2024年06月07日
【在庫管理システム】将来在庫の自動計算で発注の負担・工数を削減!生産計画と在庫を紐づける管理を実現
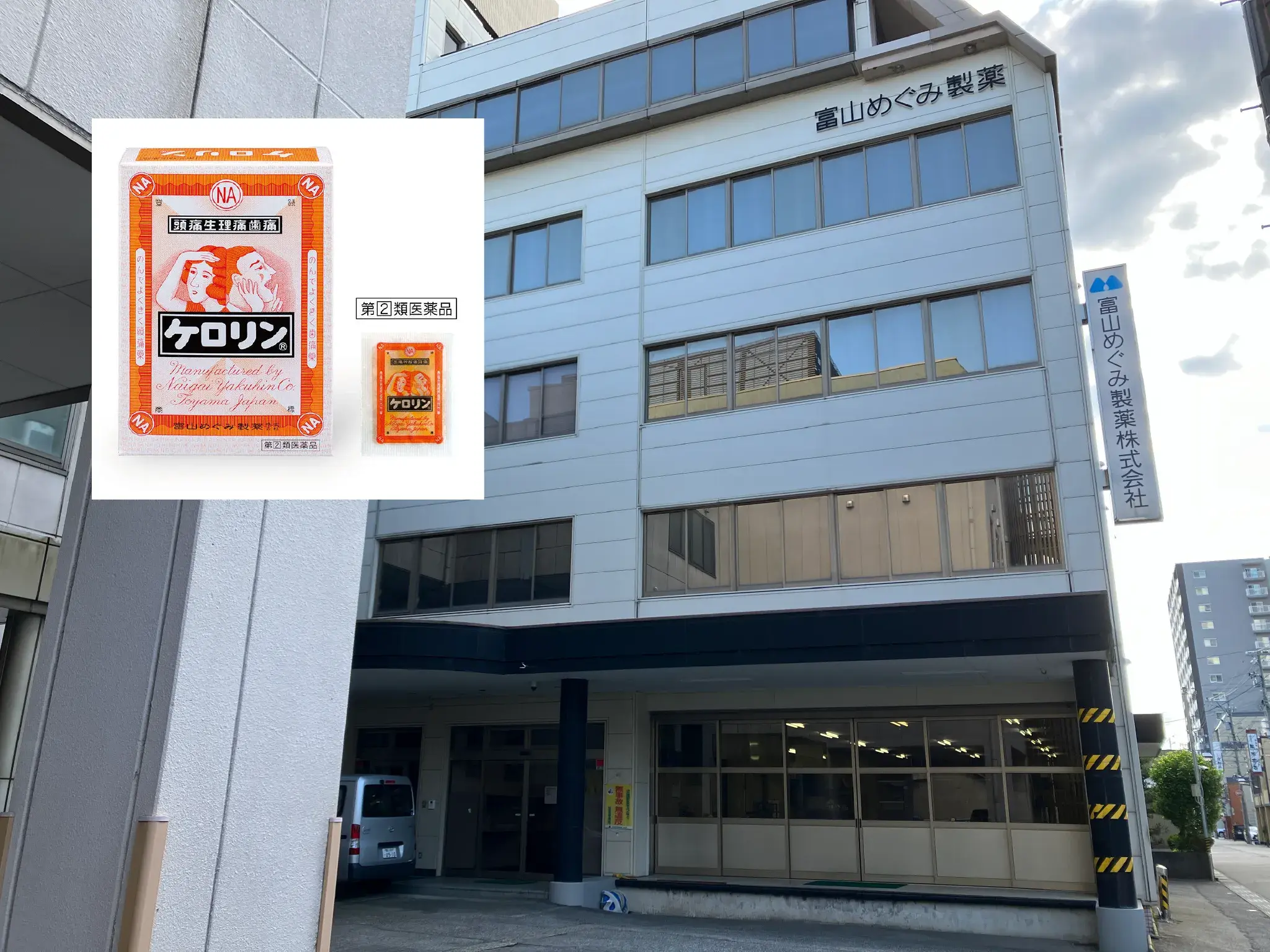
富山めぐみ製薬株式会社
業界 | 医療・医薬品業界 |
---|---|
会社規模 | 30~99人 |
機能 | 在庫管理、工程管理 |
システム概要
課題
- エクセルの生産計画表と現在庫数を突き合わせ、手作業で計算
- 経験や記憶による発注作業で分業が難しく、残業が生まれていた
- リードタイムの長い品物は、発注ミスが生産にも影響することがあった
解決策
- スマートFで生産計画データと在庫データを一元管理
効果
- スマートFに生産計画データを取り込み、将来在庫を自動計算
- 発注業務のシステム化&分業化に成功、発注による残業をゼロに
- 発注漏れやミスはゼロに、作業者の心理的負担も軽減
導入の背景
将来在庫が見える在庫管理で、生産計画と紐づいた発注業務を実現したかった
「ケロリン」シリーズをはじめ、さまざまな医薬品の製造・販売を行う、富山めぐみ製薬株式会社様。同じ在庫システムを20年以上使い続ける中で、将来在庫をふまえた発注業務に課題を持っていました。
同社では、一つの原料や資材を複数の製品に使うことが多いため、生産計画に基づく将来在庫を把握したうえで発注する必要があります。しかし、従来の在庫管理システムでは将来在庫の算出ができず、エクセルの生産計画データとシステム上の在庫を突き合わせて計算する必要がありました。属人的で煩雑な作業のため、発注漏れや発注ミスも度々起きていました。
特に、発注リードタイムが長い原材料では、3〜6ヶ月後の在庫状況を知る必要があり、発注漏れの影響も大きくなります。ミスができない作業は、作業者の心理的な負担にもなり、発注のために残業をせざるを得ない日もありました。生産と紐づけた発注を実現するため、システムの見直しを検討し始めました。
スマートFに決めた理由
求める運用が低コストに実現でき、トライアルも可能だった
低コストかつトライアル可能で、必要な機能に絞って導入できる点で、スマートFに決めました。
はじめは、既存の在庫管理システムのグレードアップを検討しました。しかし、グレードアップには追加費用が数千万円かかることがわかり、より低コストのシステムを探し始めました。しかし、製薬業界でシステムの追加や置き換えを行うと、GMP対応が必要となり、導入工数が膨らんでしまいます。
スマートFなら、GMP管理の対象となる業務(原料のロット管理や帳票管理など)は引き続き既存システムを使い、将来在庫と発注計画の見える化を実現する機能のみ部分導入が可能でした。GMP対応を考慮せずにシステム導入できたことで、手間とコストを最小限に抑えられました。
また、既存システムと問題なく併用できるかという不安もあったので、トライアル導入ができる点も非常に魅力的でした。そして、トライアルを通してスマートFの効果性を実感し、本格導入を決めました。
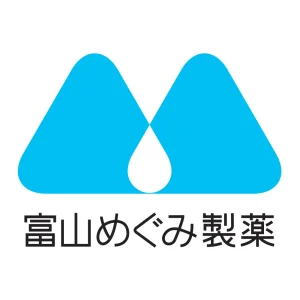
導入効果
将来在庫の見える化と自動計算を実現
【導入前】エクセルの生産計画表と現在庫数を突き合わせ、手作業で計算
従来の在庫管理システムには将来在庫を計算する機能がないため、発注のたびに手作業で計算していた。一つひとつの原材料や資材ごとに、エクセルで作成した生産計画から将来必要になる数量を確認し、従来の在庫管理システムの在庫数と突き合わせて計算する必要があった。この作業を、毎月1回行っていた。
【導入後】スマートFに生産計画データを取り込み、将来在庫を自動計算
スマートFにエクセルの生産計画表を取り込み、在庫データと紐づけることで、生産計画と連動する在庫管理を実現。将来在庫はスマートF上で自動計算されるようになり、手作業での計算は一切不要となった。製品完成後にスマートF上で完了登録をすることで在庫も引き落とされ、生産による在庫数の変動も自動反映できる。
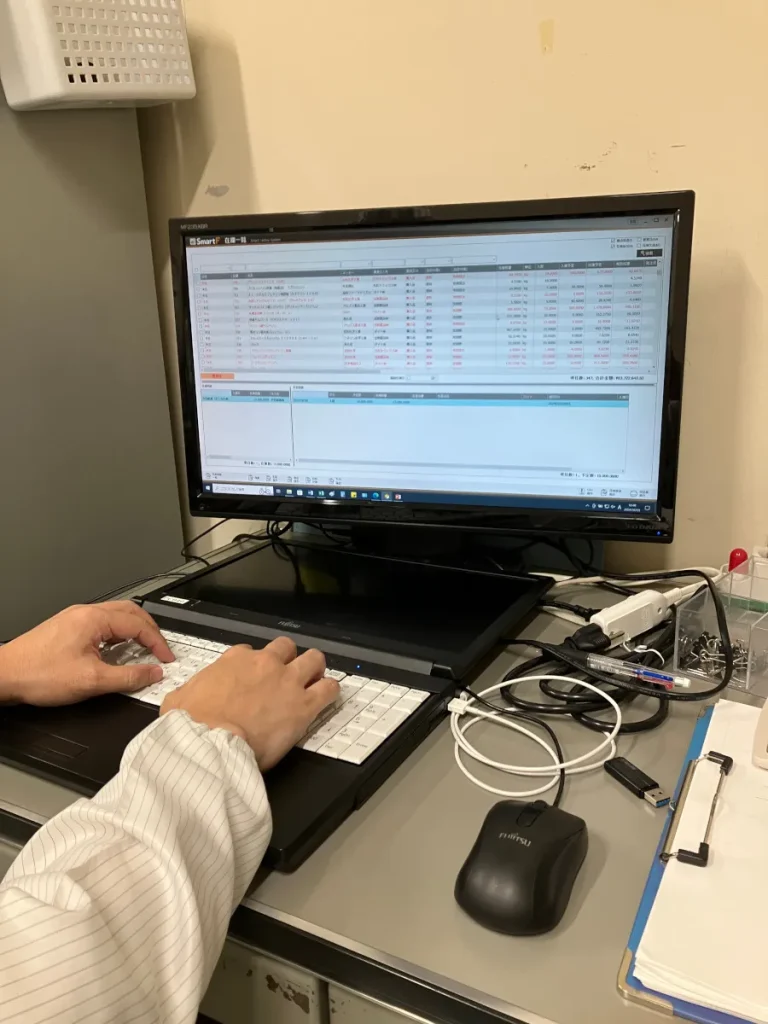
属人的な発注業務を分担可能にし、工数削減や心理的負荷の軽減にも成功
【導入前】経験や記憶による発注作業で分業が難しく、残業が生まれていた
月1回、将来在庫を計算した後、実際の発注作業も手作業で行っていた。1つの製品を作るために10〜20種類の原料・資材が必要になり、毎月およそ10製品の見込み生産をするため、100種類以上の原料・資材の将来在庫を計算しなければならなかった。一度の発注作業に3時間はかかり、作業者の残業にも繋がっていた。
また、従来の発注フローだと、生産計画を立てた人しか必要発注数を把握できず、分業が難しかった。各品物のリードタイム管理や適正在庫の維持も、作業者の経験と記憶が頼りで、発注業務全体が属人化していた。
【導入後】発注業務のシステム化&分業化に成功、発注による残業をゼロに
スマートFでの在庫管理で、指定した未来日付の在庫数を一目で確認できるようになった。各発注品のリードタイムや発注点を登録し、2〜3ヶ月後に発注点を下回る品物を随時発注するという運用に変更した。
発注点管理のシステム化により、毎月3時間かけて行っていた発注作業は、都度確認で発注するだけでよくなった。発注業務を標準化したことで、3名で分担できるようになった。これにより、発注業務による残業もなくなった。
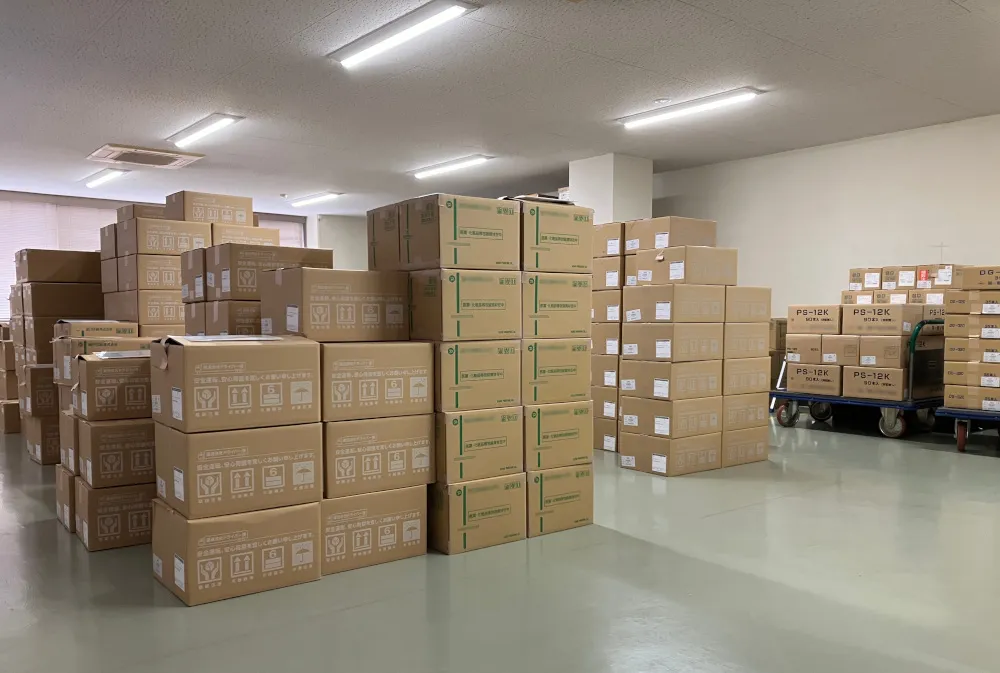
年に数回発生していた、発注漏れ・ミスは0件に
【導入前】リードタイムの長い品物は、発注ミスが生産にも影響することがあった
リードタイムの長い原料や資材は、発注漏れが起きると生産に影響する可能性があるため、作業者にとって神経を使う業務でもあった。実際に、年に数回は発注ミスが起きていた。
【導入後】発注漏れやミスはゼロに、作業者の心理的負担も軽減
スマートFで在庫や発注の状況を見える化し、リードタイムが長い品物の発注状況も簡単に確認できるようになった。発注漏れなどの発注ミスは0件となり、作業者は「在庫がリアルタイムに見える」という安心感を持って、発注業務を進められるようになった。
お客様の声
製造部 部長 田中様
製造部に異動してから現場の在庫管理に課題を感じ、システムを探し始めました。スマートFは、当社が実現したい運用ができそうだと感じたのと、トライアルから始められる点が魅力でした。スマートFを通して将来在庫を見通せるようになり、発注業務のストレスが本当に減りました。
導入に際し、営業や導入支援、プロダクトサポートの担当者の方々とやりとりをしましたが、どの方もスムーズな対応をしていただけました。
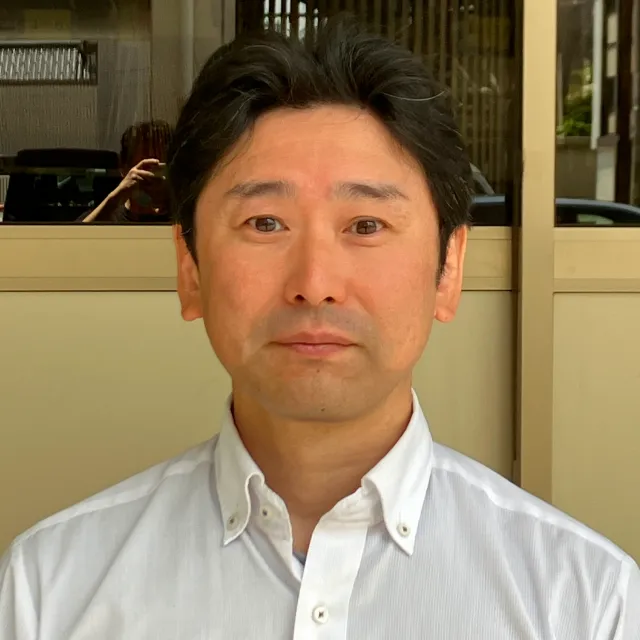
株式会社ネクスタ:導入支援担当の声
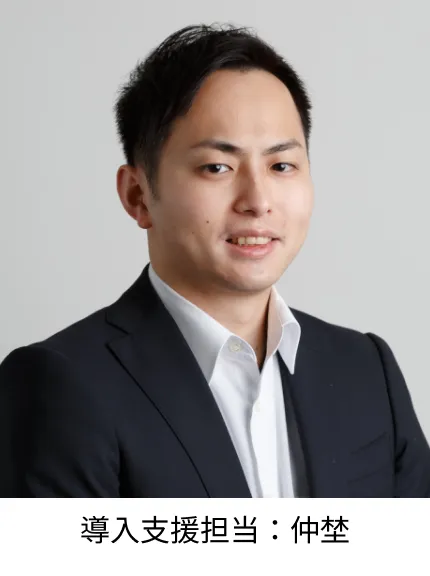
【運用提案する上で心掛けたこと】
導入の背景にある課題を、いかに解決するかを意識しました。スマートFではハンディ端末での照合なども得意部分ですが、今回は構成部材をすべて自動で引き落とし、各原料の在庫数をリアルタイムに反映、発注業務が簡素化できるような運用をご提案しました。
【導入時を振り返って】
課題や質問、相談事項があればすぐにご連絡をいただき、また、回答に対するレスポンスも非常に速く、要件の確認等が非常にスムーズにできました。
現場の担当者様も、現状の課題解決のためという共通認識のもと、新しいシステムを積極的に使用して頂き、大きな課題が発生することなく導入していただけました。