2023年12月27日
【生産管理システム】部材引落による生産工程と在庫数の連動管理を実現!
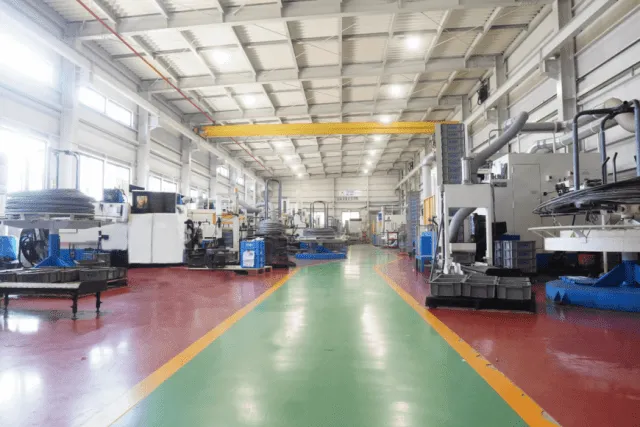
金属部品製造会社
業界 | 金属加工業界 |
---|---|
会社規模 | 30~99人 |
機能 | 在庫管理、工程管理、生産管理 |
システム概要
課題
- 仕掛品・完成品の在庫数は、生産管理に都度問い合わせていた
- 生産進捗を確認する手間が毎日発生
- 材料の入荷情報は納品書からエクセル転記、タイムリーな管理が難しい
解決策
- 部材引落機能で在庫管理を自動化
- 各生産工程に工程管理システムを導入
- 入荷検品をシステム化
効果
- 部材引落による正確なシステム管理を実現、月2時間前後の工数削減
- 毎日の進捗確認が不要になり、年間約100時間の工数を削減
- スマートF連動の入荷検品を導入、年間約36時間を割いていた転記作業がゼロになる見込み
導入の背景
既存の生産管理システムの老朽化をきっかけに、新システムを検討
ねじ製品の製造を80年以上にわたり手掛け、現在は多品種小ロット製造に強みを持つ同社。以前使用していた生産管理システムの老朽化を機に、新しいシステムを3社比較したうえでスマートFに決めていただきました。
スマートFの導入前に使用していた生産管理システムは、2008年に導入したものです。大掛かりなカスタマイズを施して導入した、当時700~800万円のパッケージソフトでした。2015年頃からWindowsのバージョンアップが重なり、このシステムがうまく動作しなくなってきたため、新しい生産管理システムの検討をすることになりました。
この度のシステム検討で特に重視されたのは、在庫管理機能です。今までの生産管理システムでは、仕掛品や完成在庫品の数量を管理できず、別途エクセル管理が必要だったからです。この在庫管理もシステム化することを重視し、最終的にはスマートFを含め3つのサービスで比較しました。
3社のうち1社は、大手パッケージソフト。サーバー設置費や開発費などの初期費用が膨大で、自社仕様にカスタマイズする費用も高額。トータルで約2,000万円の予算が必要とのことで、検討が難しい状況でした。また、過去に他の大手生産管理システムの話を聞いたことがあったものの、自社には大手のソフトが合わない感覚があったのも気がかりでした。
もう1社、スマートフォン操作が強みの生産管理システムも検討しました。利便性は魅力的だったものの、最も重視していた在庫管理機能が不足していると判断し、こちらも見送りとなりました。
スマートFに決めた理由
低コストなだけでなく、運用面や対応力にも安心感があった
まず、スマートFはコストの低さが非常に魅力的でした。クラウド型で自社サーバーの構築・保守が不要、かつ高額なカスタマイズなしで自社の運用に合わせた使い方ができるので、初期費用・ランニングコスト共に抑えられました。
また、導入検討時に営業担当者へ、他社にできないと言われた機能について相談したところ、「対応できます」とすぐに答えてもらえた点も安心でした。今回求めていた在庫管理においても十分な機能が揃っていると判断し、スマートFへの切り替えを決めました。
導入効果
【導入前①】仕掛品・完成品の在庫数は、生産管理に都度問い合わせていた
工程以降の仕掛品や完成品の在庫は管理できなかったため、別途エクセルで管理していた。エクセル管理は毎日行っており、1日に平均20分の時間がかかる。
また、エクセルでの管理だと他の従業員との情報共有が難しく、作業者だけが各在庫を把握しているという属人的な状態だった。そのため、リアルタイムに在庫数を知りたいときは、生産管理の担当者に都度問い合わせる必要があった。この在庫確認作業を必要に応じて平均週1回ほど行っており、1回の確認にかかる時間は20分程度。在庫実数の計量が必要になるときは、40分ほどかかることもあった。
【導入後①】部材引落による正確なシステム管理を実現、年間約30時間の工数削減
スマートFによるシステム管理で、在庫の見える化に成功。部材引落に関しても、第一工程で使用する材料だけでなく、仕掛品やアッセンブリーに使う部品、完成品までカバーできるようになった。特に、今まで在庫管理できていなかったアッセンブリー用の部品も、部材引落で手間なく在庫管理できるようになったのは助かる。
部材引落のために、生産で使う材料や部品は完成品に紐づけてマスタを登録。これにより、現場で各工程を完了するごとに完了登録を行うと、使用した部材が自動的に引き落とされていく仕組みを確立した。
これらの在庫管理のシステム化で、週に1回、20〜40分かかっていた仕掛品や完成品の在庫確認作業がなくなった。エクセルのみの管理に比べて、データ消去や破損のリスクも低くなったと感じている。
現在はデータの正確性を担保するため、従来のエクセル管理も並行して行っているが、今後スマートFのみで管理していく予定。エクセルでの在庫管理がなくなれば、さらに年間80時間の工数削減が見込まれる。
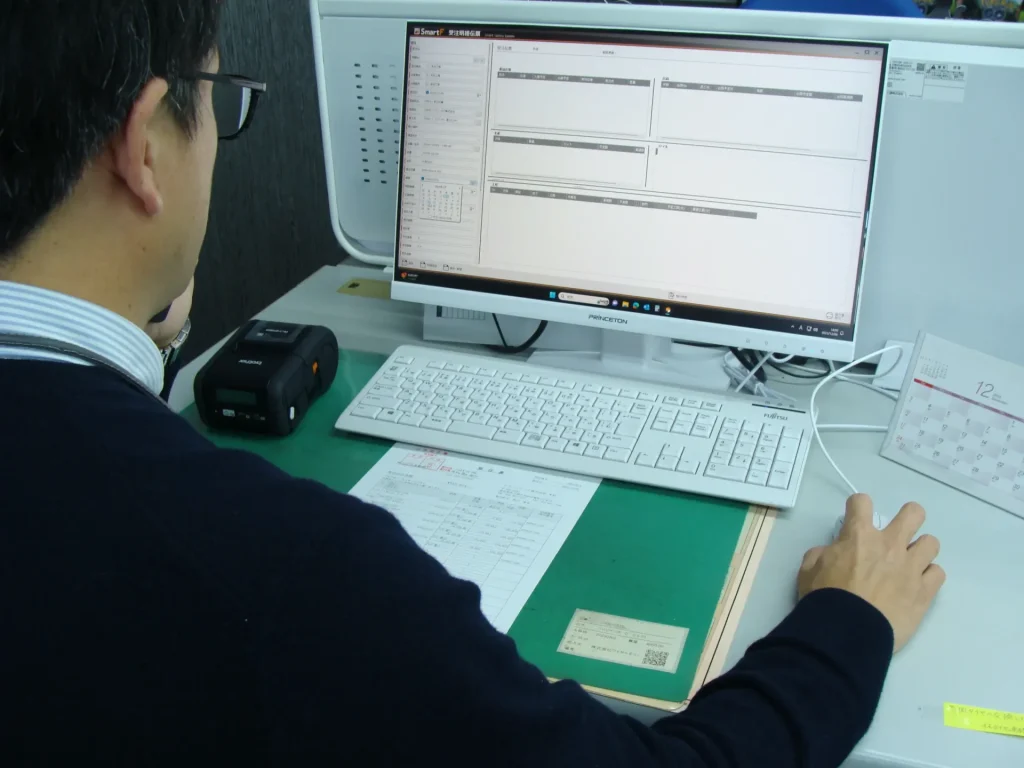
【導入前②】生産進捗を確認する手間が毎日発生
以前の生産管理システムでも工程進捗は確認できたが、最終工程が終わっているかどうかしか見られなかった。たとえば、途中で外注工程を挟む製品は、外注先から完成品が返ってきているかどうかを把握できなかった。
生産途中での入出庫情報はエクセルに記録していたが、リアルタイムに工程を確認できないという課題があった。短納期品の生産中や、工程途中で1日の作業を終える日など、タイムリーに進捗を確認したいときは生産管理に直接聞く必要があった。計5名の営業が各自、この進捗確認を毎日5分程度かけて行っていたため、合計で毎月8時間以上の工数がかかっていた。
【導入後②】毎日の進捗確認が不要になり、年間約100時間の工数を削減に期待
スマートFによる作業管理を全工程に導入。以前の生産管理システムで確認できなかった、生産途中の進捗もリアルタイムに見える化できた。具体的には、各工程の作業開始・終了時にスマートFに作業登録し、その情報がスマートF上でいつでも確認できるようになっている。その結果、毎日5名の営業が生産管理に進捗確認する手間が不要になり、毎月8時間以上、年間だと100時間もの工数削減に繋がることが見込まれる。
また、スマートFの画面が見やすく使いやすいとも感じている。旧生産管理システムでは、各工程の項目を毎回クリックして詳細画面を開く必要があったが、スマートF上では一覧で全体の進捗を確認できる。
【導入前③】材料の入荷情報は納品書からの手打ち転記、タイムリーな管理が難しい
以前の生産管理システムでも材料の入荷管理はしていた。しかし、仕入先からの納品書をもとにエクセルに入力し、その後システムに転記するというアナログな手順で情報を取り込んでいた。
この作業は月3回に分けて行っていたため、入荷情報が反映されていないタイムラグが発生していた。たとえば、実際に材料が入荷し生産工程で使い始めても、システムに入荷数量を反映していないと、材料数がマイナス表記になる。
さらに、この転記作業は1回につき1時間以上かかり、年間36時間の工数がかかっていた。また、入力ミスをゼロにできないなど、アナログ管理ならではの課題もあった。
【導入後③】スマートF連動の入荷検品を導入、年間約36時間を割いていた転記作業がゼロに
スマートFと連動した入荷検品をスタートし、入荷情報が自動的に登録されるようになった。リアルタイムに入荷数が反映されるようになったので、仕入先からの納品書のエクセル・システムへの入力作業は一切不要になる見込み。転記作業そのものがなくなることで、入力ミスの課題解消も期待できると思われる。
お客様の声
スマートFの検討時だけでなく、導入決定後も導入支援担当の方にさまざまな要望をご相談させていただきました。思い返すと度々無理を言ったなと感じますが、一つひとつ対応していただいたお陰で、無事に本稼働できました。現在は、生産管理や在庫管理だけでなく、受発注管理もスマートFを活用しています。
また、不良製品の管理にも、スマートFを使っています。品質に力を入れる中で「不良データをしっかり取る」という会社の方針があり、以前から不良の集計はしていましたが、スマートFでより細かく管理できています。不良リストを一覧で確認できるので見やすく、CSV出力すれば編集も簡単にできます。今後、品質会議で使う不良統計資料としても活用していけそうです。これからもスマートFをより活用していき、業務効率化を推し進めていきたいです。
株式会社ネクスタ:導入支援担当の声
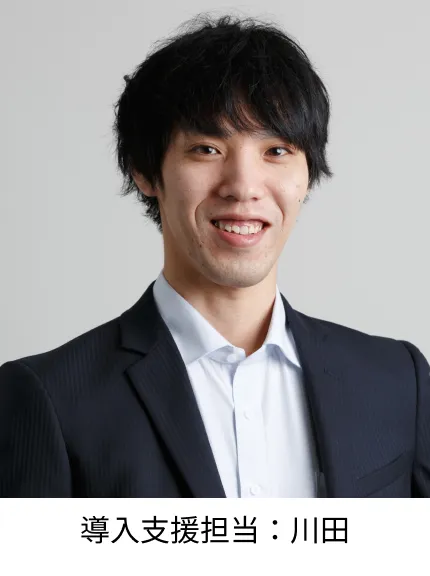
【運用提案する上で心掛けたこと】
既存システムやエクセルの運用からスマートFに置き換えるため、導入検討をされていました。既存の運用やご要望をしっかりヒアリングし、お客様の運用に沿った操作フローを提案するよう心がけました。
【導入時を振り返って】
マスタ作成や現場操作にお時間が必要な中、ご担当者の方にも推進して頂き、無事スマートFを本稼働できました。ご満足頂ける運用フローにできたかと思います。