2024年04月15日
【化粧品/原料在庫管理システム】誤使用・誤投入0件、年間損失額の数千万円が0円に!ハンディ端末で工数削減・属人化解消も成功
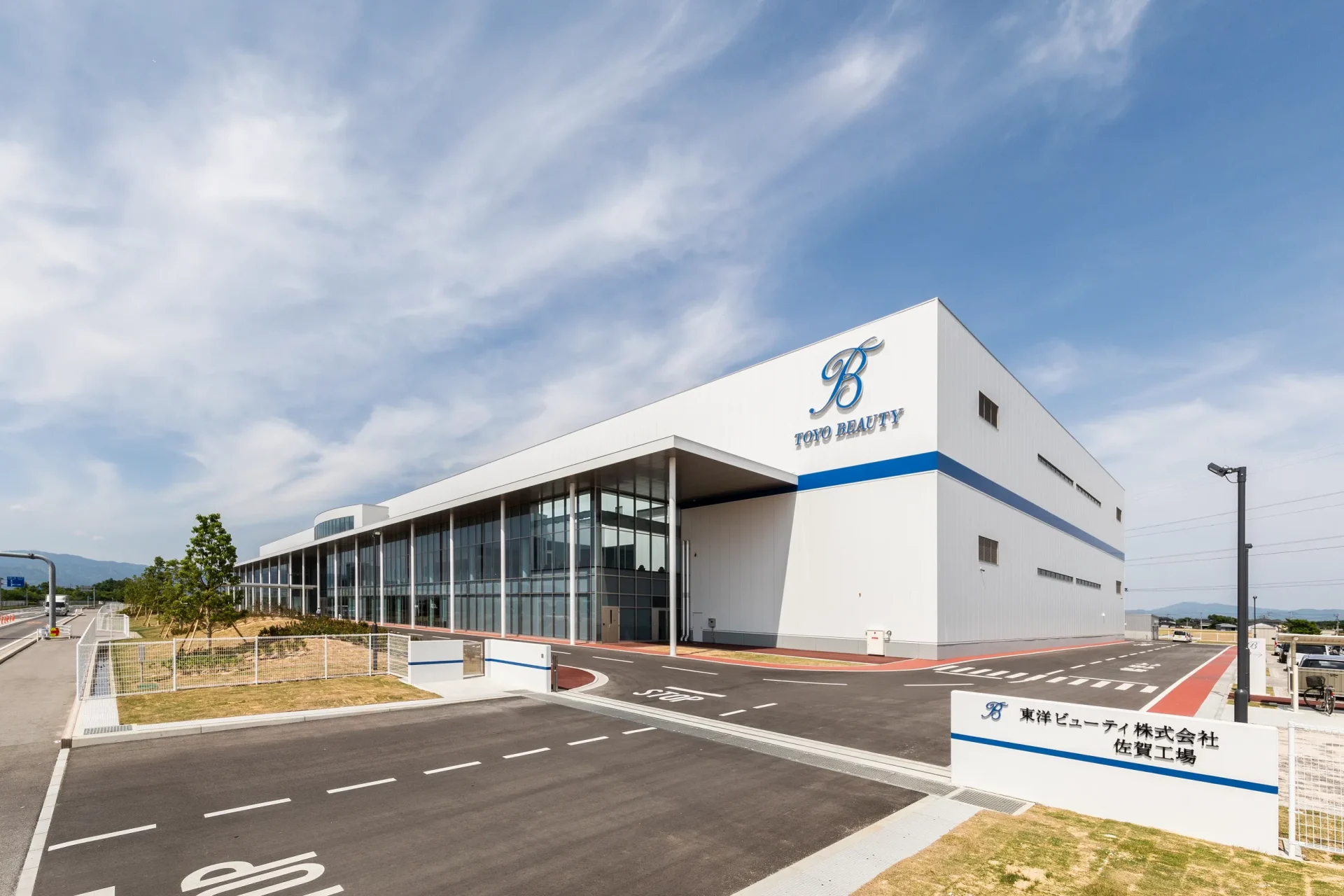
東洋ビューティ株式会社
業界 | 化粧品業界 |
---|---|
会社規模 | 500~999人 |
機能 | 在庫管理 |
システム概要
課題
- 原料の取り違いやロットミス等が年間5件程発生しており、年間損失額は数千万円に上っていた
- 基幹システム上と実在庫で、期限や検査状態に差異が生じるときがあった
- 管理者のみが原料の保管場所や実在庫を把握している属人的な状態
- 工場を全停止して連休に一斉棚卸、1チーム3人体制で完了まで4~5日かかることもあった
解決策
- 現場にスマートFを導入し、在庫管理をシステム化
- ハンディーターミナルによるバーコード管理を導入
効果
- ハンディーターミナルによる期限・検査状態管理を活用し、全工場で誤使用・誤投入は年間0件、年間損失額も0円になった
- 最新の原料ステータスをリアルタイムに把握できるようになった
- スマートF上で、誰でも現時点の実在庫数や保管エリアを確認できる体制を実現
- 棚卸は1人で完結、工場を全停止しない循環棚卸で半期決算棚卸が1.5日で完了
導入の背景
扱う原料が増えるにつれ管理工数も増加、現場改善を求める声が高まった
80年以上に渡り化粧品ODM・OEMを手掛ける東洋ビューティ株式会社様では、製造に関わるほとんどの作業を紙や目視確認で管理していました。しかし、扱う原料の種類が年々増え、管理工数も膨大になっていきました。近年では取扱原料が約1万品種にもなり、現場の負担は限界に近づいていました。この負荷が、不具合の原因になっている可能性もあると考えました。
このような状況を受け、いよいよ現場を効率化する必要性があるという現場からの声が上がり、生産管理システムの検討を始めました。特にニーズが高かったのは「在庫の見える化」です。どの原料がどこにあるか、期限や検査状態はどうなっているかを一元管理することで、普段の在庫管理や棚卸の負荷を減らそうと考えました。
一方、現場作業者からは、システム導入で作業工数が増えることに対する懸念の声もありました。そこで、まずは1つの工場に先に導入し、そこで効率化に成功した事例をもとに、他工場にも横展開したいと考えていました。
スマートFに決めた理由
自社がやりたい運用を実現できる柔軟性、具体的な提案、低リスクという条件が揃っていた
社内でシステム要件を整理する際、スマートFを含め計3社で比較検討しました。スマートF以外のうち、1社は既に使用していた基幹システムの機能拡張、もう1社はピッキングシステムでした。
しかし、既存の基幹システムは製造現場向けにサービスを提供した実績がなく、在庫の見える化を実現できるかが不透明でした。もう1社のピッキングシステムは、想定より規模が大きいパッケージで、一部の拠点から少しずつシステムを導入したいというニーズにフィットしづらい印象を受けました。また、同社が希望する運用に対する具体的な実例がなく、やりたい運用の実現にはハードルが高く感じたことも不安材料でした。
対して、スマートFは、機能面が十分で柔軟性もあり、同社が希望する運用を実現する具体的な提案がありました。まずは一部の拠点から小さく導入したいというニーズにも合っていました。また、同社の現場を深く理解したうえでの具体的な提案で、運用イメージを持ちやすい点も安心でした。初期費用や導入規模を抑えられるというメリットもふまえ、スマートFの導入を決めました。
導入効果
原料の誤使用・誤投入が全工場で年間0件になり、年間損失額数千万円を0円にできた
【導入前】原料の取り違いやロットミス等が年間5件ほど起き、年間損失額は数千万円に上っていた
以前は、投入現場の原料を紙で管理していた。ロットや重量などを目視確認し、処方一覧に手書きで書き込みながら調合していた。属人的な管理だったため、作業者の習熟度が効率性や正確性に影響するという課題があった。
特に、経験が浅い作業者は、類似原料の取り違いやロットミスが起きやすかった。習熟度の高い作業者は、原料の残量計算や類似品の見極めなどをすばやく正確にできる一方、新人などの経験が浅い作業者は慣れるまで時間を要する、属人的な状態も課題だった。その結果、誤使用・誤投入が年5件ほど発生し、導入前1年間の損失は数千万円あった。
また、多くの製品は、原料の投入順が変わると仕上がりが変わり、所定の規格に入らないNG品となってしまう。そのため、調合時は投入順も厳守する必要がある。一度でも工程飛ばしをしてしまうと、途中まで調合した原料を処分し、材料を取り寄せ一から作り直す必要があった。投入手順を目視確認していた頃は、作業者が強い緊張感を持って作業をしなければならなかった。
【導入後】ハンディーターミナルによる期限・検査状態管理を活用し、全工場で誤使用・誤投入は年間0件、年間損失額も0円になった
原料の入出庫・秤量・投入時に、ハンディーターミナルによるバーコード管理を導入。その結果、誤使用・誤投入・工程飛ばしの発生を防ぎ、年間の不適合件数0件を実現できた。その結果、スマートF導入前の年間損失額数千万円は、導入後に0円にできた。
原料入庫時は、受入検査で合格となった原料にバーコードを印字したラベルを貼り付ける。原料出庫時は、ハンディーターミナルで工程一覧表と出庫原料の双方のバーコードをスキャンし、取り出そうとしている原料が正しいものかどうか照合する。各原料を投入する前には、受入時に貼付した原料のバーコードをスキャンし、正しい原料かどうかをシステムにて判断できる。このバーコード管理の導入により、経験が浅い作業者も、投入ミスをする前に原料や数量、投入順の違いに気づくことができるようになった。
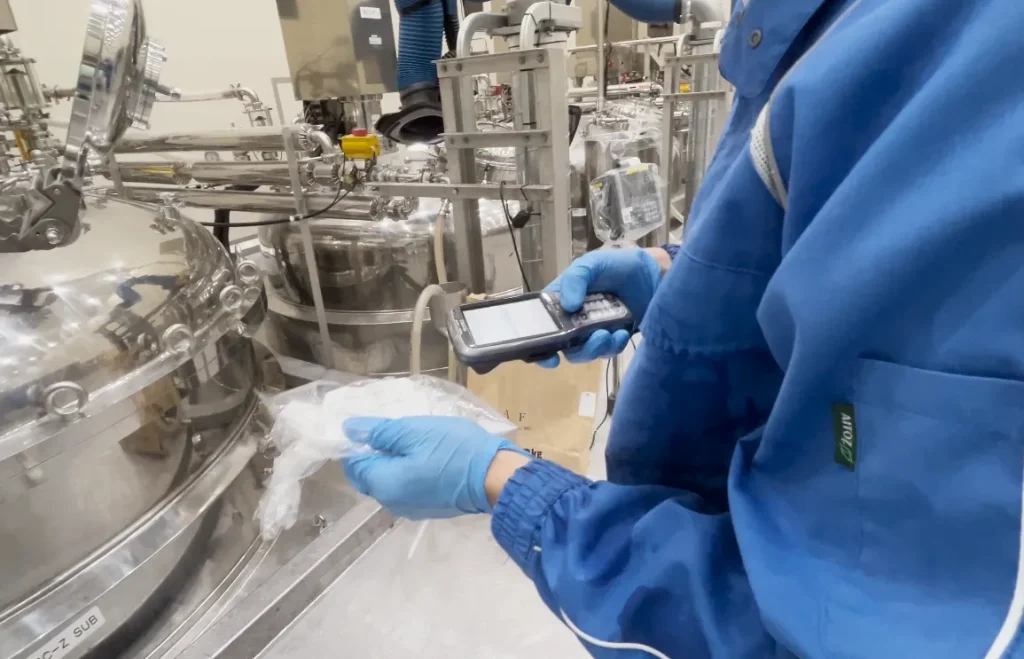
原料の有効期限や検査状態など、あらゆるステータスをリアルタイムに一元管理
【導入前】基幹システム上と実在庫で、期限や検査状態に差異が生じるときがあった
スマートF導入前は、原料の期限や検査状態は基幹システムにて記録していた。しかし、実際に現場にある原料の状態と差異が出るケースが度々あり、このステータス管理の課題も誤使用・誤投入の原因の一つとなっていた。
たとえば、同じ品番、同じロットの個体を複数エリアに保管している場合、一箇所に保管してある原料が期限切れや検査NGになると、他エリアの同ロットの原料もNGとなる。基幹システムに検査状況を記録したり、原料に不適合品の赤札をつけたりしていたものの、他のロケーションにある原料実物への情報反映にはタイムラグがあった。
【導入後】最新の原料ステータスをリアルタイムに把握できるようになった
スマートFと連動したバーコード管理により、原料のバーコードを読むだけで原料の有効期限や検査状態を即時確認できるようになった。他エリアにある同一ロットの原料にも自動反映されるため、常に最新のステータスで管理できる体制となった。
さらに、期限管理を徹底できるようになったことで、古いロットの原料から引き当てる先入れ先出しも、より管理しやすくなった。
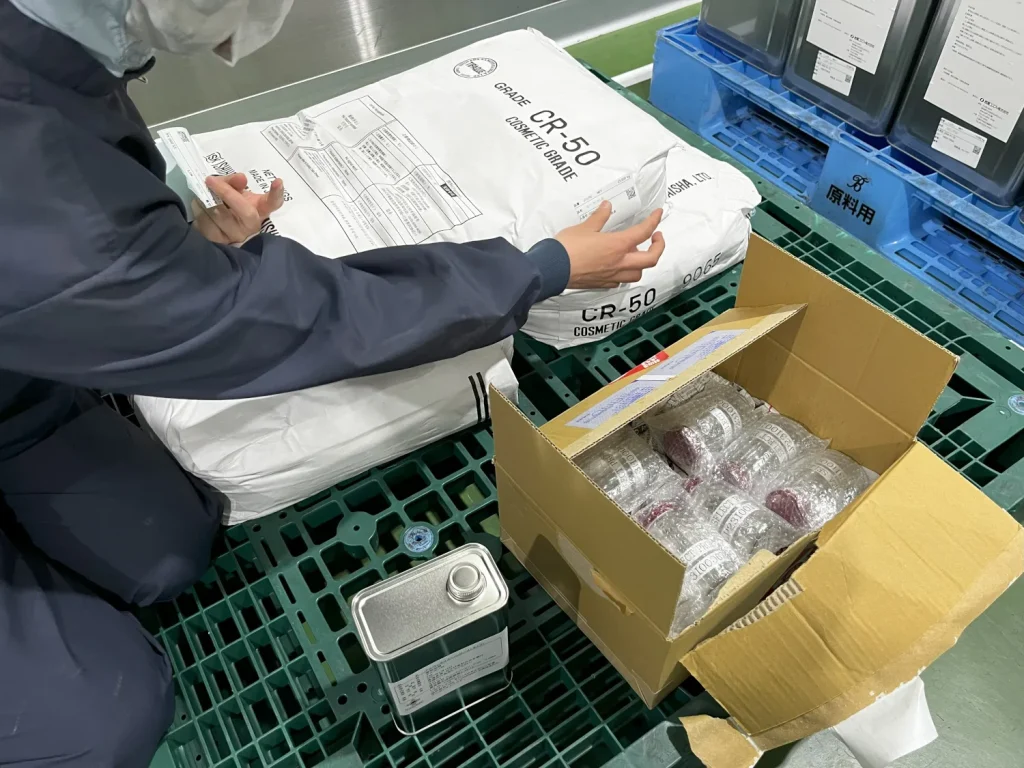
原料の実在庫の数量・エリアをリアルタイム管理、管理者以外も正確な在庫を確認できるようになった
【導入前】管理者のみが原料の保管場所や実在庫を把握している属人的な状態
スマートF導入前は、原料管理者しか正確な原料の保管場所を把握できない状況だった。たとえば、投入時に必要な量の材料がないことに気づいた場合など、担当ではない作業者が原料を探す際は、特に多くの時間を要していた。
基幹システムで、原料の理論在庫は管理していたが、部材引落の反映前などは実在庫との差異が生じていた。また、必要数の原料を取り出したつもりでも誤っていた場合など、人的ミスで在庫数がずれるケースもあった。そのため、システム上で在庫があると思っていた原料が、倉庫にはないという状況が度々あった。
【導入後】スマートF上で、誰でも現時点の実在庫数や保管エリアを確認できる体制を実現
現在は、スマートFとハンディーターミナルによる在庫管理で、各原料のロケーション情報を管理。原料を探す際は、スマートFの在庫一覧を見たり、エリアで絞り込んだりすれば、どの作業者でも原料の保管場所を簡単に見つけられるようになった。
原料の出庫時は、バーコード管理による出庫処理を行うことで、在庫の動きがリアルタイムにスマートF上に反映される。実在庫の動きがシステムと即座に連動するため、実在庫と理論在庫の差異が発生する問題も解消できた。
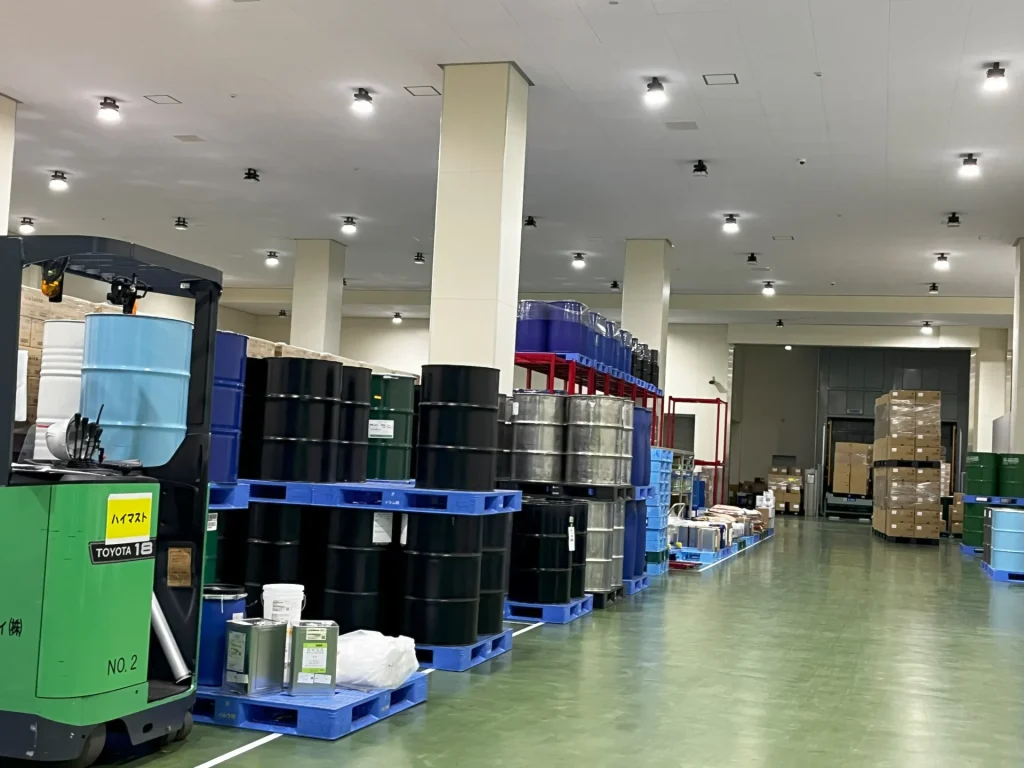
3人1チームで行っていた棚卸は1人で完結、工場を全停止しない循環棚卸で現場負荷を大幅軽減
【導入前】工場を全停止して連休に一斉棚卸、1チーム3人体制で完了まで4~5日かかることもあった
6月・12月の半期決算の棚卸では、連休中に工場の稼働を全て停止し、台帳を1点ずつチェックする実地棚卸を行っていた。原料の動きをすべて止める必要があり、現場への負担が大きかった。
たとえば、連休明けにすぐ作業をするためには、連休前にあらかじめ秤量作業をしておく必要がある。しかし、事前に秤量を済ませると、原料倉庫以外にも原料を保管することになり、ロケーション管理が煩雑になっていた。これらをすべて紙で管理するには限界があった。
実際の棚卸作業では、3人1チームで行うことが多かった。1人目は原料を取って読み上げ、2人目が計量、3人目が紙の棚卸表の束を持ち記帳するという分担を行っていた。これらの作業には、作業者の経験値によっても作業スピードや精度が左右されるという課題があった。また、工場によっては空調が効かないロケーションで長時間の棚卸を行わなければならず、作業者の負荷も大きかった。
在庫の現物確認後は、手書きで記入した棚卸表を管理者に渡し、照合確認を行っていた。基幹システム上の在庫との誤差を照らし合わせていく作業となるが、棚卸表に書き込まれた手書き文字は時折読みづらく、読み間違いや計算間違いが起きていた。計算が合わない場合は現場担当へ再確認を指示することもあり、棚卸には計4〜5日間かかっていた。
【導入後】棚卸は1人で完結、工場を全停止しない循環棚卸で半期決算棚卸が1.5日で完了
スマートF導入後の棚卸は、作業者は1名のみがハンディーターミナルを使用。ハンディーターミナル約7台を使う分担作業により、1.5日程で棚卸を完了できる体制になった。また、ハンディーターミナルでの作業は担当者の習熟度を問わず、誰でも正確な棚卸ができる。新人作業員は、ハンディーターミナルでの作業に1〜2ヶ月で慣れることができた。
さらに、ハンディーターミナル導入により、エリアを限定して少しずつ棚卸を進める循環棚卸も可能になった。棚卸中のエリアのみ製造を止め、他エリアは稼働し続けられるため、平日のうちから棚卸を進められるようになった。これにより製造現場への負荷も大きく改善された。
お客様の声
小さくスタートすることで、成功体験を着実に積み上げられた
もともと紙管理のみだった当社の現場も、お陰さまでシステム化が進んできています。一部の工場では「スマートFがない現場は考えられない」という声もあります。
当社には4つの国内工場があり、そのうちの1つの上野工場からスマートFの導入を始めました。まずは1拠点から小さくスタートし、徐々に横展開できたのが、結果的によかったと思っています。
初めにスマートFを導入した上野工場でも、まずは少人数からシステム活用を始めました。システムというものに不慣れな者が多い中、ネクスタ様にも都度相談しながら少しずつ運用に慣れていき、上野工場を当社の成功事例にすることができました。このお陰で、他の工場への横展開をよりスムーズにできたと感じています。実際に他工場でスマートFを導入する際は、他工場の担当者が上野工場に来て、スマートFやハンディーターミナルの操作を学ぶ機会も作っていました。
さらに、スマートF導入当初に新工場が竣工したことも、他工場への横展開を後押ししたように思います。新工場を立ち上げる際、他工場からも従業員が集まり、スマートFの効果を実感したあと元の工場に戻りました。彼らが新工場でスマートFの導入を経験したことで、元の工場でも推進しやすくなりました。
初めのうちは、現場担当者に「業務量が増えるのではないか」という不安もあったと聞いています。現在の業務フローに、さらにハンディーターミナルを使うことで、仕事が増えるのではないかと。この現場担当者への理解促進という面でも、まずは小さく導入して、少しずつ慣れていけたのが良かったと思います。
また、今のシステム運用が実現できているのは、ネクスタ様の手厚いご支援のおかげでもあります。他のベンダー様とやりとりをする機会もありますが、そのなかで比較しても、ネクスタ様はフットワークが軽いと感じています。スマートF導入前は、遠方にも関わらず各工場の現場を見ていただき、当社の運用に合わせた設定や使い方を提案してもらえました。導入後も、何か困った時に問い合わせると、すばやく対応してくださっています。現場が着実にスマートFに慣れていけたのは、これらのサポートのお陰でもあります。今後も引き続き宜しくお願い致します。
開発中の機能もたくさんあるとお伺いしているので、さらにスマートFが便利になっていくことを楽しみにしています。
株式会社ネクスタ:導入支援担当の声
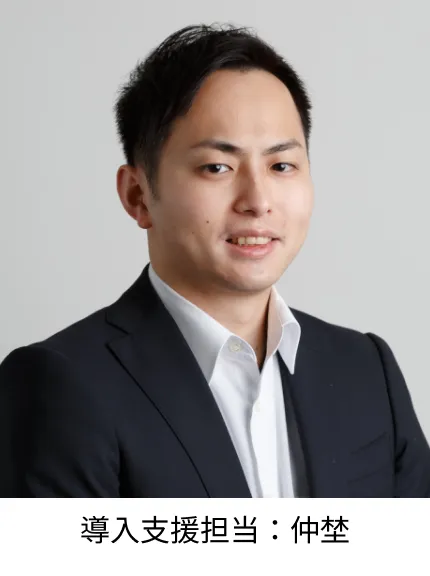
【運用提案する上で心掛けたこと】
お客様の本当に求める機能や運用が何か、ということを強く意識してご提案いたしました。長年培われた現在の運用を変えたくない、という現場の声に対して、なぜそのような運用をしているのか、本当に必要なのか、目的が達成出来れば別の手順でも良いのではないかなど、しっかりと何度もヒアリングをさせて頂き、現場の基本的な流れは変えずに上手くシステムをはめる様に検討に検討を重ねました。
【導入時を振り返って】
本件の導入に際してスマートFの検査モジュールや一括受入、現品発行や誤差判定など、一から構築した機能が多々あり、個人的に一番の思い入れがあります。また、導入当初は既存の運用との並行稼働が必要なため、どうしても対応工数が肥大し、ある製造の原料投入時は1分以内に入れる、といった制限もある中でスマートFの使用が難しいというお声も頂戴しておりましたが、システムの改善と作業者の操作習熟により、運用にのせることが出来ました。