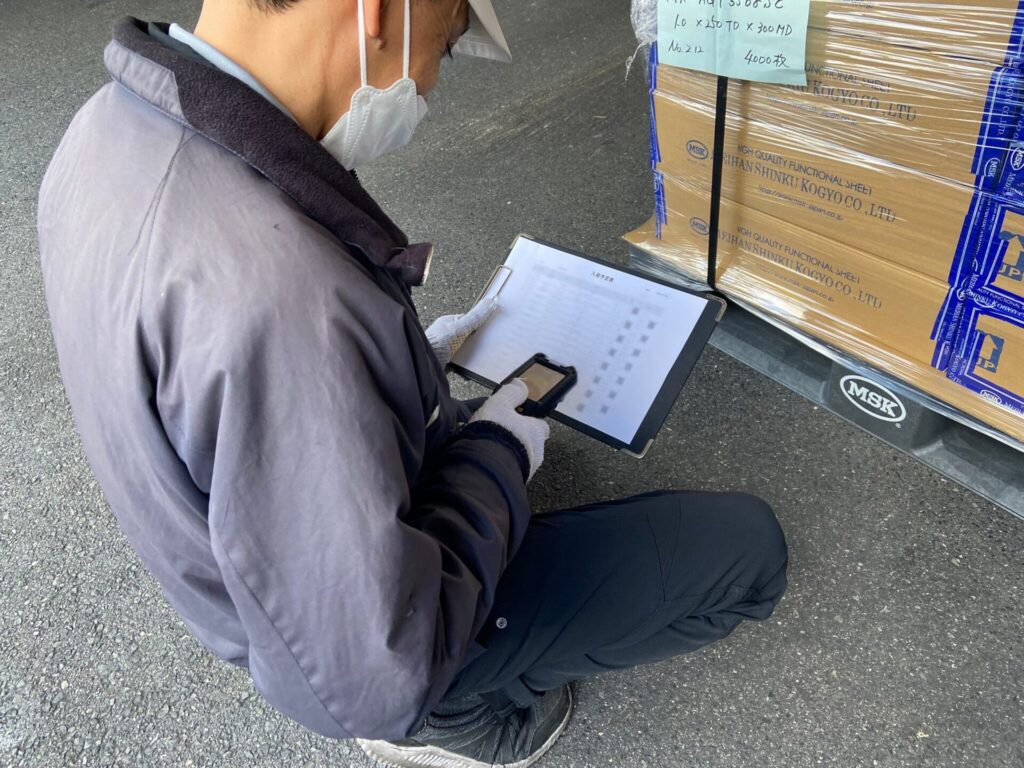
【入荷管理】スマートF導入前後の変化
入荷品を保管後、納品書をもとに入荷数をエクセル手入力
↓
入荷したその場で、ハンディーターミナルで入荷登録(手入力の手間はゼロに)
製造現場への在庫移動においてもエクセル手入力作業が不要に
【導入前】在庫移動もエクセルの在庫管理表に手入力、リアルタイムに製造現場の在庫状況が確認できなかった
倉庫から製造エリアに必要部品を払い出す際は、生産管理担当者が部品リストをもとに移動依頼書を作成し、それに基づき倉庫担当者がピッキングを行う。そしてピッキング後に、エクセルの在庫管理表へ移動実績を手入力していた。この作業を各拠点で毎日行っており、入荷作業と同様にデータ入力の手間やミスが課題だった。
また、製造現場の在庫状況がリアルタイムに把握できないため、払出指示をしたものの製造現場には在庫が十分ある、というケースも度々あった。逆に、あるはずの原材料在庫が現場になく、工程調整が必要になったこともあった。
【導入後】在庫移動のエクセル管理もなくなり年間360時間の工数削減
ハンディーターミナルで払出処理を行うようになり、在庫の移動情報もリアルタイムに更新できるようになった。
移動情報はハンディーターミナルからスマートFへ即座に反映されるため、移動実績をエクセルに手入力する手間は一切不要に。エクセルの手入力作業がなくなったことで、全拠点で年間360時間の工数削減に繋がった。
【在庫移動】スマートF導入前後の変化
ピッキング後、移動実績をエクセルに手入力
↓
ハンディーターミナルでリアルタイムに払出登録(手入力の手間はゼロに)
棚卸しの棚札手書き作業やデータ手入力のシステム化に成功
【導入前】棚卸しは棚札を用いて丸1日、その後の棚卸データは手入力で5営業日かかっていた
従来の年次棚卸では、全工場の生産を止め、丸1日かけて行っていた。各在庫の数量確認後、複写式の棚札を各在庫に貼り付けていき、すべて数え終わったら複写1枚目を回収し棚卸しデータを手入力していた。この棚卸データの入力作業は、約5営業日ほどかかっていた。
さらに、棚卸準備にも半日〜1日が必要だった。棚札の使用予定数の集計や発注、1枚ずつに担当者印を押印するなどの手間があった。
この一連の棚卸は、工数が膨大なだけでなく、ヒューマンエラーが防ぎづらいという課題もあった。手書きの棚札では書き損じや読み間違いが起きやすく、データの手入力もミスを防ぐことが難しかった。
【導入後】紙の棚札運用・棚卸しデータ入力が不要になり、約100時間の棚卸工数削減&約300万円の経費削減
紙とエクセルで行っていた棚卸しを、スマートFとハンディーターミナルで実施する運用に変更。今まで丸1日かかっていた棚卸しは、2時間程で終わるようになった。
さらに、現場でのハンディーターミナル作業で即座に棚卸データを登録できるようになり、データ手入力の作業も不要になった。これにより、各拠点で棚卸しを終えた後は、棚卸しデータをCSV出力し、当日中に経理へ渡すだけで済むようになった。
これらの結果、全拠点で棚卸工数を約100時間削減できた。
また、棚卸にかかる実質的な人件費の圧縮にくわえ、棚札購入が不要になった分も合わせると、300万円近くの経費削減にも繋がった。
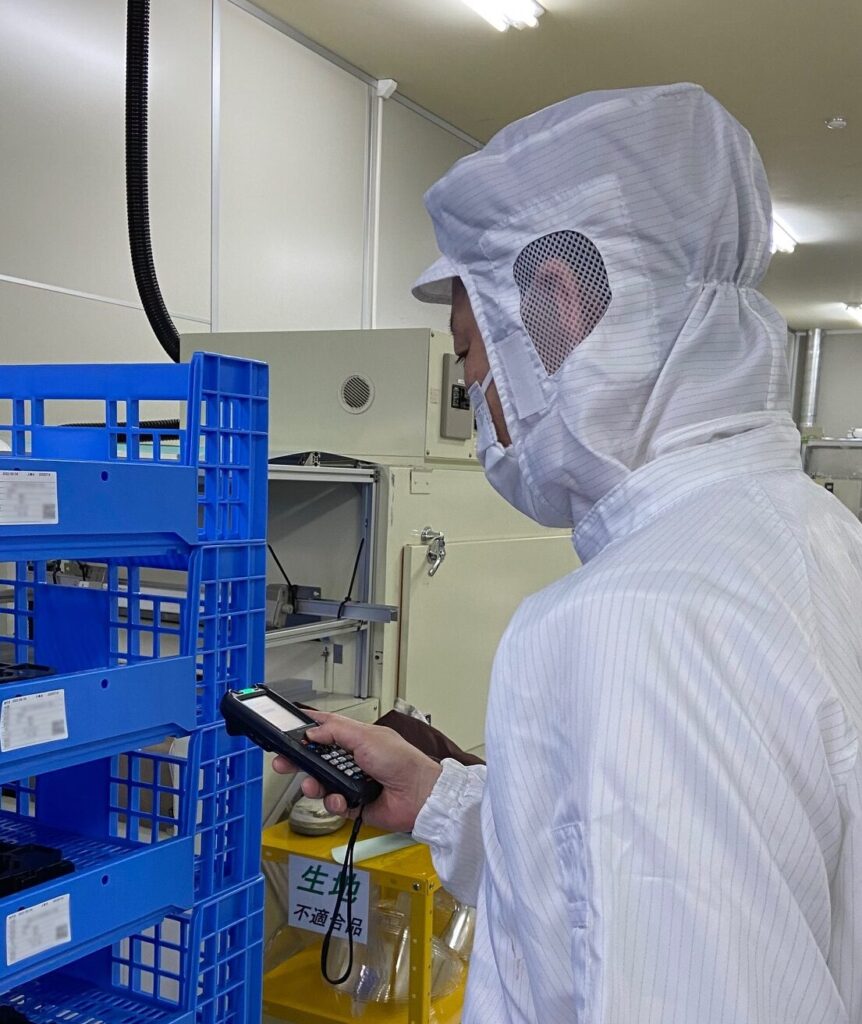
【棚卸し】スマートF導入前後の変化
■棚卸準備
複写式の棚札の数量確認や発注、棚札1部ずつに担当者印の押印etc. (半日)
↓
棚札の準備は不要に
■棚卸当日
各在庫の数量確認→棚札を在庫に貼付→棚札回収(丸1日)
↓
ハンディーターミナルで棚卸登録(棚差はその場でデータ修正)
■棚卸後
棚卸データを各拠点で手入力し、経理へ提出(約5営業日)
↓
スマートFから棚卸データをCSV出力し、経理へそのまま提出(データ手入力は一切なし)
毎日行っていた現場への実在庫数の確認が不要に
【導入前】正確な在庫を知るため、現場に実在庫数の確認を毎日依頼していた
エクセルの在庫管理表のリアルタイム性・正確性が低かったので、発注前は倉庫に都度電話し、現場の実在庫数の確認を依頼していた。このやりとりがほぼ毎日発生していた。
【導入後】スマートFで正確な在庫情報を照会できるようになり、現場問い合わせの工数を年間約100時間圧縮
全拠点の在庫をスマートFで一元管理し、リアルタイム更新まで実現。在庫確認のために倉庫へ問い合わせる必要がなくなった。各拠点で1日約5分の在庫確認が発生していたと仮定すると、年間で約100時間の工数圧縮に成功した。
【実在庫確認】スマートF導入前後の変化
発注前に在庫数を現場へ確認(毎日)
↓
スマートF上で最新の在庫情報をすぐに確認(現場へ問い合わせる必要なし)
お客様の声
小さく導入できるのはメリットが大きいと感じた
まずは在庫管理から現場をシステム化し、エクセルの在庫管理表の運用をなくすことができました。フルカスタマイズのシステムだと、初めに全要件を決めないといけませんが、スマートFだと「まずはここからやってみよう」と小さく始め、段階的にシステム化を進められます。これは、大きなメリットだと思います。
とはいえ、当社は個々人が独自のエクセルで在庫管理をしている状況だったので、導入前のマスタ整備は少し大変でした。基幹システムとの連携を考慮してマスタ整備をする必要があったのですが、導入支援担当の方はそれも踏まえて支援してくださいました。連携周りで難しい要望を相談した際も、当方がやりたい運用を実現していただきました。
営業担当の方も、稟議で必要な資料を細かく揃えていただくなど、柔軟にサポートしていただきました。提案から導入まで、柔軟でスピーディーに対応していただき助かりました。
少しずつ機能拡張し、自社のペースで生産管理システムを作り上げていく
今後もスマートFの機能追加を進め、幅広い生産データを一元管理できる生産管理システムとして完成させていく予定です。既に在庫管理にてハンディーターミナルやシステムの運用に慣れることができたので、他の機能もスムーズに導入できると思います。
まず次のステップとしては、受注管理と工程管理への拡張を検討中です。紙で行っている生産記録や各検査項目、使用原料のロット管理をシステム化することで、よりトレーサビリティを強化していきたいです。
そして、工程管理までシステム化できた後は、アナログ管理では難しかった原価管理まで実現したいと考えています。原材料の価格変動も大きい中、精緻な原価管理にはシステムの力が不可欠です。引き続き、ご支援の程宜しくお願いします。
株式会社ネクスタ:営業担当の声
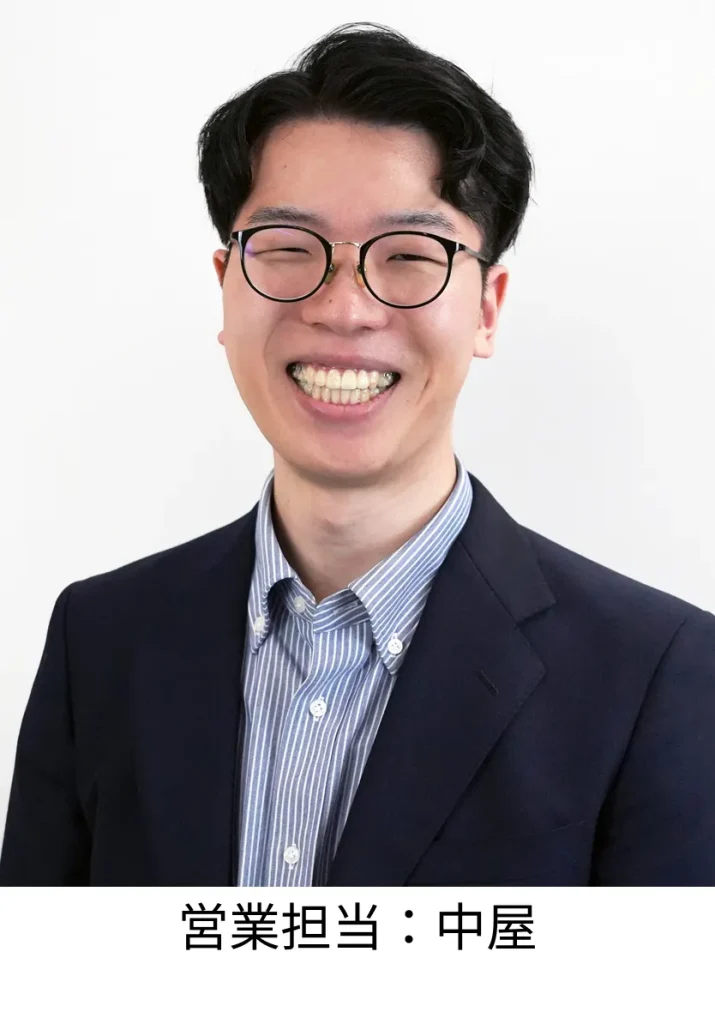
私が名阪真空工業様のもとへ初めて訪問した際、業務課題の深さと広がりが印象的でした。SmartFの特長と、名阪真空工業様の課題が見事にマッチしていたため、導入効果には大きな手応えを感じていました。
一方で、大規模なシステム導入に対する不安の声も率直に伺いました。そこで提案したのが、段階的な導入アプローチです。
各ステップの具体的な導入機能と期待される効果、そして投資対効果を綿密に分析し、明確な導入ロードマップをご提示させていただきました。
お客様には「現場での確実な運用」と「具体的な投資対効果」の両面からご納得いただき、導入のご決定につながりました。
このたびシステムが無事本稼働を迎え、私自身、大きな喜びを感じております。今後、工程管理システムの展開まで実現できれば、さらなる業務改革の実現が期待できると確信しています。
株式会社ネクスタ:導入支援担当の声
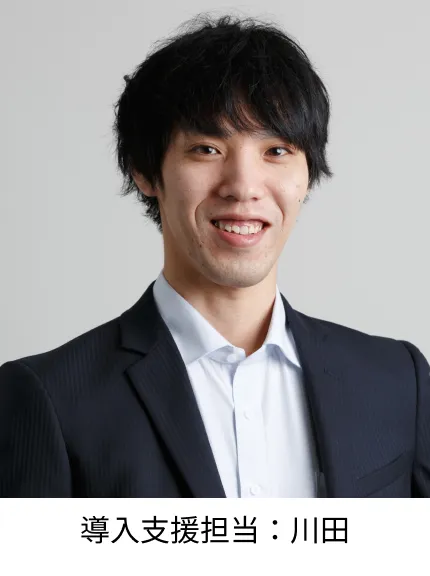
【運用提案する上で心掛けたこと】
各種マスタの登録について手戻りができるだけ発生しないように、段階的な機能展開を見据えた提案を心掛けました。
また、基幹システムと会計システムとのデータ連携が必要でしたが、お客様のご希望を手間なく実現できるような連携仕様をご案内できたと思います。
【導入時を振り返って】
各工場へ訪問させて頂き、現場の作業者の方に直接操作説明をさせて頂きました。今回のステップでは、モノの入庫と出庫だけのシンプルな機能の導入だったこともあり、順調に全工場で本稼働をして頂くことができました。
次の機能展開に向けて、さらなる改善をご提案できるように進めていきたいと思います。